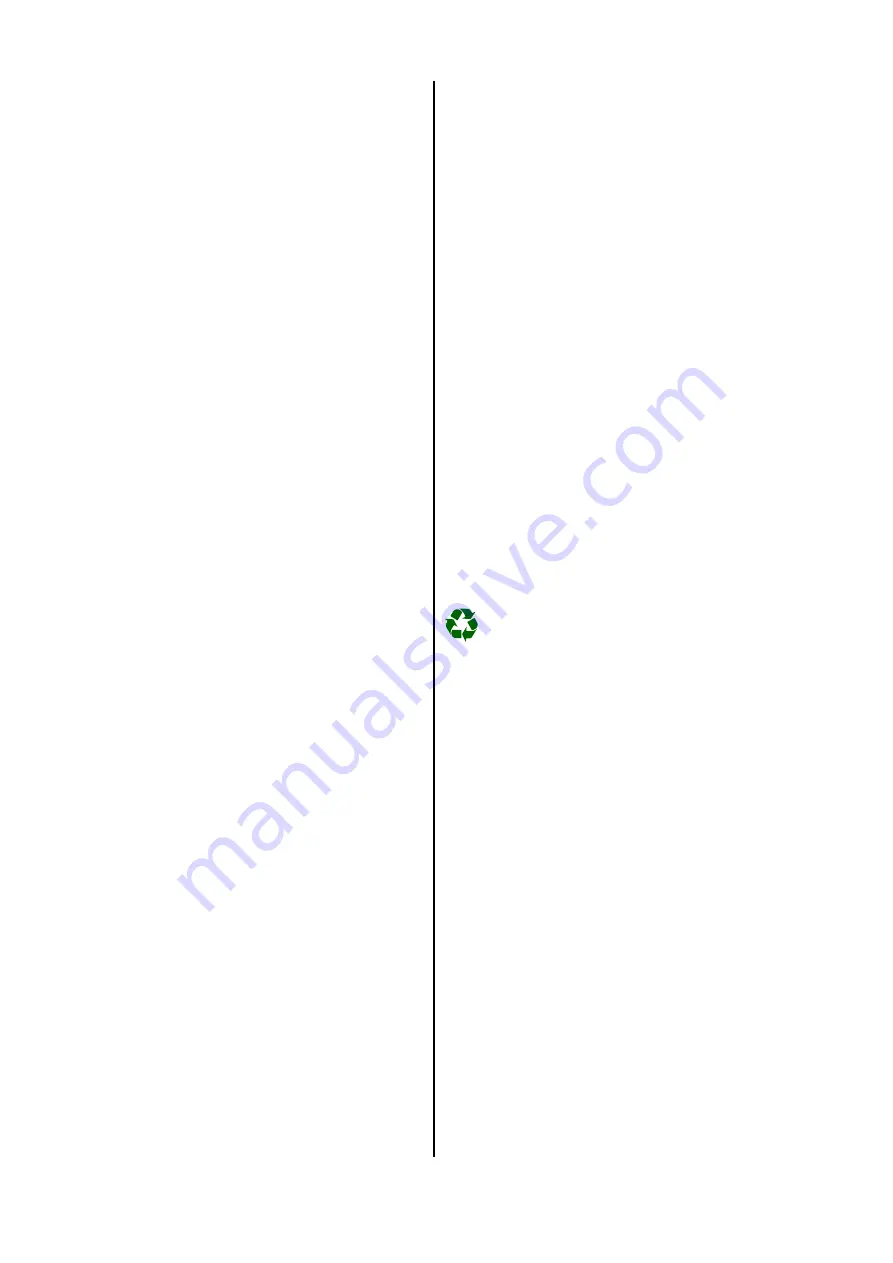
26
Operation
The unit must be put into operation by the manufacturer
or one of his appointed representatives. All regulation,
control and safety mechanisms must be checked to en-
sure that they are working properly and have the correct
settings.
Follow the instructions below to put the unit into opera-
tion:
1. Remove the housing cover.
2. Make sure that the shafts in the circulation pumps
can turn freely. To do this, remove the plug
(depending on the pump type) and turn the shaft or
remove the housing cover by taking off the four
screws and then rotate the shaft.
3. Make sure that there is no dirt.
4. Reassemble the pump in the opposite order and se-
lect the highest performance level for multi-phase
circulation pumps.
5. Make sure that the shut-off valves of the hydraulic
lines are open and set the pipe regulating valves to
the corresponding flow rate.
6. Make sure that all pipes and valves in the system
have been insulated correctly.
7. Fill the system with water or a pre-mixed water-glycol
mixture.
8. Ventilate the entire system and the pump.
9. Make sure that there is no air in the differential pres-
sure monitor line. If there is, ventilate it at the con-
nection.
10.Check the entire system for leaks.
11.Check the insulation of all components.
12.Check that the operating current is consistent with
the power current.
13.Before switching the unit on, make sure that the
power input and the condenser (s) have the correct
rotational field. If an incorrect rotational field has
been connected, the integrated phase-sequence re-
lay interrupts the supplied current of the regulation.
14.Switch the chiller on by pressing ON / OFF / RESET
and select the cooling operating mode via MODE. If
the drainage temperature is warmer than the factory
setting of 12 °C, the COMP. display blinks and the
condenser begins to run in approx. three to five min-
utes.
15.If the factory setting has been changed, set the de-
sired drainage temperature by setting the Parame-
ter -02 to the target value, exit the parameter level
and press the ON / OFF / RESET button twice.
16.If the drainage target temperature falls below 8 °C in
the parameter level, both displays begin blinking.
You must then select a higher drainage temperature.
17.The supply temperature is approx. 5 Kelvin under the
drainage temperature for the rated flow rate.
18.If the supply temperature is below the factory setting
of 4°C, the unit registers a malfunction (E05/E25). In
this case, the drainage temperature must be set
higher. If the difference between the supply and re-
turn temperatures is too high or too low, check the
flow rate.
19.The circulation pump starts and the regulation
checks the volume current via the flow switch
(differential pressure monitor). If the amount of water
is too small, the unit registers a malfunction and the
cold cycle is not released.
20.In this case, the source of the error (pipe regulating
valve not set, all valve assemblies of the inner units
are still closed, pipe dimensions of the system are
not correct) must be identified and fixed.
21.The cold cycle switches on after a time delay of ap-
prox. 3 to 5 minutes.
22.Check the system pressure, system height between
chiller and the highest inner unit and the water vol-
ume and set, if necessary, the filling pressure of the
membrane expansion vessel to the system.
23.Reattach the covers.
24.Train the operator in system operation.
Only authorised personnel may come into contact with
the cold cycle. This ensures that refrigerant does not es-
cape into the environment when the unit is being re-
paired.
Both the refrigerant and the system parts are subject to
special requirements for disposal.
Important information about recycling!
Environment and Recycling
G
The refrigerant in use is a safety refrigerant. This
means that, should damage occur, the quantities
released will not cause injury to the respiratory
systems of people and animals. Do not touch the
liquid refrigerant as it can freeze the skin!
G
Operation/handling which does not comply with
these instructions is prohibited!
In cases of non-compliance, we assume no liability
and the guarantee becomes null and void.
Service and Guarantee
For the guarantee to be valid, the purchaser or his cus-
tomer must completely fill out the "guarantee certificate"
enclosed with all units and send it back to REMKO GmbH
& Co. KG
.
The units are repeatedly tested at the production site to
ensure that they are working properly. If a malfunction
occurs that cannot be eliminated by the operating per-
sonnel, please contact your dealer or contact person.