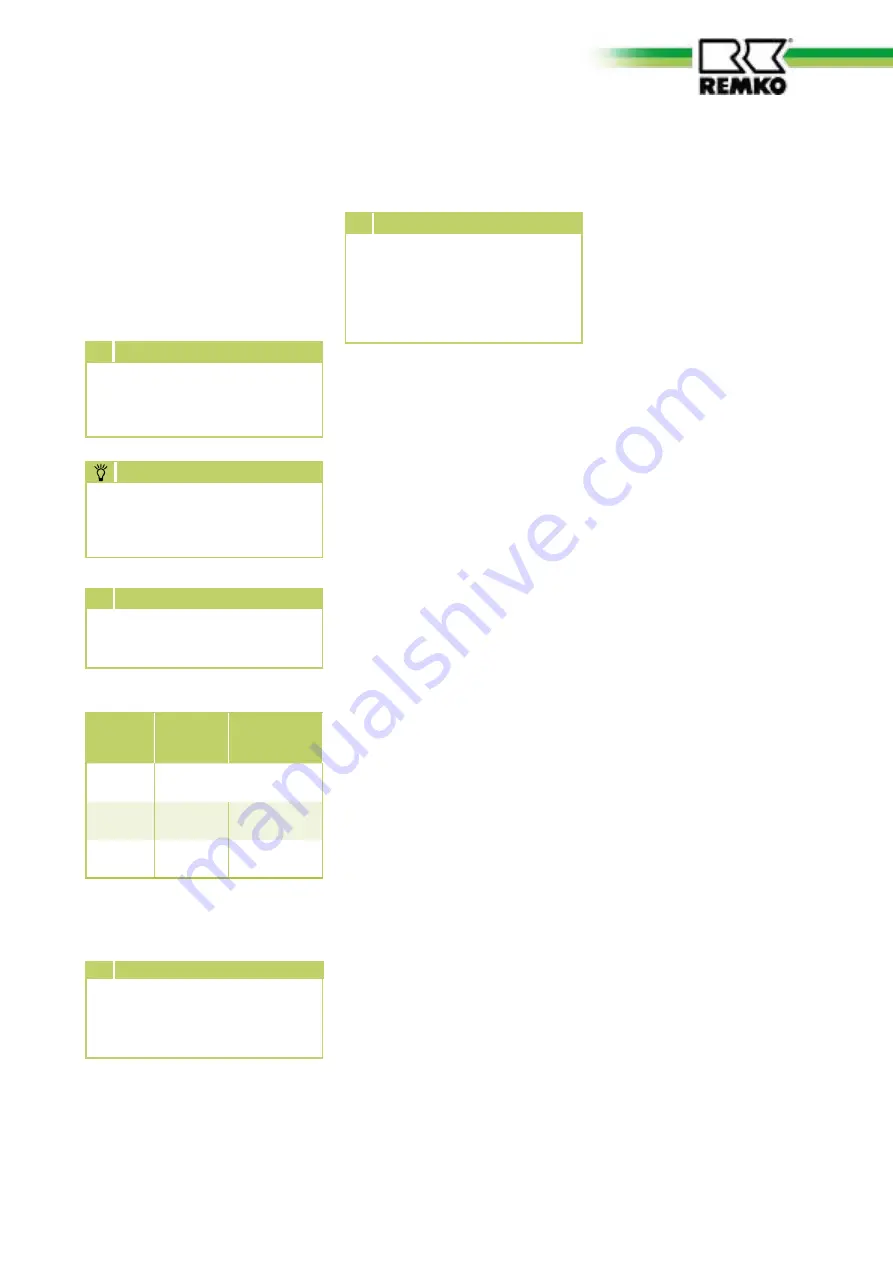
Add refrigerant
The equipment contains a basic
quantity of refrigerant. Beyond
these conditions, for refrigerant
pipe lengths of more than 5 meters
per circuit, an additional amount of
refrigerant must be added, accord-
ing to the following chart:
RVD 351DC RVD 521DC
Up to and
incl. 5m
0 g/m
5m to
max. 15m
25
g/m
-
5m to
max. 20m
-
25 g/m
Note that the employed refrig-
erant is always filled in liquid
form!
CAUTION
NOTE
Check the overheating to
determine the refrigerant fill
quantity
Wear protective clothing when
handling refrigerant.
CAUTION
Commissioning
Commissioning should only be
performed and documented by
specially trained personnel.
NOTE
The system can be commissioned
once all the components have
been connected and tested. A
functional check should be per-
formed to verify its correct func-
tion and identify any unusual
Function test and
test run
Check the following points:
■
Leak tightness of refrigerant
pipes.
■
Compressor and fan running
smoothly.
■
In cooling mode, cold air should
be output by the indoor unit,
and warm air should be output
by the outdoor component.
■
Functional test of the indoor
unit and all program
sequences.
■
Check of the surface tempera-
ture of the suction pipe and
determination of vaporiser
overheating. To measure the
temperature, hold the ther-
mometer to the suction pipe
and subtract the boiling point
temperature reading on the
pressure gauge from the meas-
ured temperature.
■
Record the measured tem-
peratures in the commissioning
report.
Check that the stop valves and
valve caps are tight after carrying
out any work on the refrigerant
circuit. If necessary, use appropri-
ate sealant products.
NOTE
Functional test for cooling
and heating modes
1. Remove the caps
from the valves.
2. Begin the commissioning
process by briefly opening the
blocking valves of the external
section until the manometer
displays a pressure of approx. 2
bar.
operational behaviour prior to
handing it over to the operator.
3. Use leak detection spray or suit-
able devices to check that all
the connections are tight.
4. If no leaks are found, fully open
the stop valves by turning them
anti-clockwise using a spanner.
If leaks are found, repair the
faulty connection. It is impera-
tive that the vacuum creation
and drying steps are repeated.
5. Switch off the main circuit
breaker or remove the fuse
(provided by the customer).
6 Press the test knob on the
outdoor unit and wait until
a frequency of min. 50 Hz is
established (only RVD521).
6. Use the remote control to
switch on the unit and select
the cooling mode, maximum
fan speed and lowest target
temperature.
7. Check the overheating, out-
door, indoor, outlet and vapori-
sation temperatures and record
the measured values in the
commissioning report. Check
the correct function and set-
tings of all regulation, control
and safety devices.
8. Check the indoor unit control
system using the functions
described in the chapter "Oper-
ation". Timer, temperature set-
ting, fan speeds and switching
to ventilation or dehumidifying
mode.
9. Check the correct function
of the condensation pipe by
pouring distilled water into the
condensation tray.
A bottle with a spout is recom-
mended for pouring the water
into the condensation tray.
10. Switch the indoor unit to heat-
ing mode.
23
Содержание RVD 351DC
Страница 2: ......
Страница 31: ...Notes 31...