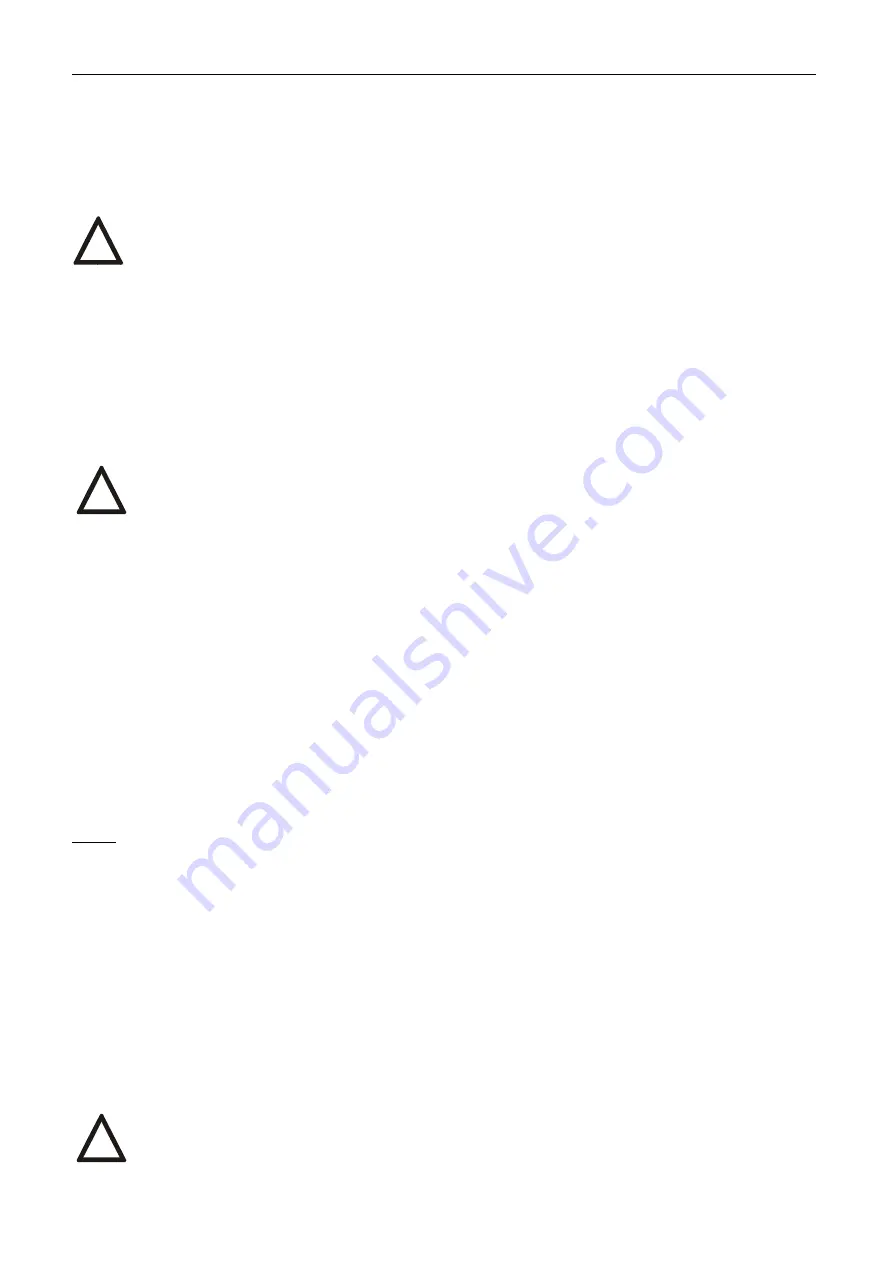
14
SP 1-Ex
3.2 Electric connection and checking of function
Follow up with connecting the EA with mains or master system.
1. Follow instructions in the part "Requirements for professional qualification"!
2. While laying electrical line abide by the instructions for heavy current installations.
3. Cables to terminal boards or connectors lead through screw bushings.
4. Before initiation ES into operation internal and external protection terminals are needed to be
connected.
5. Feeding cables are to be fixed to the solid construction at most 150 mm from the bushings.
Connecting with the master system:
The EA can be controlled with:
•
a built-in position controller
•
an external position controller
1. If the EA is controlled with an external controller using unified signal from a two- wire transmitter
(capacitive or resistive with a converter in two-wire connection), it is needed to arrange connecting of
the two-wire transmitter loop to electrical earth of the successive external controller!
2. Connection can be performed only in one point, in any part of loop out of the EA.
3. Electronics of the two-wire transmitters is galvanically insulated that is why it can serve as an
external source for supplying of several transmitters (their number depends on current which the
source can supply).
4. Do not connect and disconnect live connectors)!
Connecting to terminal board
•
Check whether the type of current, supply voltage and frequency correspond with data on the
nameplate of electric motor.
•
Remove the upper cover.
•
In case of the single-phase version the phase L1 and the lead N connect to the corresponding
terminals. In case of the three-phase version connect the phase cables L1, L2 and L3 to U, V, W
(terminals 2, 3, 4), the protection cables to the marked places of internal and external protection
terminals.
•
Connect the control cables according to the wiring diagram placed into the internal side of the
cover.
•
Put the cover on and tighten it uniformly crosswisely.
•
Tighten the cable bushings firmly to assure the protection enclosure rate.
Notes:
1. The EA are delivered with bushings, which in case of tight putting on the leads assure protection enclosure
IP 67 at least. For required protection enclosure it is needed to use rings according to the actual cable
diameter and required thermal resistance.
2. While fixing the cable it is needed to count with allowed bend radius to avoid damaging or deformation of the
sealing element of the bushing. The leads are to be fixed with the solid construction at most 150 mm from
the bushings.
3. It is recommended to use screened cables to connect remote transmitters.
4. The face areas of the control part cover have to be before re-mounting clean, coated with a grease without
any acid (e.g. vaseline) and sealing not damaged to avoid joint corrosion.
5. Reversation of the EA is sure, if the period between switching-off and switching-on of power supply for the
reversed movement of the output part is minimally 50 ms.
6. Delay after switching-off, i.e. time since a reaction of switches till the motor is dead can be maximally 20 ms.
7. It is recommended to have the corresponding direction protection switched-off directly with the
corresponding position or torque switches.
Abide by instructions of valve producers, whether switching-off in limit positions is to
be realised with position or torque switches!
!
!
!
Содержание SP 1-Ex
Страница 28: ...26 SP 1 Ex 7 Enclosures 7 1 Wiring diagrams Wiring diagrams EA SP 1 Ex...
Страница 29: ...SP 1 Ex 27 Wiring diagrams EA SP 1 Ex with controller ERROR MESSAGE ERROR MESSAGE...
Страница 30: ...28 SP 1 Ex...
Страница 33: ...SP 1 Ex 31 7 2 Dimensional drawings 7 2 1 Dimensional drawings flange connection Flange...
Страница 35: ...SP 1 Ex 33 Coupling shape Pull rod TV360...