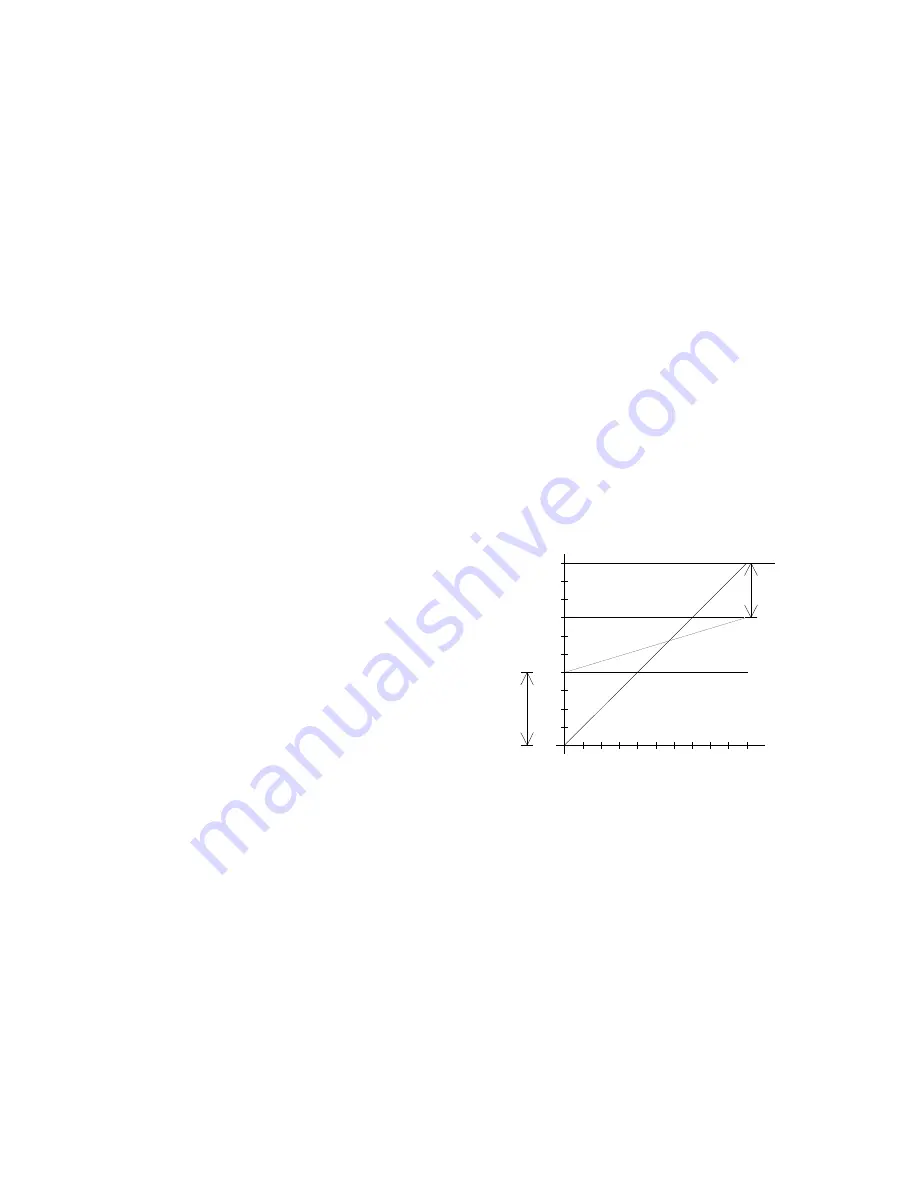
For 100Hz (120Hz) vibrating frequency, this switch must be closed or a link fitted and for 50Hz (60Hz) vi-
brating frequency the switch must be open, or a link is removed.
In the case of
frequency inverters
the vibrating frequency has a step less setting through the operator front
panel.
Coils can be damaged if the vibrating frequency is set incorrectly (too low).
The rating label on a coil is often not very explicit, e.g. 50Hz is stated but no reference is made to whether
this is mains frequency or the vibrating frequency of the feeder (generally it refers to the electrical fre-
quency). It is important (in the case of thyristor and triac controllers) to know if the coil operates with one or
both of the mains half-waves (6000 or 3000vibs/min).
Coils for 50Hz (3000 vibs/min) are often designated with the additional wording “for rectifier opera-
tion”.
A coil for 6000 vibs/min installed to operate on half-wave (3000 vibs/min) will draw too high a current and will
inevitably overheat, leading to breakdown. The frequency adjustment range, on frequency controllers, is very
wide and so it is particularly important to monitor the coil current.
When in doubt the current must be checked
.
8.2 Setting the feeder throughput
Different feeder constructions (size, weight, damping etc.) means that the set-point control range, i.e. they
has to be trimmed for each individual feeder. In other words, the output voltage value at which material just
moves and also which gives maximum deflection, differs from feeder to feeder. The trimmers Umin and
Umax are used for setting the control range, so that it can be fully used, whether this be for control from a set
point potentiometer, 0...10V control voltage or 0(4)...20mA current signal.
Controllers with digital control panels, because of their
improved setting abilities, do not require this facility. It is only
necessary to limit the maximum feeder throughput, to either
protect the coil against hammering or to limit a feeder that is
too quick (jamming or interlocking parts).
When an external, analogue, set-point signal is used in
conjunction with a digital controller, it is still necessary to
adjust the minimum value.
In this case the setting is as follows:
1. Increase the throughput setting to the level where the
feeder does not quite feed.
2. Now go into the user menu and select the external set
point source. The value set previously will remain as the
minimum level when the throughput signal is “0”.
9.0 Setting up regulation control of frequency controllers
•
To use regulation mode it is necessary to fit an accelerometer to the vibratory feeder.
•
When an accelerometer is used in regulation mode, it will sense and feed back
all
vibration signals.
Stray signals can be generated by neighbouring equipment, inadequate supporting structures for the
feed equipment or from inadequate mounting of the sensor itself. These can cause incorrect regulation.
It is especially important to ensure that there are no external influences on the feeder, when an
automatic frequency search is being carried out.
•
Resonant frequency:
Depending on the construction of the feeder and mass distribution, it is possible
to have several frequencies that will exhibit resonance. The additional resonance points are multiples of
the main resonant frequency. In certain, critical, circumstances the automatic frequency search may not
locate resonance for this reason and in such cases the frequency must be set manually.
15
0
10 20 30 40 50 60 70 80 90 100 [%]
10
20
30
40
50
60
70
80
90
100
[%]
O
utp
ut
v
ol
ta
ge
Set point
Um
in
Um
a
x
F
ul
l
sc
al
e