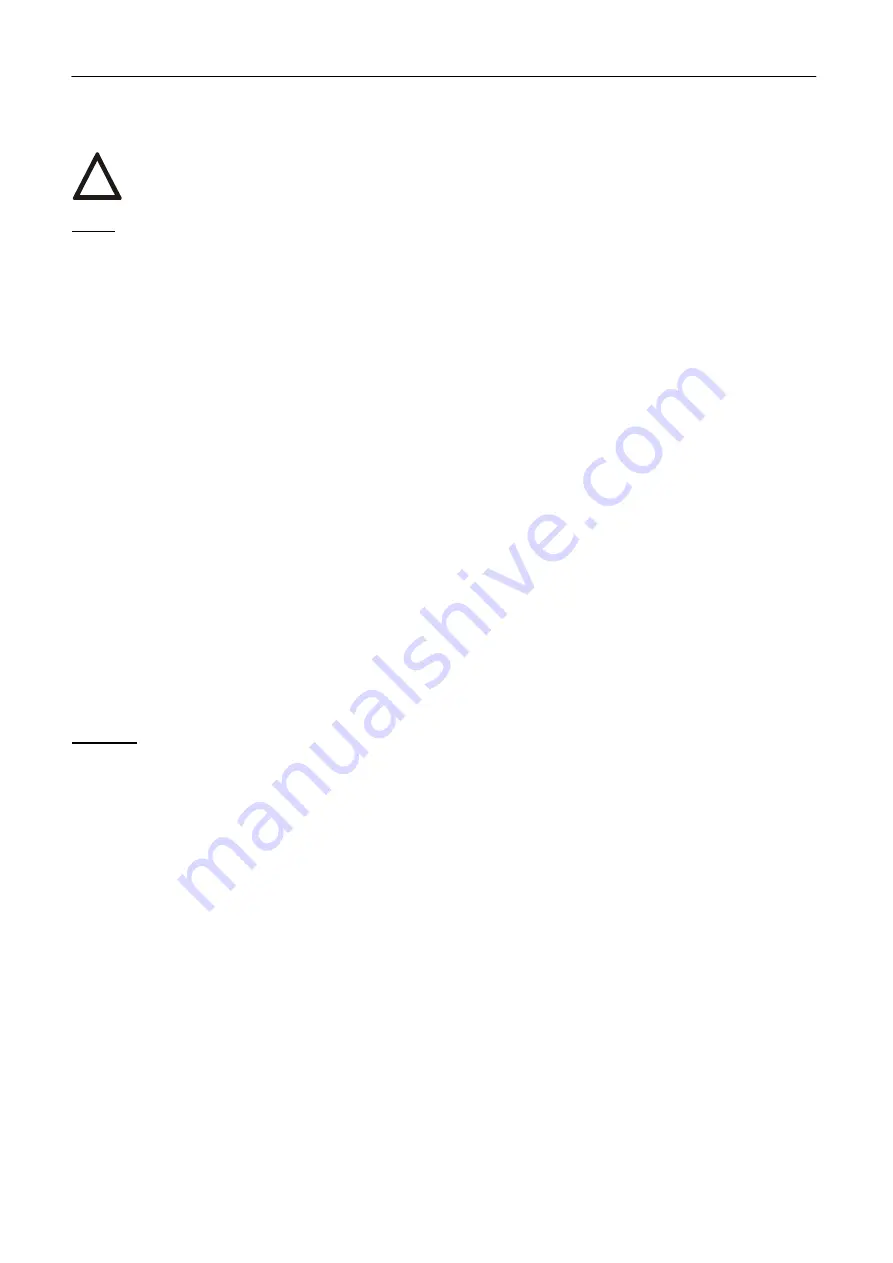
MO 3, MO 3.3, MO 3.4, MO 3.5
17
3. Installation and dismantling of actuator
Abide by safety measures!
Notes:
Repeatedly verify whether placing of EA correspondents to part "Operating conditions". If actual conditions
differ from recommended, it is necessary to consult it with manufacturer.
Before starting of mounting the EA onto the valve:
•
Check again whether the EA was not damaged during storing.
•
Check whether the adjusted operating speed angle and connecting dimensions of the actuator (see the
nameplate) are in compliance with the valve parameters.
•
In case of inconsonance, perform adjusting according to the part Adjustment.
3.1 Installation
The actuator is set up by the manufacturer to the parameters according to label tag, with connecting
dimensions according to relevant dimensional drawing and is set to mid - position.
Put on the hand wheel before assembly.
3.1.1 Mechanical connection to the armature
In case that required shape of mechanical connection is designed by A-shape adapter (with flange F16,
F14 or F10), resp. C-shape adapter (with flange F14) at first is necessary to fix this adapter to connecting flange
of EA by the screws.
Mechanical connection – shape of connecting element B, C, D, E (eventually B3) and gear clutch :
•
Bearing surfaces of EA connecting flange must be carefully de-greased.
•
Slightly grease the shaft of armature/gearbox by acid-free grease;
•
Shift EA to its terminal position „CLOSED“; shift armature into identical terminal position.
•
Put EA on armature, so as output shaft reliably fits into clutch of armature.
Warning!
Do not use force when you put EA on armature, otherwise the gear can be damaged!
•
Should there is the necessity to synchronize the openings in the EA flange and armature, turn the EA by hand
wheel;
•
Verify, whether connecting flange fits tightly to the armature / gearbox.
•
Attach the flange by four bolts (with mechanical hardness min. 8G), which steadily tighten crosswise.
•
At the end of mechanical connection perform
the check of proper connection with the armature,
by
turning hand wheel in the „open“ direction.
Mechanical connection – rising spindle (for shape A, C resp. B3):
•
If the rising spindle of armature is in terminal position „open“ longer than dimension of mounting flange up to
the control box cover, disassembly cover of output shaft (Fig.1) on control box and replace it by covering
pipe (not part of delivery) after assembly of electric actuator on armature.
•
Seating surfaces of EA connecting flange and armature carefully de-grease.
•
Slightly grease the output shaft of armature.
•
Shift EA to terminal position „CLOSED“; shift armature into identical terminal position.
•
Slide electric actuator by output shaft / nut on the spindle / nut of armature and turn by hand wheel
counterclockwise until connecting flange of electric actuator fits to connecting flange of armature. Further
procedure is identical to previous part of mechanical connection for shapes B, C, D.
•
At the end of mechanical connection perform the check of proper connection of EA with the armature by tur-
ning the hand control wheel wheel in the „open“ direction.
Note:
It is also possible to fix the EA on the wall construction using the three feeders located at the box external wall,
opposite to the hand wheel.
!
Содержание MO 3
Страница 35: ...MO 3 MO 3 3 MO 3 4 MO 3 5 33 7 Enclosures 7 1 Wiring diagrams Wiring diagrams MO...
Страница 36: ...34 MO 3 MO 3 3 MO 3 4 MO 3 5...
Страница 37: ...MO 3 MO 3 3 MO 3 4 MO 3 5 35 Wiring diagrams MO with controller...
Страница 41: ...MO 3 MO 3 3 MO 3 4 MO 3 5 39 4 x tooth F10 shape D F10 shape C DIN 3338 F10 shape E ISO 5210...
Страница 42: ...40 MO 3 MO 3 3 MO 3 4 MO 3 5 Mechanic connections for EA MO 3...
Страница 43: ...MO 3 MO 3 3 MO 3 4 MO 3 5 41...
Страница 45: ...MO 3 MO 3 3 MO 3 4 MO 3 5 43 Dimension drawings for EA MO 3 5...
Страница 46: ...44 MO 3 MO 3 3 MO 3 4 MO 3 5 Dimension drawings for EA MO 3 4...
Страница 47: ...MO 3 MO 3 3 MO 3 4 MO 3 5 45 Dimension drawings for EA MO 3 3...
Страница 50: ...48 MO 3 MO 3 3 MO 3 4 MO 3 5 Mechanic connections for EA MO 3 4 with connect adapter...
Страница 51: ...MO 3 MO 3 3 MO 3 4 MO 3 5 49...
Страница 53: ...MO 3 MO 3 3 MO 3 4 MO 3 5 51 Mechanic connections for EA MO 3 5 with connect adapter F14 shape A ISO 5210...