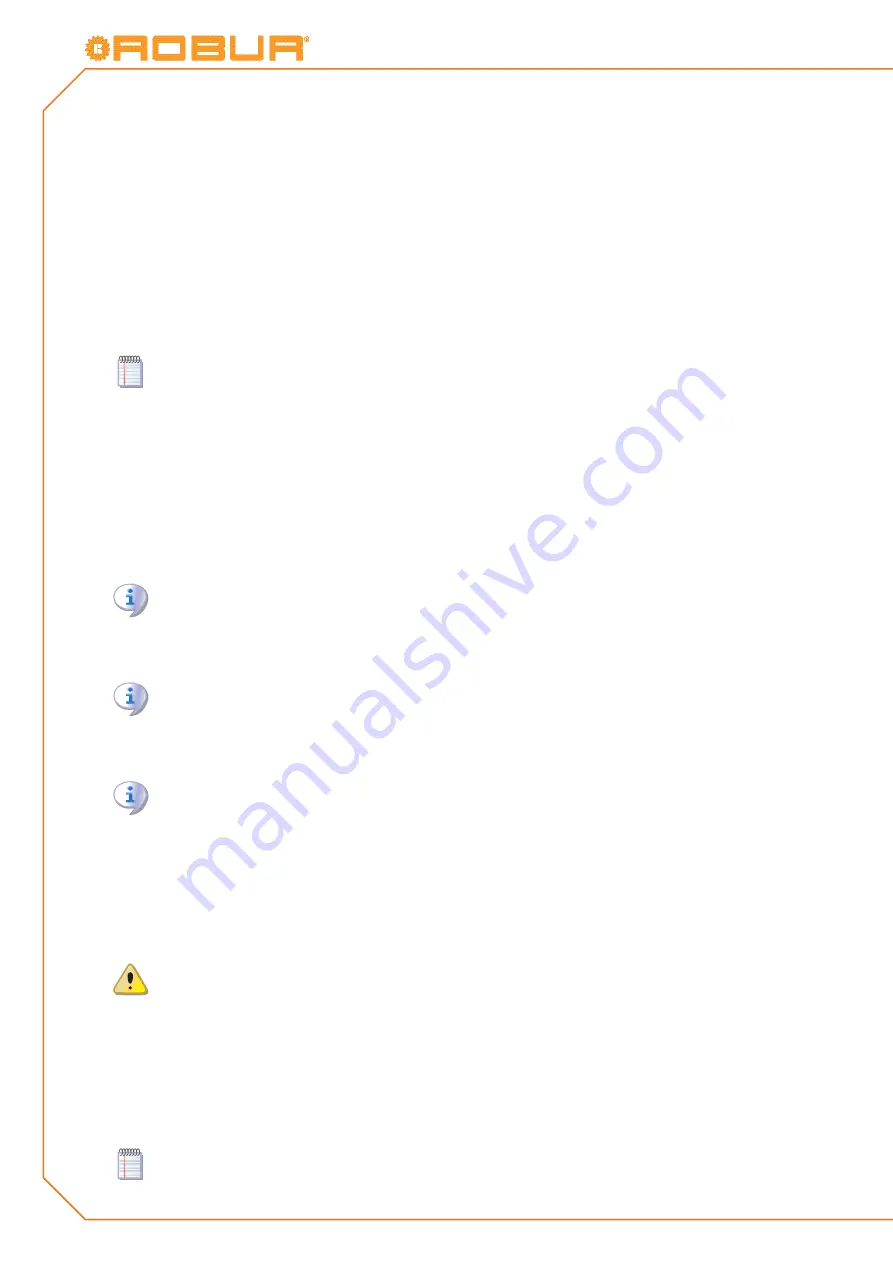
32
FLEXIBLE JOINTS on water and gas connections of the appliance.
•
PRESSURE GAGES on the inlet and outlet water pipes.
•
FLOW REGULATION VALVE on the water inlet pipe (only if the appliance is control-
•
led by a CCP/DDC).
WATER FILTER installed on the water inlet pipe.
•
ISOLATION BALL VALVE on the water and gas pipes of the installation.
•
3 BAR SAFETY VALVE installed on the outlet water pipe.
•
PLANT EXPANSION TANK installed in the appliance outlet water pipe.
•
EXPANSION TANK for the individual appliance, installed on the water outlet pipe
•
(primary side). Provide a plant expansion tank in any case (secondary side), in-
stalled in the water outlet pipe.
The appliance is not equipped with an expansion tank; therefore it is necessary to install
a suitable expansion tank, sized for the maximum temperature range and maximum op-
erating water pressure of the plant.
variable rate WATER CIRCULATION PUMP, FOR PLANT WITH A SINGLE APPLIANCE,
•
located on the water inlet pipe of the appliance, flowing towards the appliance.
variable rate WATER CIRCULATION PUMP, FOR PLANT WITH A SEVERAL APPLIANCES
•
(each appliance have is pump), flowing towards the appliance.
PLANT FILLING SYSTEM: if automatic filling systems are used, a seasonal check of
•
the percentage of monoethylene glycol in the plant is recommended.
For other components to be installed in the system, refer to "Design Manual". For fur-
ther information or technical support in this regard, contact Robur S.p.A.'s Presales Office
(tel.+39 035.888.111) or visite site www.robur.it.
The operations necessary for the First Activation or Regulation of the appliance must be
carried out exclusively by an authorised Robur Technical Assistance Centre (TAC). These
operations are described in Section 7 INITIAL ACTIVATION AND MAINTENANCE
→
69.
The products' guarantee is void if initial activation is not carried out by a Robur TAC.
5�4
GAs sUPPLY
The installation of gas supply pipes must be compliant with current regulations and
norms.
The gas supply pressure must be in the range given in Table 5.2 Network gas
pressure
→
33.
Supplying gas to the appliance at pressures higher than those indicated above can dam-
age the gas valve, resulting in dangerous situations.
LPG systems must be equipped with a first stage pressure reducer close to the LPG stor-
age tank, in order to reduce the gas pressure to 1,5 bar, and a second stage pressure
reducer, close to the unit, in order to reduce pression from 1,5 bar to the value in agree-
ment with the gas network pressure of the country of installation (see Table 5.2 Network
gas pressure
→
33).
Exemple for the Italian market: for the G30 gas, from 1,5 bar to 0,030 bar (30mbar); for the
G31 gas, from 1,5 bar to 0,037 bar (37mbar).