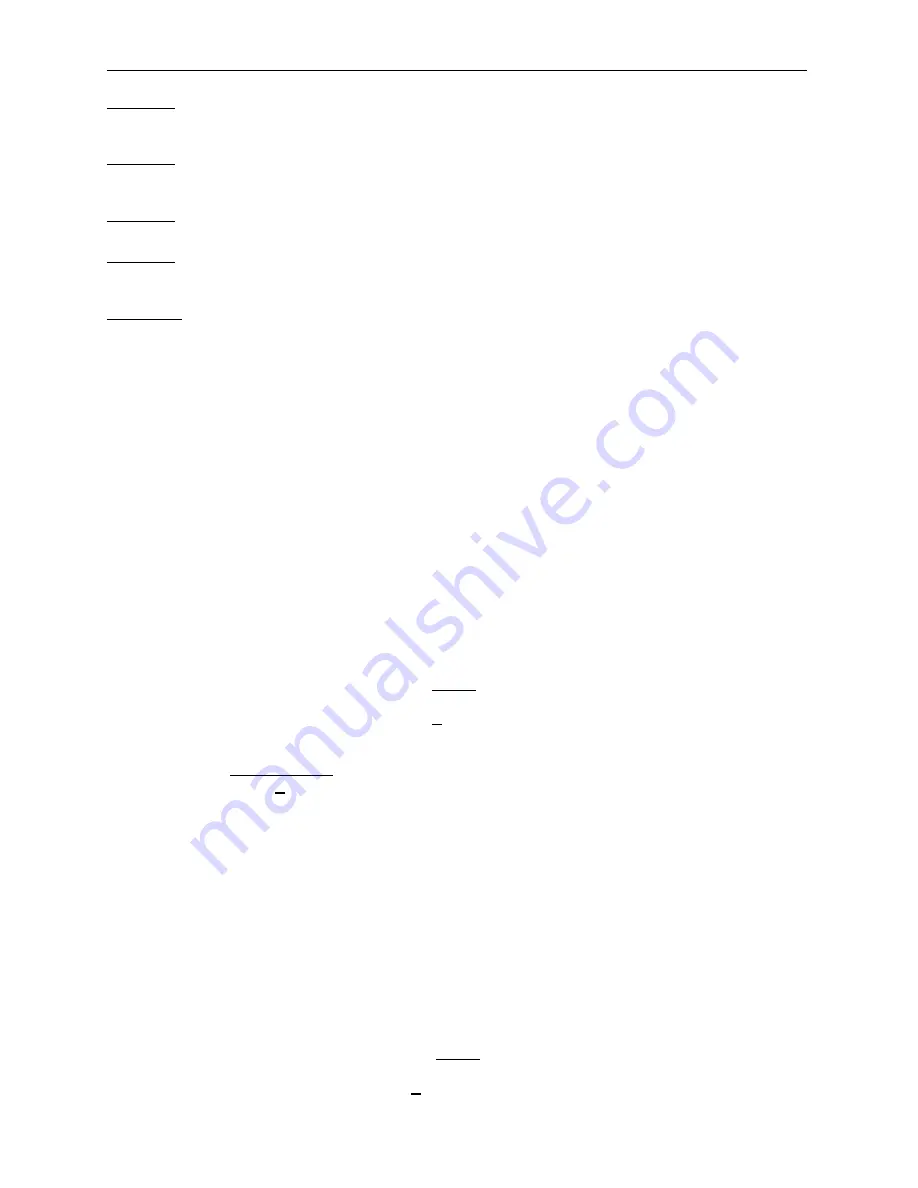
28
ULR 1PA-Ex, ULR 2PA-Ex
Warning 1:
W
hen the input control signal is set to the value 0
÷
20 mA
(0 to 10 V)
, or 20
÷
0 mA
(10 to 0 V)
and
the input control signal fails, then the EA keeps the position as with a 0 mA
(0 V)
input signal (EA doesn’t
recognise between input signal fail and 0 mA
(0 V)
input signal).
Warning 2: Auto-calibration process doesn’t run if triggered in time when the EA is in error state, e.g. EA is
overloaded (EA is switched -off from torque). In such case is necessary to resolve issue, e.g. the EA must be
moved in a position in which is not switch-off from torque and to start the auto-calibration again.
Warning 3: Calibration process must be performed at any change of the operating angle value of more than
10%.
Warning 4: Operate adjusting button
P
on the control to activate the calibration process or start it from
MENU 4
in the version with local control (use the buttons on local control) or from the programme once the EA is
connected to the PC. All calibration start methods have been equal.
Note No. 5: In case that EA with supply voltage 3x400V AC after calibration start shows the error „rotation
direction“ (error No. 7), it is necessary to stop EA by switching-off the supply voltage and change the
phases sequence on the terminals 2 and 3 (change mutually phases wires) and after switching-on the
supply voltage run n the calibration again.
Rotation direction definition of the electric actuator´s output element
The output rod of the actuator while rotating in the direction “Close“ protrudes from the actuator. It means that
the direction of rotation of the actuator is set as clockwise.
In case the direction of rotation shall be changed the parater „Direction of rotation of the actuator“ must je
adjusted as anticlockwise. This parameter can be adjusted through the PC only by use of the EHL Explorer SW.
The PC must be connected to the actuator via communication cable and the window “Parameters“ used for
direction adjustment.
4.3 Putting an EA into operation when the EA is set up and connected with the
armature already in the production plant (starting the calibration)
If EA is delivered from manufacturing plant joined with valve, or with control device,
calibration
must
be performed to ensure correct operation, under actual pipeline conditions.
The procedure is as follows:
-
fit the given assembly into the specified technology complex
-
connect the EA on the supply voltage electrically according to the wiring diagram and chapter
Electric connection and checking of function.
-
introduce the EA into an mid-position (see
Note 2
presented above)
-
switch on the supply voltage
-
start the EA calibration
by pressing the
P
button on the control unit
for 2 seconds as minimum
until LED ERROR (red), LED MENU (green) and LED PAR (red) light up – see also the procedure in
the separate attachment
No.74 1053 02
-
release the
P
setting button
-
after releasing the
P
button the calibration procedure starts – inertia measuring
-
after the calibration procedure is finished, the EA is prepared for its operation and starts to response
to control inputs
-
if changes to some parameters would be necessary, proceed please according to the instructions
given in the separate attachment
No. 74 1053 02
.
4.4
Putting an EA into operation when the stroke and parameter setting done by the
producer suit to your needs
When an EA is delivered from the producer without armature and the setting of stroke (stroke end
positions) and other parameters done by the producer suit Your needs, please proceed as follows:
-
connect the EA with the armature to be controlled (
according to chapter 2
) and fit this assembly
into the specified technology complex
-
connect the EA electrically according to the wiring diagram and chapter Electrical connection and
checking of function
-
introduce the EA into an mid- position (see
Note 2
presented above)
-
switch on the supply voltage
-
start the EA calibration by pressing the
P
button on the control unit
for 2 seconds as minimum
until
LED ERROR (red), LED MENU (green) and LED PAR (red) light up – see also the procedure in the
separate attachment No. 74 1053 02
-
release the
P
setting button
Содержание REMATIC ULR 1PA-Ex
Страница 13: ...ULR 1PA Ex ULR 2PA Ex 11 Fig 1 2 1 7 6 5 4 8 3...
Страница 14: ...12 ULR 1PA Ex ULR 2PA Ex Fig 1A 8 2 4 6 5 5 3 7 1...
Страница 38: ...36 ULR 1PA Ex ULR 2PA Ex 7 Enclosures 7 1 Wiring diagrams ULR 1PA Ex and ULR 2PA Ex...
Страница 39: ...ULR 1PA Ex ULR 2PA Ex 37...
Страница 40: ...38 ULR 1PA Ex ULR 2PA Ex...
Страница 41: ...ULR 1PA Ex ULR 2PA Ex 39...
Страница 42: ...40 ULR 1PA Ex ULR 2PA Ex...
Страница 45: ...ULR 1PA Ex ULR 2PA Ex 43 7 2 Dimensional drawings Explosion proof electric linear actuator Rematic ULR 1PA Ex...
Страница 46: ...44 ULR 1PA Ex ULR 2PA Ex...
Страница 47: ...ULR 1PA Ex ULR 2PA Ex 45...
Страница 48: ...46 ULR 1PA Ex ULR 2PA Ex Explosion proof electric linear actuator Rematic ULR 2PA Ex...