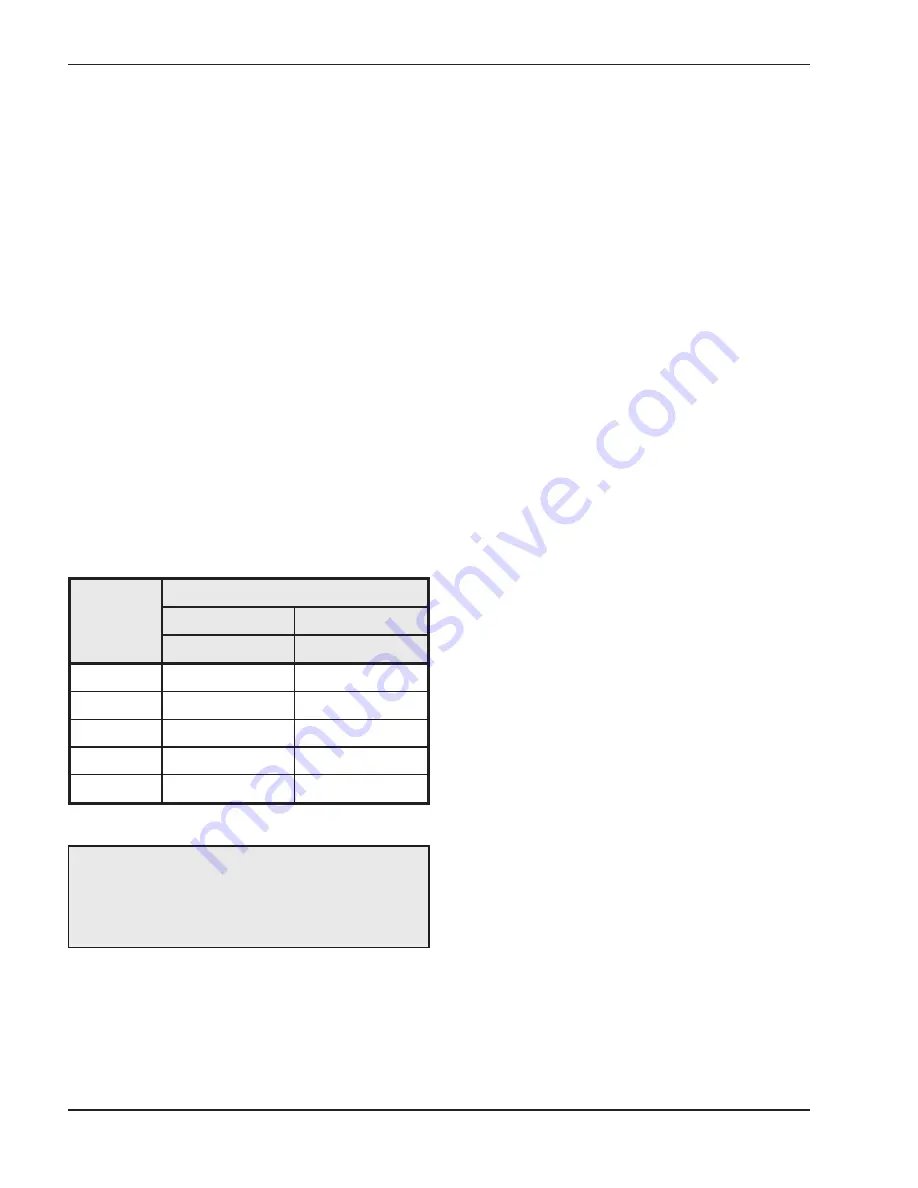
22
CAUTION:
For proper operation, no more than a
30% drop in gas supply pressure from no-load to full-
load conditions is acceptable. Under no
circumstances should the pressure be outside the
listed operational range.
Gas Supply Pressure
A minimum of 4.5 in. WC upstream gas pressure
under full load and a maximum gas supply pressure
setpoint of 10.5 in. WC under load and no-load condi-
tions for natural gas. A minimum of 8.0 in. WC
upstream gas pressure under full load and a maximum
gas supply pressure setpoint of 13.5 in. WC is required
for propane gas. The gas pressure regulator(s) sup-
plied on the boiler is for low-pressure service. If
upstream pressure exceeds 1/2 PSI at any time, an
intermediate gas pressure regulator, of the lockup
type, must be installed. This regulator should be
placed a minimum distance of 10 times the pipe diam-
eter upstream of the boiler gas controls.
When connecting additional gas utilization equipment
to the gas piping system, the existing piping must be
checked to determine if it has adequate capacity for
the combined load. The gas valve pressure regulator
on the boiler is nominally preset as noted in Table K.
During normal operation, carbon dioxide should be 8.8
to 10.5% at full fire for natural gas and between 10.2
and 10.8% for propane gas. Carbon monoxide should
be ‹200 ppm.
Table K: Manifold Gas Pressure Settings
Model
No.
Manifold Pressure (in. WC)
Natural Gas
Propane Gas
High
High
88AR
-.1” WC
-.1” WC
108AR
-.1” WC
-.1” WC
198AR
-2.0” WC
-1.4” WC
278AR
-2.1” WC
-2.0” WC
398A
-3.4” WC
-3.0” WC
Electrical Power Connections
Installations must follow these codes:
•
National Electrical Code and any other national,
state, provincial or local codes or regulations hav-
ing jurisdiction.
•
Safety wiring must be NEC Class 1.
•
Heater must be electrically grounded as required
by the NEC.
•
In Canada, CSA C22. 1 C.E.C. Part 1.
The XPak FT 88AR-398A boilers are wired for 120
VAC single-phase 60 Hz power. Consult the wiring dia-
gram shipped with the unit. Before starting the boiler,
check to ensure proper voltage to the boiler and
pump(s).
The expected current draw for the boiler is less than 5
amps. The pump load is additional.
The boiler pump (up to ¼ HP) and the indirect DHW
pump (up to ¼ HP) get their power supply directly from
the boiler power supply. The system pump relay is
rated for pilot duty only. An indirect DHW pump larger
than ¼ HP or 5A must use a separate power supply
and run the power through an external field-supplied
pump contactor. Use appropriately-sized wire as
defined by NEC, CSA and/or local codes. All primary
wiring should be 125% of minimum rating. The indi-
rect and system pumps outputs are fuse-protected.
If any of the original wire as supplied with the boiler
must be replaced, it must be replaced with 105°C wire
or its equivalent.
All 120VAC field wiring connections to the XPak FT are
made inside the rear wiring box as shown in Fig. 17.
Low-voltage wiring is connected to the VERSA control
board and the Platform Ignition Module (PIM) at the
front of the unit. Sensors, enable/disable contacts,
(optional) 0-10 VDC control wiring, and cas- cade con-
nections are wired into the VERSA and PIM field wiring
plugs. See the wiring diagram on page 47.
Содержание 88AR-398A
Страница 18: ...18 Fig 13 MODE 1 Single Boiler Primary Secondary Piping...
Страница 19: ...19 Fig 14 MODE 2 Single Boiler Primary Secondary Piping with Indirect DHW on System Loop...
Страница 20: ...20 Fig 15 MODE 3 Single Boiler Primary Secondary Piping with Indirect DHW on Boiler Loop...
Страница 47: ...47 WIRING DIAGRAM Fig 46 Wiring Diagram...
Страница 54: ...54 Fig 55 Boiler Lighting Shut Off Instructions...
Страница 65: ...65 ILLUSTRATED PARTS LIST...
Страница 66: ...66...
Страница 67: ...67...
Страница 68: ...68 www raypak com Raypak Inc 2151 Eastman Avenue Oxnard CA 93030 805 278 5300 Fax 805 278 5468 Litho in U S A...