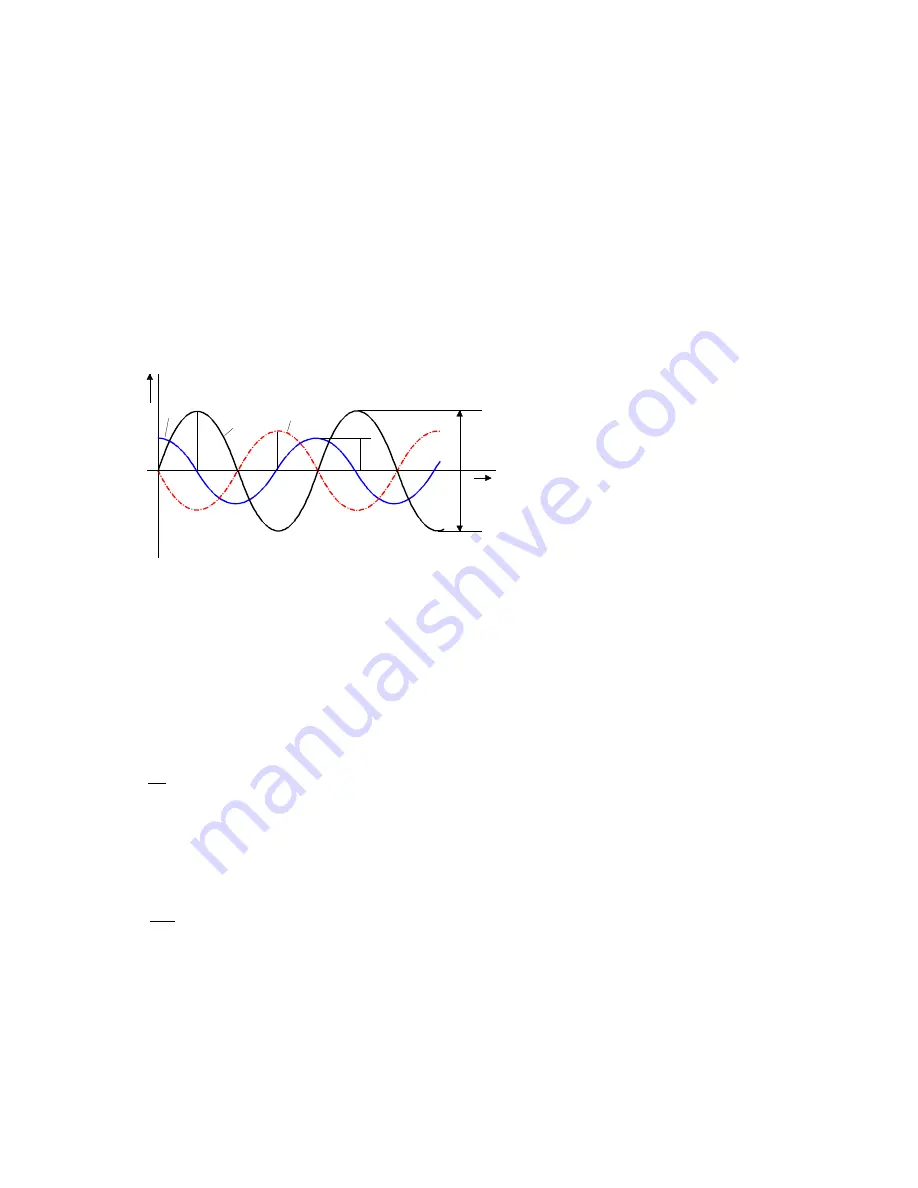
2.0 Background to feed engineering
The use of mechanical vibrators for feeding material, dosing, screening or mixing of goods is long estab-
lished. Drives, with so called out-of-balance motors and vibrating equipment with electromagnetic drives are
certainly the most widely applied. Electromagnetic drives are more frequently used in automation engineer-
ing and hence some fundamental differences require further explanation. In general one is referring here to
vibratory feeders.
Vibratory feeders comprise the actual drive unit, including one or more coils, a reaction base, a spring sys-
tem and tooling, which can be in the form of a tray, tube, track or a bowl with a spiral track inside. Tray
shaped vibratory feeders that deflect in one direction, are used to convey material and are generally referred
to as “Linear Feeders“. Vibratory feeders with a spiral track and a spring/coil combination that gives a com-
posite motion that are used for sorting, orientating and feeding parts, are known as “Bowl Feeders“.
2.1 The vibration wave form
The vibratory motion in the case of a vibratory feeder moves backwards and forwards in a straight line. The
direction of movement is at a specific angle relative to horizontal, referred to as the “vibrating angle“. The
movement plotted against a time axis gives a curve approaching the shape of a sine wave.
s
Deflection
a
Acceleration
v
Speed
Diagram 1 The vibration curve
The sinusoidal waveform is derived from the formula
[mm]
where “s“ is the time based vibration movement, s
0
the amplitude (half of the total deflection) and
ω
the cycle
frequency (2
π
f ).
The vibrating speed is derived from the differential of deflection over time
with
the acceleration
with
2
t
s
s
ω
sin
0
=
t
s
dt
ds
v
ω
ω
cos
0
=
=
ω
0
0
s
v
=
t
s
dt
ds
a
ω
ω
sin
2
0
2
2
−
=
=
2
0
0
ω
s
a
=
S
a
v
S,a,v
Sn
t
a
0
s
0
v
0