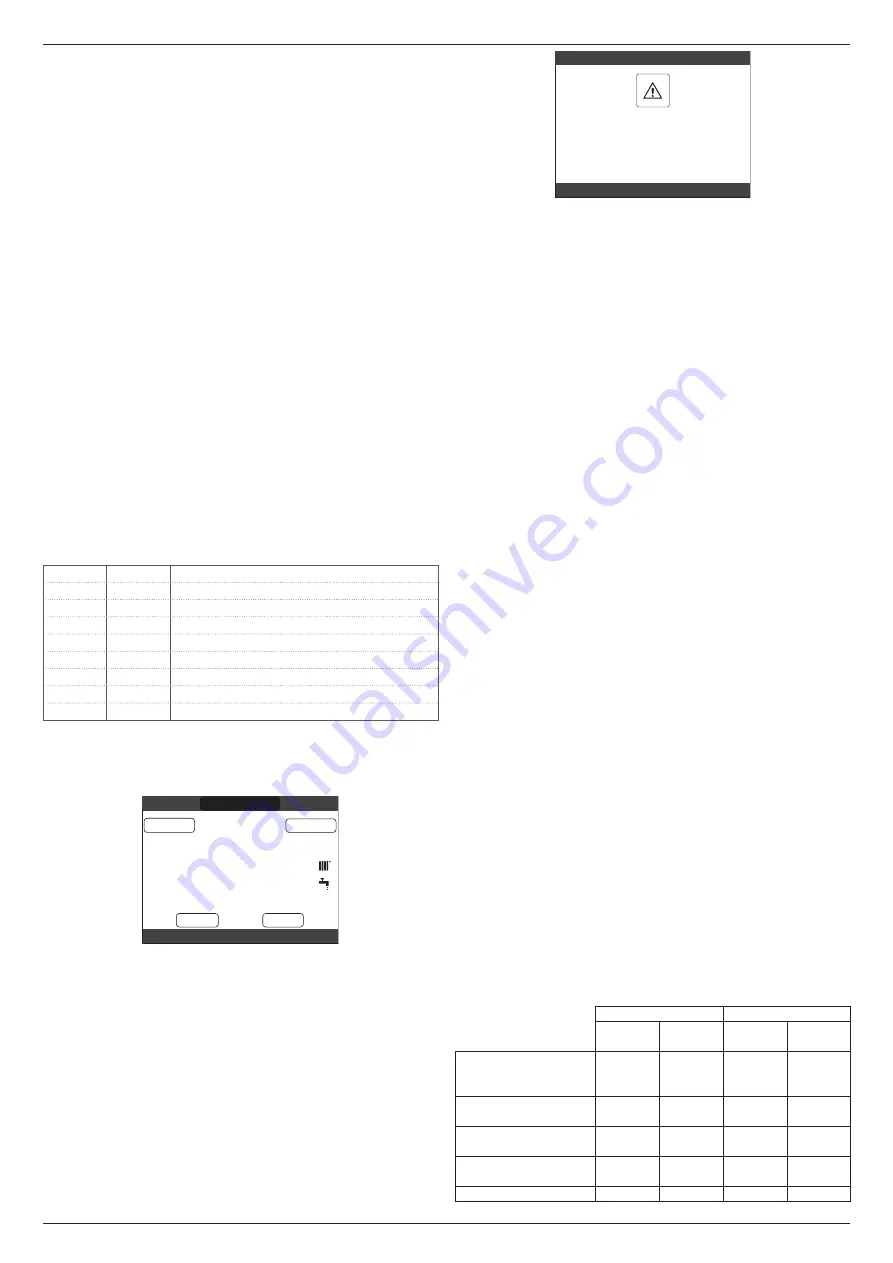
FAMILY
6
3.9
Positioning the wall-mounted boiler and hydraulic
connections (Fig. 10)
The boiler comes as standard with a boiler support plate. The position and dimension of
hydraulic fittings are shown in the detail drawing.
For the assembly, proceed as follows:
-
fasten the boiler support plate (F) to the wall and use a spirit level to make sure it is
perfectly horizontal
-
mark the 4 holes (ø 6 mm) envisaged for securing the boiler support plate (F)
-
make sure that all measurements are exact, then drill the wall using drill tips with the
diameters indicated above
-
fix the plate with the built-in template (G) to the wall.
-
fix the safety valve pipe supplied in the documentation envelope onto the coupling of the
safety valve (S), then connect it to an adequate discharge system.
Make the hydraulic connections.
M
heating delivery
3/4” M
RB
storage cylinder return line
3/4” M
G
gas
3/4”
M
R
heating return
3/4” M
MB
storage cylinder delivery
3/4” M
3.10 Electrical wiring (Fig. 11a-11b-11c)
Low voltage connections
Carry out the low voltage connections as follows:
-
use the external cable box supplied as standard
-
unscrew the fixing screws of the cover (V)
-
carry out the connections as shown in the detailed drawing (Fig. 11a-11b)
b
We recommend using conductors with a section no larger than 0.5 mm
2
.
b
In the event of TA or TBT connection, remove the relative jumpers on the
terminal board (Fig. 11c).
-
Close the box with the screws (V) that were removed beforehand.
-
Press the two tabs on the sides of the box to position it correctly in the seat on the boiler
(bottom left on the inside) sliding it towards the top inside the relative slide bars.
-
Tighten the safety screw (V1).
b
If the low voltage electrical connection box is not connected the boiler does
not ignite.
1-2-3-4
(- A B +)
Bus 485
5 - 6
TA
Room thermostat (contact without voltage)
7 - 8
TBOL
Storage cylinder thermostat
9-10
TBT
Low temperature limit thermostat
11 - 12
SE
Outdoor temperature sensor
13 - 14
OT+
Open therm
15 - 16
SBOL
Storage tank probe
17 - 18
X1
Not used
19 - 20
X2
Not used
OTBus remote control connection
When an OTBus remote control is connected to the system, the boiler display shows the
message “Open Therm Connected”, while some of its functions are disabled and transferred
to the OTBus remote control that takes control of the domestic hot water and heating
functions regarding the main zone.
42
°C
MENU
STATE
SET
INFO
OPENTHERM CONNECTED
PLANT
HOT WATER TEMPERATURE
FRI
1.5
bar
18/05/2013
12:17
In particular on the boiler display:
-
it is no longer possible to set the boiler OFF/WINTER/SUMMER status (it is set by the
OTBus remote control)
- it is no longer possible to set the domestic hot water setpoint (it is set by the OTBus
remote control)
-
it is not possible to activate the CHIMNEY SWEEPER function if a OTBus
remote control
is connected to the boiler
In addition:
-
The domestic hot water setpoint is displayed in the INFO menu in the place of the flow
meter flow rate value
- The heating setpoint set on the boiler display is used only if there are heat requests from
the TA and the OTBus remote control does not have a request if the parameter DO_AUX1
= 1 or DO_AUX1 = 0 and the jumper on 1-2 pin of X21 is closed.
-
We should point out that it is not possible, with the OTBus remote control connected, to
change the values of the parameters ACTUATION TYPE and REQUEST TYPE of the
main zone.
Note: an OTBus remote control cannot be connected if the system already has a
REC10H or BE16 interface boards. in this case the system gives the following error
message:
WRONG CONFIGURATION
OPENTHERM CONNECTED
High voltage connections
The connection to the mains supply must be made via a separation device with an omnipolar
opening of at least 3.5 mm (EN 60335/1 - category 3). The appliance works with alternating
current at 230 Volt/50 Hz, and is in compliance with standard EN 60335-1. It is obligatory to
make the connection with a safe ground/earth, in compliance with current directives.
b
The installer is responsible for ensuring the appliance is suitably earthed; the
manufacturer will not be liable for any damage resulting from an incorrect or absent
earth connection.
b
It is also advisable to respect the phase-neutral connection (L-N).
b
The earth conductor must be a couple of cm longer than the others.
b
To create the seal of the boiler use a clamp and tighten it on the cable grommet
used.
The boiler can operate with a phase-neutral or phase-phase (not floating) power supply.
It is forbidden to use gas and/or water pipes to earth electrical appliances. Use the power
cable supplied to connect the boiler to the mains power supply. If the power cable has to be
replaced, use a HAR H05V2V2-F, 3 x 0.75mm² cable, Ø max external 7 mm.
3.11 Gas connection
The connection of the gas supply must be carried out in compliance with current installation
standards. Before carrying out the connection, check that the type of gas is that for which
the appliance is set up.
3.12 Removing the casing (Fig. 12)
To access the components inside, remove the casing as indicated below:
-
find and unscrew the 2 screws (A) fixing the casing to the boiler levering the two fixing
clips (C), detach the bottom part of the casing
-
lift the casing upwards to release it from the top tabs (B), then remove it.
WARNING
b
If removing the side panels, put them back in their initial position, referring to the
adhesive labels on their walls.
b
If the front panel is damaged it must be replaced.
b
The noise absorbing panels inside the front and side walls ensure the airtight seal for the
air supply duct in the installation environment.
b
It is therefore CRUCIAL after the dismantling operations to correctly reposition the
components to ensure the boiler's seal is effective.
3.13 Flue gas exhaust and combustion air suction (Fig. 13)
To evacuate the combustion products, refer to UNI 7129-7131. Always comply with
local standards of the Fire Department, the Gas Company and with possible municipal
dispositions.
The evacuation of the combustion products is carried out by a centrifugal fan and the control
board constantly monitors that it is operating correctly.
It is essential for the evacuation of the flue gases and the adduction of the boiler's combustion
air that only original pipes be used (except C6) and that the connection is made correctly as
shown in the instructions provided with the flue gases accessories.
A single flue can be connected to several appliances provided that every appliance is the
condensing type.
The boiler is a C-type appliance (with airtight chamber), and must therefore have a safe
connection to the flue gas discharge pipe and to the combustion air suction pipe; these both
carry their contents outside, and are essential for the operation of the appliance.
Both concentric and twin terminals are available.
Suction/discharge pipes length table
Maximum straight length
Pressure drop
25
IS
35
IS
Bend
45°
Bend
90°
Flue gases pipe Ø 80 mm
("forced open” installation)
(type B23P-B53P)
110 m
65m
1 m
1.5 m
Concentric pipe
Ø 60-100 mm (horizontal)
10 m
6 m
1.3m
1.6m
Concentric pipe Ø 60-100 mm
(vertical)
11 m
7 m
1.3m
1.6m
Concentric pipe
Ø 80-125 mm
25 m
15 m
1 m
1.5 m
Twin pipe Ø 80 mm
60+60 m
35+35 m
1 m
1.5 m