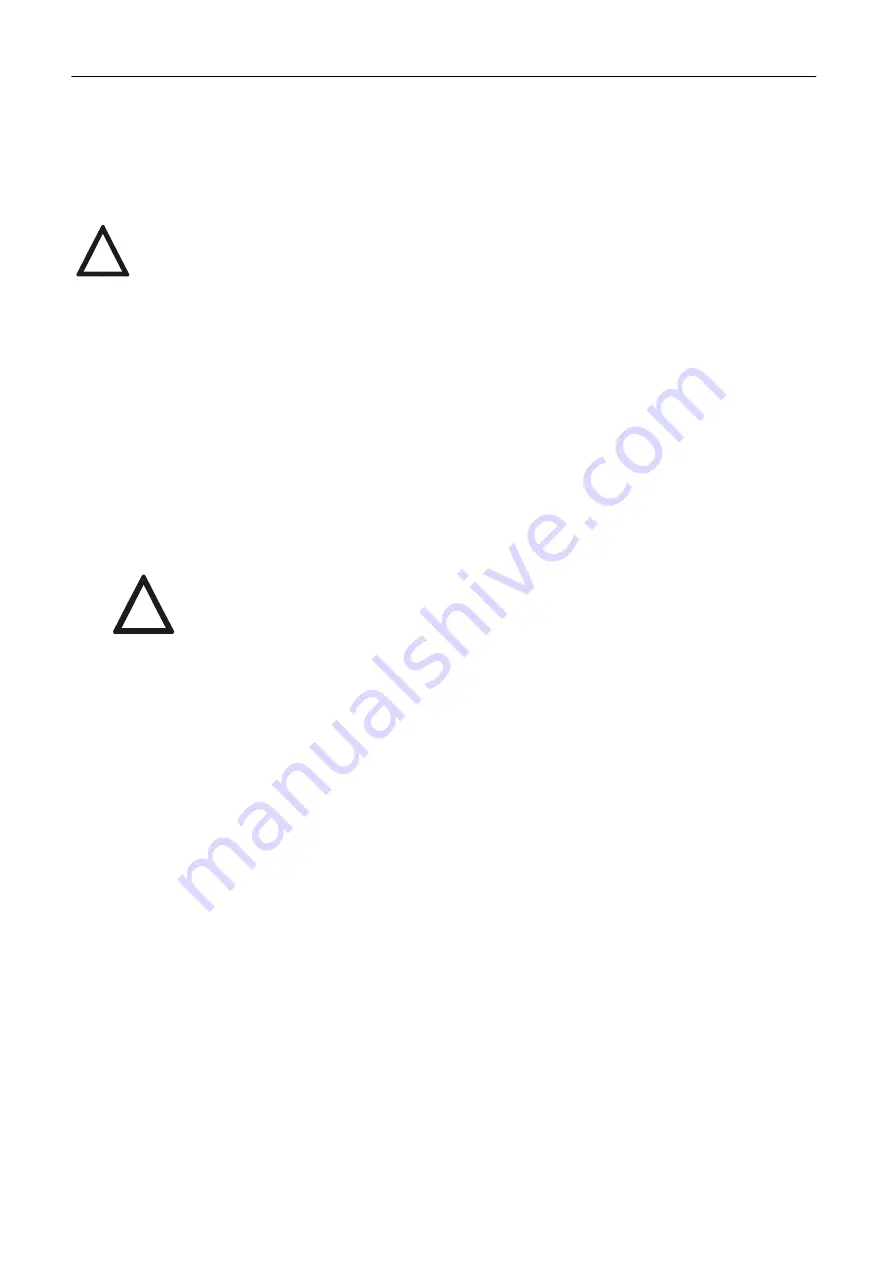
MO 3, MO 3.3, MO 3.4, MO 3.5
19
Check of position switches (Fig.6,8).
When the actuator moves towards "close" switch over contacts of
switches S4 resp. S6 by pressing of disconnecting bell of relevant switch. If the connection is properly
performed, the actuator must stop when contacts of switch S4 are switched over and light up when contacts of
switch S6 are switched over. Analogous repeat test towards "open". By pressing disconnecting bell of switches
S3 resp. S5, the actuator must stop resp. signalize. Again, if any of the function is not correct, connection of
switches should be checked according to wiring diagram.
In the
EA MO
with controller
version
with the built-in electronic controller (Fig.13) it is needed to
perform
autocalibration
for assuring optimal functioning.
The procedure is as follows
•
Preset the EA to a mid-position position (position and torque switches are not hooked)
•
Press the button
SW1
for about 2 sec (i.e. till the
D3
diode is got on) to set the controller to the
autocalibration
mode. During this process the controller checks the feedback transmitter and the sense of
turning, puts the EA to the positions open and closed, measures inertia mass in the directions "opening" and
"closing", and loads the adjusted parameters into the EEPROM memory. In case that during the initialization
process an error occurs (e.g. in connection or adjustment) the initialization process will be interrupted and
the controller with the
D4
diode reports about the type of the error. Else after finishing the initialization
process the controller is put into the
regulation
mode
. If needed to change adjusted parameters of the
controller follow instructions given in the part “Adjusting of actuator”.
3.2 Disassembly
Attention!
Before disassembly is necessary to disconnect electric supply of electric actuator!
Connection and disconnection of connectors must not be performed under the voltage!
Secure by prescribed way protection against connection of EA to the network and thus
potential electrical accident!
•
Disconnect the EA from mains.
•
Disconnect the leads from the EA terminal boards and loosen the cables from bushings. Pull out the
connectors in case of the connector version.
•
Loosen the fixing screws of the EA flange and disconnect the EA from the valve/gearing.
•
While sending the EA to be repaired put it into a package solid enough to avoid damages of the EA during
transportation.
!
!
Содержание MO 3
Страница 35: ...MO 3 MO 3 3 MO 3 4 MO 3 5 33 7 Enclosures 7 1 Wiring diagrams Wiring diagrams MO...
Страница 36: ...34 MO 3 MO 3 3 MO 3 4 MO 3 5...
Страница 37: ...MO 3 MO 3 3 MO 3 4 MO 3 5 35 Wiring diagrams MO with controller...
Страница 41: ...MO 3 MO 3 3 MO 3 4 MO 3 5 39 4 x tooth F10 shape D F10 shape C DIN 3338 F10 shape E ISO 5210...
Страница 42: ...40 MO 3 MO 3 3 MO 3 4 MO 3 5 Mechanic connections for EA MO 3...
Страница 43: ...MO 3 MO 3 3 MO 3 4 MO 3 5 41...
Страница 45: ...MO 3 MO 3 3 MO 3 4 MO 3 5 43 Dimension drawings for EA MO 3 5...
Страница 46: ...44 MO 3 MO 3 3 MO 3 4 MO 3 5 Dimension drawings for EA MO 3 4...
Страница 47: ...MO 3 MO 3 3 MO 3 4 MO 3 5 45 Dimension drawings for EA MO 3 3...
Страница 50: ...48 MO 3 MO 3 3 MO 3 4 MO 3 5 Mechanic connections for EA MO 3 4 with connect adapter...
Страница 51: ...MO 3 MO 3 3 MO 3 4 MO 3 5 49...
Страница 53: ...MO 3 MO 3 3 MO 3 4 MO 3 5 51 Mechanic connections for EA MO 3 5 with connect adapter F14 shape A ISO 5210...