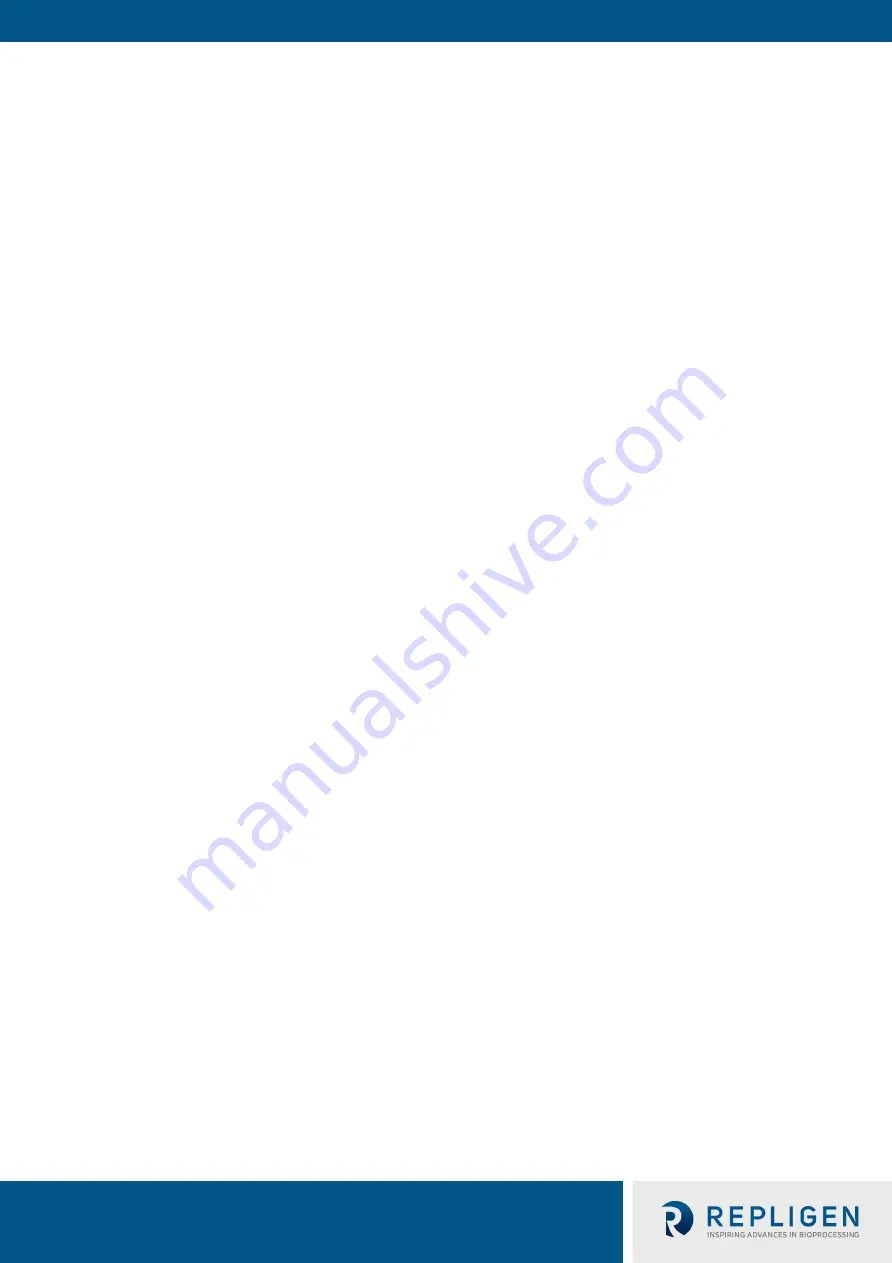
XCell™ C410:V3 Controller
User Guide
48 repligen.com UG-C410v3-06
14.
Rapidly close the Steam inlet valve and immediately open the main valve into the filtration
assembly to minimize a pressure drop in the connection.
Note:
that following SIP of the connection, the cool-down of the connection post SIP will generate a
vacuum within the connection, which must be minimized.
7.
Maintenance
7.1
Diaphragm
It is recommended that a new diaphragm be used with each new run. To avoid premature failure, it
is important to ensure that the diaphragm is seated in the proper orientation.
Use with aqueous liquids only. For use with other fluids contact
Repligen
.
7.2
Pump air inlet filter
The replacement of the pump air inlet filter will be determined by how the system is configured. If
the air filter is autoclaved with the filtration assembly, it is qualified for 135° C, for 30 minutes, 3
times.
7.3
“O” Rings, gaskets and quick connects
The O-rings on the ventilation ports and quick connects (XCell ATF® 4 Device and XCell ATF® 6
Device) should be replaced every two or three runs. Replacement kits are available from Repligen.
HFM Filter “O” rings should be replaced with each new filter. For pump line, air supply, and vacuum
source, all “O” rings and gaskets should be replaced periodically. An approved lubricant may be used
to facilitate coupling of parts containing an “O” ring seal.
7.4
Controller maintenance
7.4.1
Bi-annual maintenance
1.
P2 verification or calibration.
2.
Complete system visual inspection for damage or risk to the operator or surrounding
personnel.
3.
P-box vacuum system leak test.
4.
Verification that the pressure regulator is set to correct pressure.
5.
Inspection of air and vacuum connection to the P-box.
6.
Inspection of pneumatic fittings.
7.
Inspection of the pneumatic tube from the P-box to the XCell ATF® Device pump housing.
8.
Inspection of enclosure for damage, locks and hinge performance, external electrical
connection, cables, and pneumatic tubing.
9.
PRV verification or calibration.
10.
PRV trend verification or calibration.
11.
PV verification or adjustment.
12.
Inspection that all components inside the enclosures are secured and intact.
13.
P2 verification or calibration.
14.
Inspection of touch screen alignment and performance.
15.
Flow test (low, middle, and high flow rate).