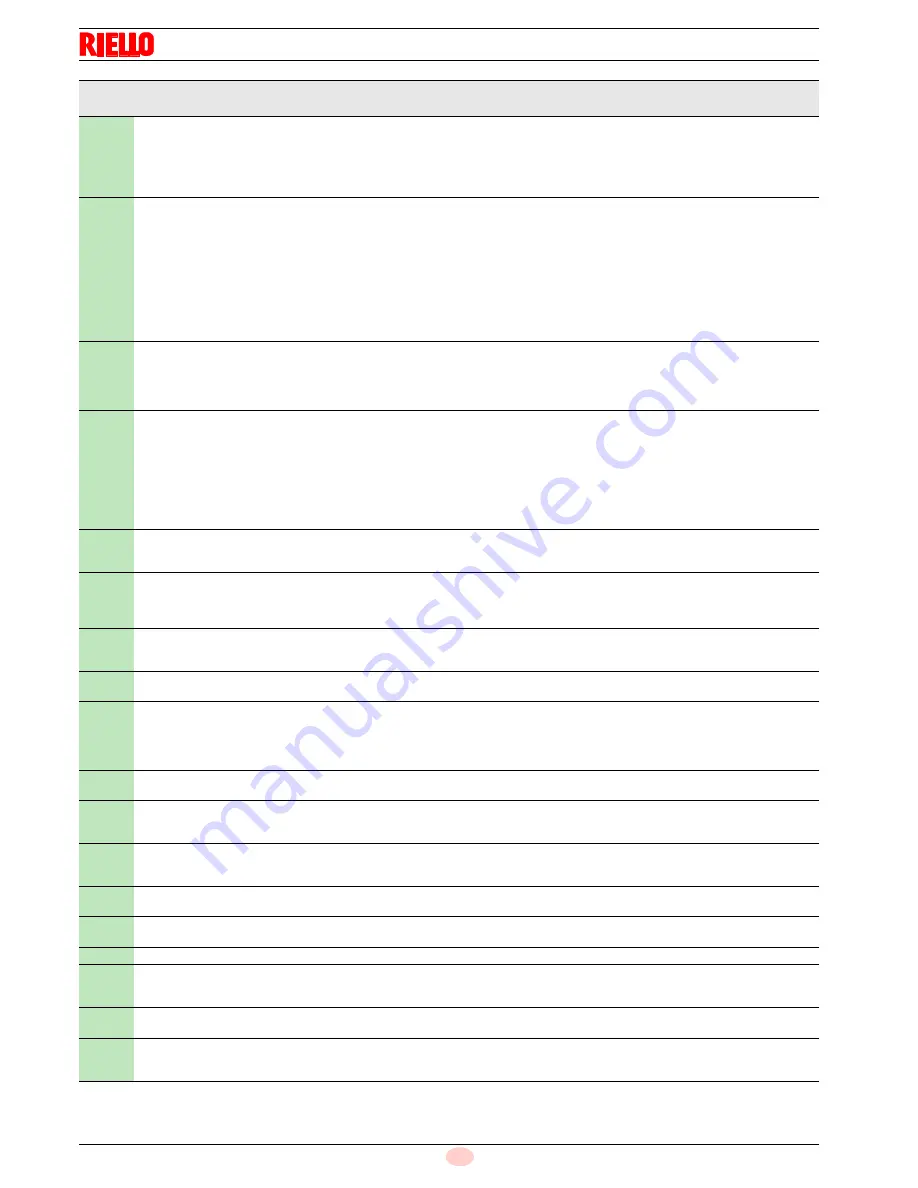
20081753
58
GB
Faults - Possible causes - Solutions
3
Speed sensor circuit open
The standard unit does not receive pulses from the speed
sensor:
1. The motor does not turn.
2. The speed sensor is not connected.
3. The speed sensor is not activated by the sensor disc (check
the distance).
4
Variation in speed / VSD acceleration time too long / speed
below the minimum limit for standardisation
The motor has not reached a stable speed after acceleration.
1. The VSD train times are not shorter than those of the
standard unit (parameters 522, 523).
2. The VSD characteristic is not linear. The VSD voltage input
configuration must correspond with that of the standard unit
(parameter 645).
3. The VSD does not follow the changes of the standard unit
quickly enough. Check the VSD settings (input filter, slide
compensation, different latent speeds).
4. The VSD speed is below the minimum for standardisation
(650 rpm).
5
Incorrect rotation direction
The motor rotation direction is incorrect.
1. The motor does not rotate in the correct direction ---> modify
the parameterisation of the rotation direction, or invert 2 phases.
2. The sensor disc is incorrectly assembled ---> turn the sensor
disc.
6
Implausible speed sensor signals
The required pulse pattern (60°, 120°, 180°) has not been
correctly identified.
1. The speed sensor does not detect all the noses of the sensor
disc ---> check the distance.
2. When the motor turns, other metal parts are detected along
with the noses.
---> improve the assembly.
3. Electromagnetic interference on the sensor lines ---> check
the cable path, improve the EMC.
7
Standardised speed not valid
The standardised speed measured is not within the allowed
range.
1. The motor turns too slowly or too quickly.
15
Speed deviation µC1 + µC2
Microcomputer speeds 1 and 2 have an excessive deviation.
This may be caused by incorrect standardised speeds (e.g.
after the reintegration of a set of data in a new unit)
---> repeat the standardisation and check the air/fuel ratio.
20
Incorrect phase of the phase controller
The standardisation was performed in the wrong phase.
The only phases allowed are
≤
12 ---> controller OFF, restart
the standardisation.
21
Safety loop/burner flange open
The safety loop or burner flange is open ---> repeat the
standardisation with the safety loop closed.
22
Pneumatic actuator without reference
The air actuator has no reference, or has lost it.
1. Check whether the reference position can be approached.
2. Check whether the actuators have been swapped over.
3. If the error only arises after the start of standardisation, the
actuator may be overloaded and unable to reach its destination.
23
VSD deactivated
The standardisation was started with the VSD deactivated --->
activate the VSD and repeat the standardisation.
24
No valid operation mode
The standardisation was started without a valid operation mode
---> activate a valid operation mode and repeat the
standardisation.
25
Pneumatic control of the air/fuel ratio
The standardisation was started with a pneumatic control of the
air/fuel ratio ---> it is not possible to carry out the standardisation
with a pneumatic control of the air/fuel ratio.
128
Run command without prior standardisation
The VSD is controlled but not standardised ---> perform the
standardisation.
255
No standardised speed available
The motor turns but is not standardised ---> perform the
standardisation.
83
#
VSD speed error
The required speed has not been reached.
Bit 0
Valence 1
Lower control range limit
The speed was not reached because the control range limit was
activated.
---> for the measurements, see error code 80.
Bit 1
Valence 2...3
Greater control range limit
The speed was not reached because the control range limit was
activated ---> for the measurements, see error code 80.
Bit 2
Valence 4...7
Stop caused by electromagnetic interference
The speed has not been reached because there are too many
electromagnetic interferences on the sensor line. For the
measurements, see error code 81.
Error
code
Diagnostic code
Meaning of the REC 37.400A2 system
Recommended measures
Содержание RS 310/EV BLU FS1
Страница 2: ...Translation of the original instructions...
Страница 79: ......