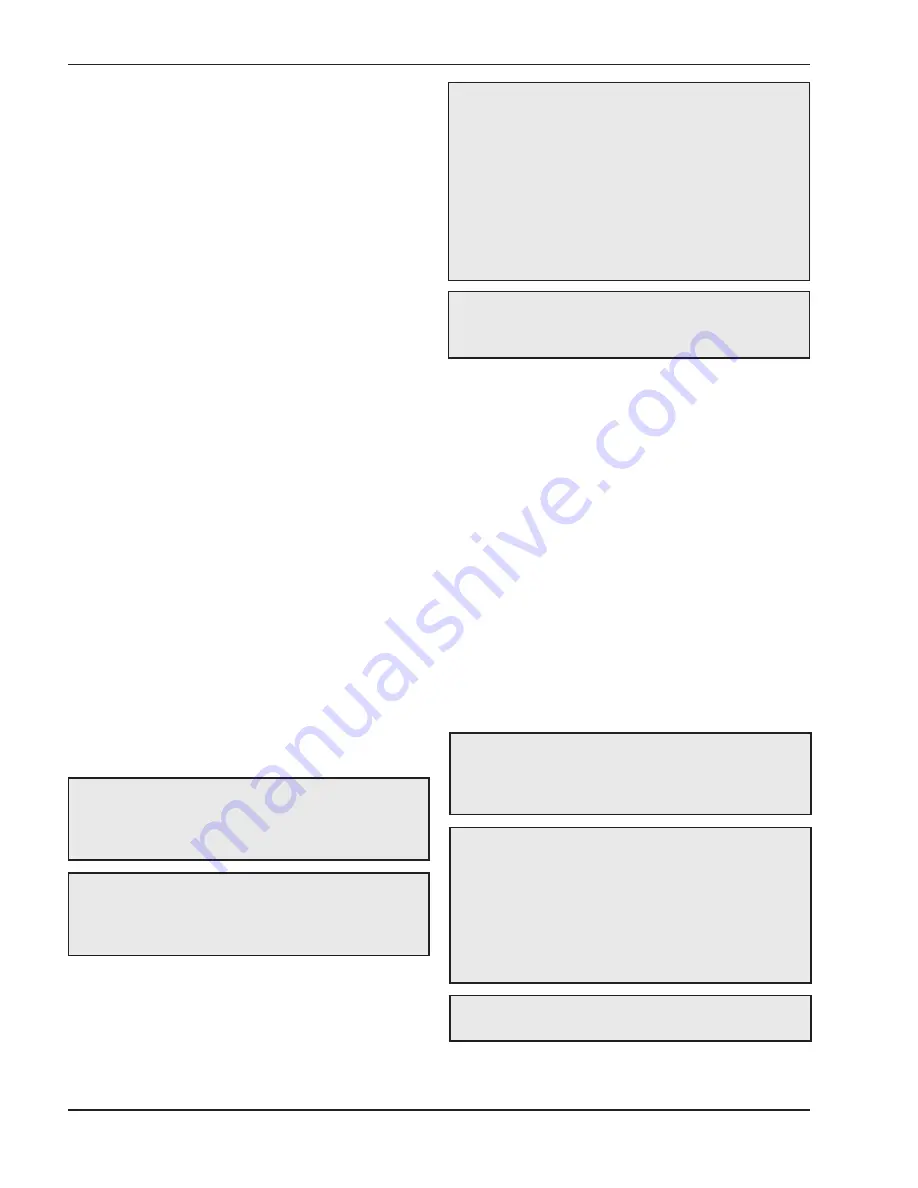
32
The minimum flue pipe diameter for conventional vent-
ing is: 3 in. (76 mm) for Models 88AR (2” optional),
108AR, 198AR and 278AR, and 4 in. (102 mm) for
Models 398A (3” optional).
The connection from the appliance vent to the stack
must be as direct as possible and shall be the same
diameter as the vent outlet. The horizontal breaching
of a vent must have an upward slope of not less than
1/4 inch per linear foot from the heater to the vent ter-
minal. The horizontal portions of the vent shall also be
supported for the design and weight of the material
employed to maintain clearances and to prevent physi-
cal damage or separation of joints.
The vent terminal should be vertical and should termi-
nate outside the building at least 2 ft above the highest
point of the roof that is within 8 ft. The vent cap should
have a minimum clearance of 4 ft horizontally from and
in no case above or below (unless a 4 ft hori-zontal
distance is maintained) electric meters, gas meters,
regulators and relief equipment.
The distance of the vent terminal from adjacent public
walkways, adjacent buildings, open windows and
building openings must be consistent with the NFGC
(U.S.) or B149 (Canada). Vents supported only by
flashing and extending above the roof more than 5 ft
should be securely guyed or braced to withstand snow
and wind loads.
Common Venting
The NFGC does not address sizing guidelines for the
common venting of multiple Category IV heaters. This
is covered in the NFGC under “Engineered Vent Sys-
tems”. Table O provides volumes of flue products at
full fire for the calculation of appropriate vent and
extractor sizing for common venting.
WARNING:
Vent connectors serving any other
appliances shall not be connected into any portion of
mechanical draft systems operating under a positive
pressure. If an XPak FT boiler is installed to replace
an existing boiler, the vent system MUST be verified
to be of the correct size and of Category IV AL29-4C
vent material, approved PVC/CPVC construction, or
DuraVent
®
polypropylene (in Canada, ULC- S636
approved plastic materials must be used). If it is
NOT, it MUST be replaced..
NOTE:
For extractor sizing, typical CO2 levels are
9.0% for natural gas and 10.5% for propane gas and
flue temperatures of less than 180°F.
CAUTION:
A listed vent cap terminal suitable for
connection to the Cat IV vent materials, adequately
sized, must be used to evacuate the flue products
from the boilers.
At the time of removal of an existing boiler, the follow-
ing steps shall be followed with each appliance
remaining connected to the common venting system
placed in operation, while the other appliances remain-
ing connected to the common venting system are not
in operation:
(a) Seal any unused openings in the common venting
system.
(b) Visually inspect the venting system for proper size
and horizontal pitch and make sure there is no
blockage or restriction, leakage, corrosion and
other deficiencies which could cause an unsafe
condition.
(c) Place in operation the appliance being inspected.
Follow the lighting instructions. Adjust thermostat
so appliance will operate continuously.
WARNING:
An extractor is required when multiple
heaters are vented through a common vent pipe.
The extractor must operate when one or more units
are firing.
NOTE:
While a drain connection is required in the
vent of all XPak FT installations, the drain can be ac-
complished in several different ways. The figures in
this manual show the drain in a vent tee, however,
this can also be accomplished using an inline collec-
tor for condensing stacks or an inline vertical or
horizontal collector available from several of the
listed vent manufacturers.
WARNING:
Condensate is acidic and highly
corrosive.
NOTE:
Vent and intake piping must be supported so
that the weight of the venting is not transfered to the
unit. Horizontal runs of vent and intake piping must
be supported to prevent sagging.
Содержание 88AR-398A
Страница 18: ...18 Fig 13 MODE 1 Single Boiler Primary Secondary Piping...
Страница 19: ...19 Fig 14 MODE 2 Single Boiler Primary Secondary Piping with Indirect DHW on System Loop...
Страница 20: ...20 Fig 15 MODE 3 Single Boiler Primary Secondary Piping with Indirect DHW on Boiler Loop...
Страница 47: ...47 WIRING DIAGRAM Fig 46 Wiring Diagram...
Страница 54: ...54 Fig 55 Boiler Lighting Shut Off Instructions...
Страница 65: ...65 ILLUSTRATED PARTS LIST...
Страница 66: ...66...
Страница 67: ...67...
Страница 68: ...68 www raypak com Raypak Inc 2151 Eastman Avenue Oxnard CA 93030 805 278 5300 Fax 805 278 5468 Litho in U S A...