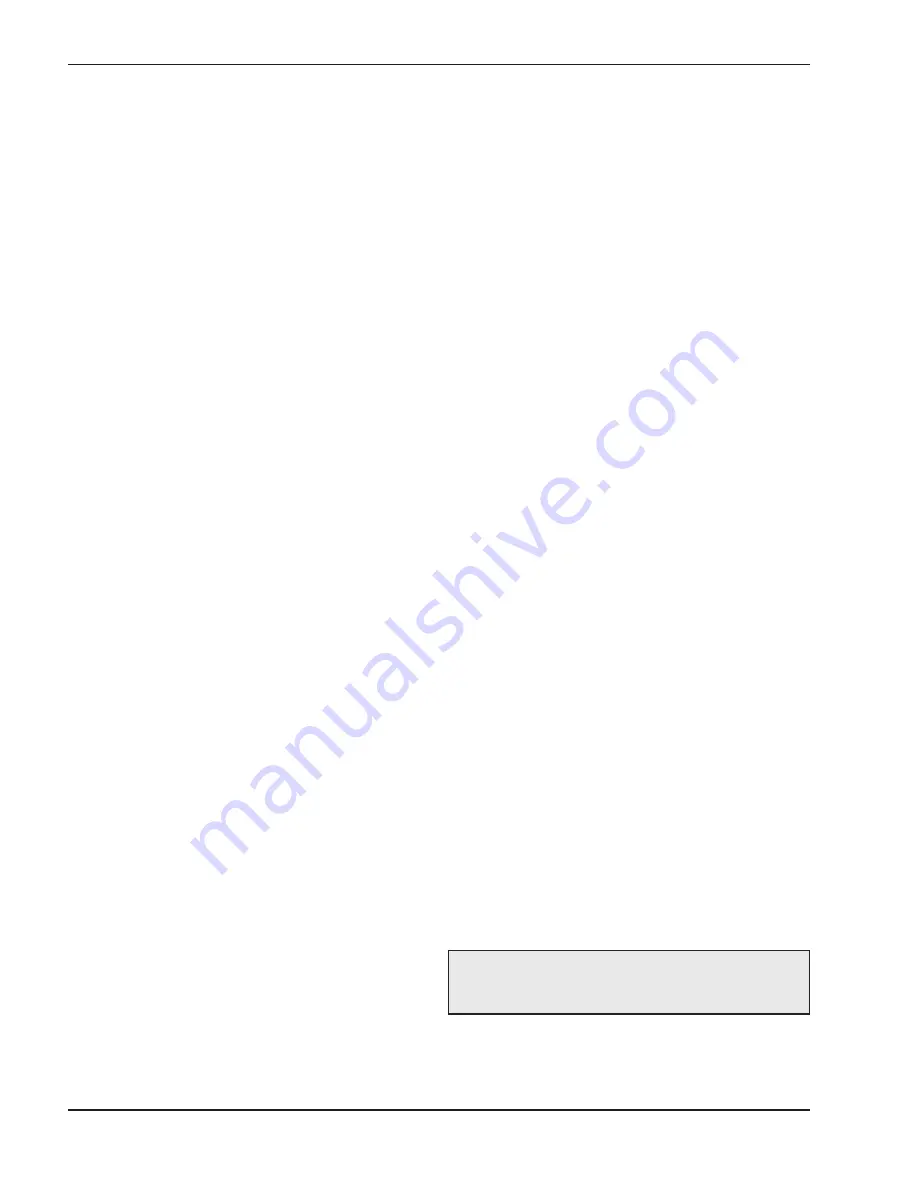
14
Direct Vent
If outside air is drawn through the intake pipe directly
to the unit for combustion:
1. Install the combustion air ducting kit.
2. Install combustion air direct vent in accordance
with Fig. 24 (horizontal) or Fig. 26 (vertical) of this
manual.
3. Ventilation of the space occupied by the boiler(s)
is recommended and can be provided by an open-
ing(s) for ventilation air at the highest practical
point communicating with the outdoors. The total
cross-sectional area should be at least 1 in² of free
area per 20,000 BTUH (111 mm² per kW) of total
input rating of all equipment in the room when the
opening is communicating directly with the out-
doors or through vertical duct(s). The total
cross-sectional area should be at least 1 in² of free
area per 10,000 BTUH (222 mm² per kW) of total
input rating of all equipment in the room when the
opening is communicating with the outdoors
through horizontal duct(s). Damage to the equip-
ment due to inadequate ventilation of the space is
not a warrantable failure.
4. In cold climates, and to mitigate potential freeze-
up, Raypak highly recommends the installation of
a motorized sealed damper on the air intake to
prevent the circulation of cold air through the boiler
during non-operating hours.
Conventional Combustion Air
Supply
U.S. Installations
All Air from Inside the Building
The confined space shall be provided with
TWO
per-
manent openings communicating directly with an addi-
tional room(s) of sufficient volume so that the com-
bined volume of all spaces meets the criteria for a
room large in comparison (NFGC). The total input of all
gas utilization equipment installed in the combined
space shall be considered in making this determina-
tion.
Each opening
shall have a minimum free area
of 1 in.2 per 1,000 BTUH (2,225 mm2 per kW) of the
total input rating of all gas utilization equipment in the
con- fined space, but not less than 100 in.2 (645 cm2).
One opening shall commence within 12 in. (305 mm)
of the top, and one opening shall commence within 12
in. (305 mm) of the bottom of the enclosure. The mini-
mum dimension of air openings shall be not less than
3 in. (76 mm) in any direction.
All Air from Outdoors
The confined space shall communicate with the out-
doors in accordance with one of the methods below.
The minimum dimension of air openings shall not be
less than 3 in. (76 mm) in any direction. Where ducts
are used, they shall be of the same cross-sectional
area as the net free area of the openings to which they
connect.
1.
Two permanent openings
, one commencing
within 12 in. (305 mm) of the top, and one com-
mencing within 12 in. (305 mm) of the bottom of
the enclosure, shall be provided. The openings
shall communicate directly, or by ducts, with the
outdoors or spaces (crawl or attic) that freely com-
municate with the outdoors.
a. Where directly communicating with the out-
doors or where communicating to the
outdoors through vertical ducts,
each open-
ing
shall have a minimum free area of 1 in.
2
per 4,000 BTUH (550 mm
2
per kW) of total
input rating of all equipment in the enclosure.
b. Where communicating with the outdoors
through horizontal ducts, each opening shall
have a minimum free area of 1 in.
2
per 2,000
BTUH (1,100 mm
2
per kW) of total input rat-
ing of all equipment in the enclosure.
2.
One permanent opening
, commencing within 12
in. (305 mm) of the top of the enclosure, shall be
permitted where the equipment has clearances of
at least 1 in. (25 mm) from the sides, top and bot-
tom and 6 in. (152 mm) from the front of the
appliance. The opening shall directly communi-
cate with the outdoors or shall communicate
through a vertical or horizontal duct to the out-
doors or spaces that freely communicate with the
outdoors, and shall have a minimum free area of:
a. 1 in.
2
per 3,000 BTUH (740 mm
2
per kW) of
the total input rating of all equipment located in
the enclosure, and
b. Not less than the sum of the areas of all vent
connectors in the confined space.
WARNING:
Do not use the “one permanent
opening” method if the equipment room is under
negative-pressure conditions.
Содержание 88AR-398A
Страница 18: ...18 Fig 13 MODE 1 Single Boiler Primary Secondary Piping...
Страница 19: ...19 Fig 14 MODE 2 Single Boiler Primary Secondary Piping with Indirect DHW on System Loop...
Страница 20: ...20 Fig 15 MODE 3 Single Boiler Primary Secondary Piping with Indirect DHW on Boiler Loop...
Страница 47: ...47 WIRING DIAGRAM Fig 46 Wiring Diagram...
Страница 54: ...54 Fig 55 Boiler Lighting Shut Off Instructions...
Страница 65: ...65 ILLUSTRATED PARTS LIST...
Страница 66: ...66...
Страница 67: ...67...
Страница 68: ...68 www raypak com Raypak Inc 2151 Eastman Avenue Oxnard CA 93030 805 278 5300 Fax 805 278 5468 Litho in U S A...