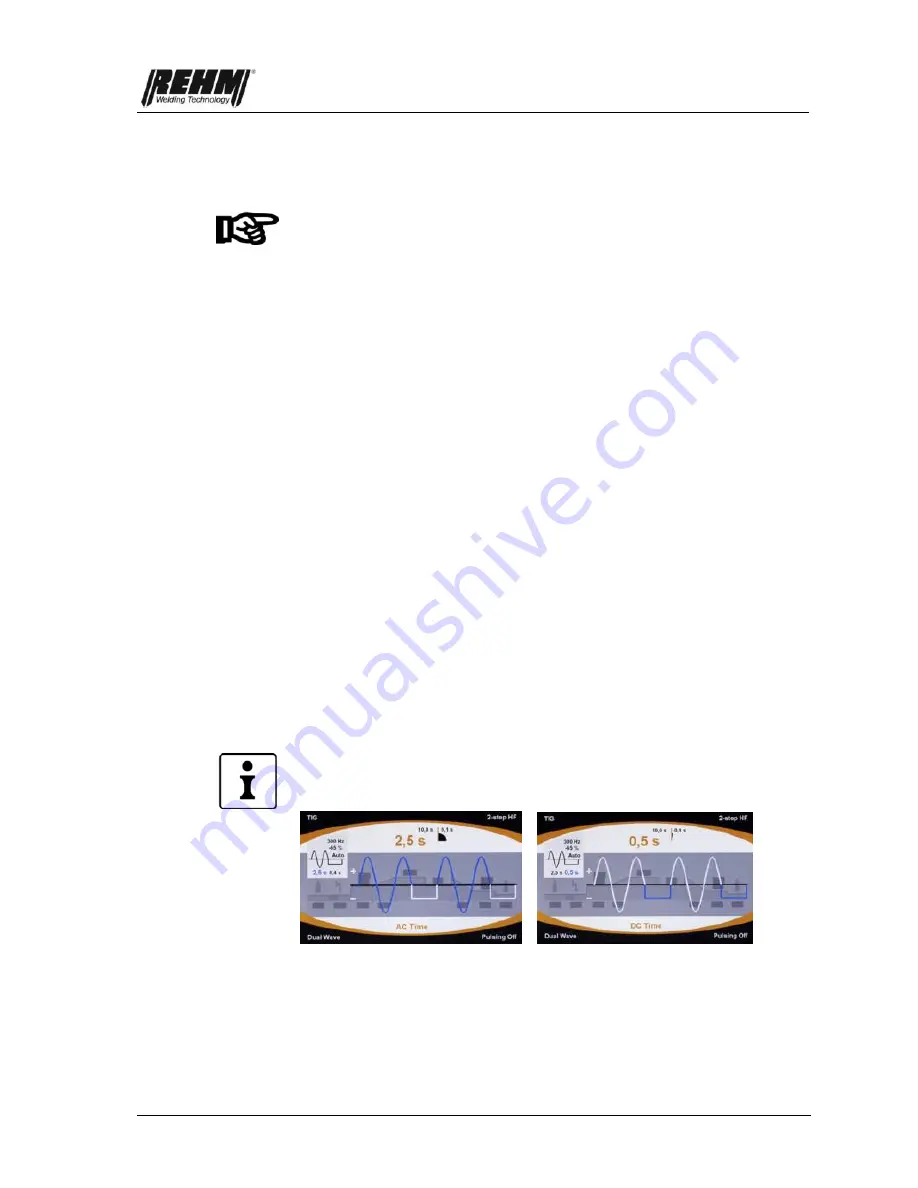
Functional description
30
3.7.2
DC current positive terminal
During TIG welding, TIG spot welding and TIG interval welding with DC current
positive terminal, the positive terminal is applied to the upper output connector
for the TIG torch.
During TIG welding, TIG spot welding and TIG interval welding with DC positive
terminal, the electrode is under extremely high thermal stress which can make
the electrode melt, even with small currents, and can cause damage. Welding
with DC current positive terminal is only possible using a REHM INVERTIG.PRO
digital
AC/DC welding system.
During electrode welding the electrode holder is also connected to the upper
output connector. With the DC current positive terminal setting, the electrode is
welded with positive terminal. Electrode welding with DC current positive terminal
is only possible using a REHM INVERTIG.PRO
digital
AC/DC welding system.
With electrode welding, the polarity for the electrode is selected depending on
the type of electrode that is used (pay attention to electrode manufacturer
information).
3.7.3
DC current negative terminal
During TIG welding and TIG spot welding with DC current negative terminal, the
negative terminal is applied to the upper output connector for the TIG torch.
During TIG welding or TIG spot welding with DC current, welding usually takes
place with this setting.
During electrode welding the electrode holder is also connected to the upper
output connector. The electrode is welded with negative terminal with the DC
current negative terminal setting. During electrode welding with an
INVERTIG.PRO
digital
DC welding system at the positive terminal, the electrode
holder must be plugged into the lower connector, since the polarity is not
selectable. With electrode welding, the polarity for the electrode is selected
depending on the type of electrode that is used (pay attention to electrode
manufacturer information).
3.7.4
Dual Wave
The Dual Wave process from REHM is a combination of AC and DC welding.
The AC and DC times can be adjusted independently of each other The selected
values for welding current I1 and I2, the frequency and the balance are taken
into consideration in the same way as they are in DC-only or AC-only welding.
AC time
DC time
Fig. 18: Individual AC and DC time settings
The Dual Wave process reduces the excess AC part in the arc to the necessary
minimum. The reduced heat introduction that this causes makes it easier to
control the welding bath and produces less pore formation, and is used in difficult
welding situations, when welding workpieces of different thickness and when
processing thin plates made from aluminium and aluminium alloys.
Содержание INVERTIG.PRO digital 240 DC, 240 AC/DC
Страница 1: ...GB OPERATING INSTRUCTIONS TIG inert gas welding units INVERTIG PRO digital 240 450 DC AC DC...
Страница 7: ...Introduction 7 1 2 General description Figure 1 INVERTIG PRO digital...
Страница 75: ...Circuit diagrams 75 9 Circuit diagrams...
Страница 76: ...Circuit diagrams 76...
Страница 77: ...Circuit diagrams 77...
Страница 78: ...Circuit diagrams 78...
Страница 81: ...Components 81 Figure 53 Exploded view of an INVERTIG PRO digital 240 DC 450 AC DC left...
Страница 82: ...Components 82 Figure 54 Exploded view of an INVERTIG PRO digital 240 DC 450 AC DC right...
Страница 87: ......