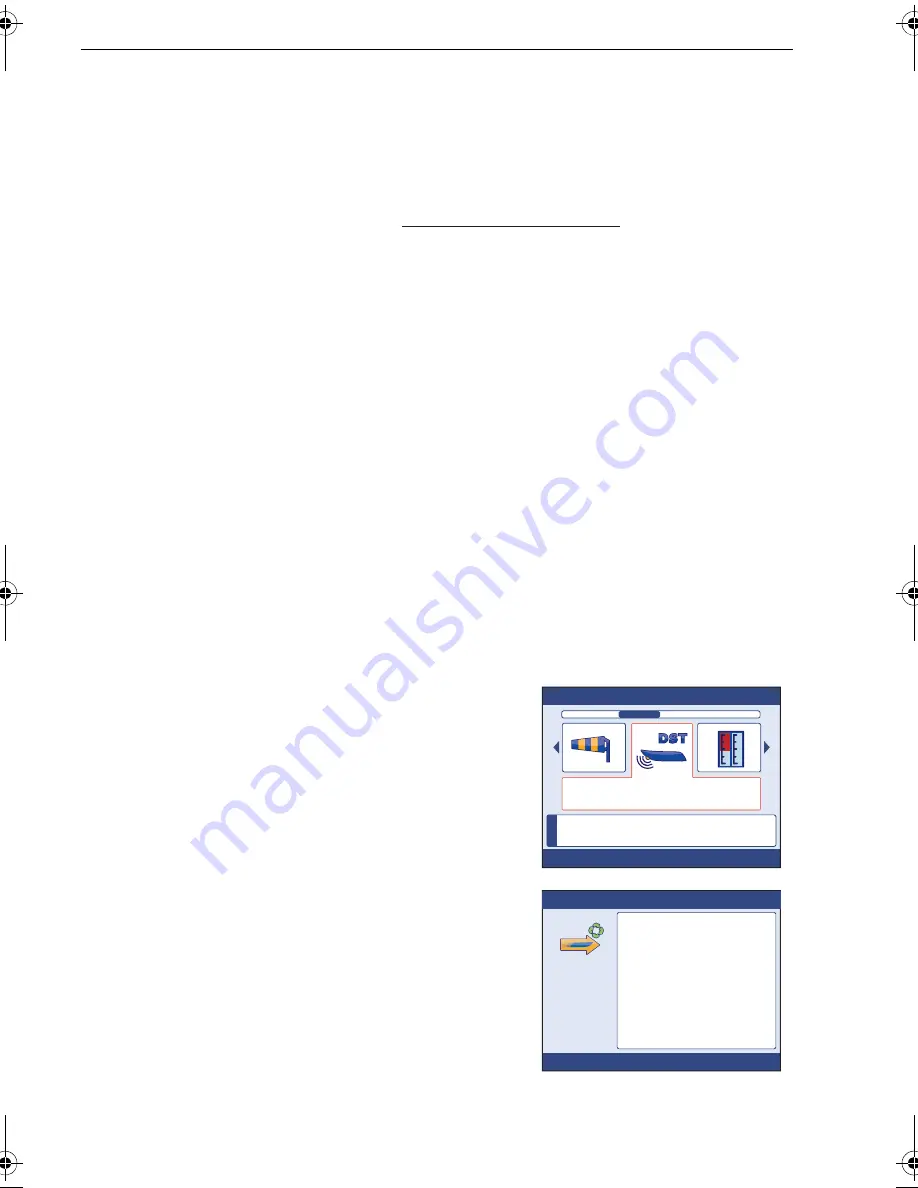
50
ST70+ User Reference Manual
4. If the calculated speed is:
• The same as the current speed value noted during the calibration run, then the
calibration is correct at this speed, so proceed from
Manual calibration
step 6.
• Not the same as the indicated speed:
i.Calculate a new, corrected calibration factor, as follows
ii.Press
PAGE DN
to highlight the calibration factor value field.
iii.Scroll to set the displayed calibration factor to the new calculated value.
5. Repeat
Manual calibration
steps 2 to 4, until the current speed value displayed
during the calibration run is the same as the calculated speed.
6. Press
PAGE UP
to highlight the calibration speed field.
7. Scroll to select the next calibration speed.
8. Repeat
Manual calibration
steps 2 to 7, until the calibration factor values are
correct at all calibration speeds.
9. Press
OK
to save the values and return to the
Speed
transducer setup menu.
10. Press
CANCEL
to return to the Transducers found menu.
Speed calibration for smart transducer
When fitted, a smart (DST800) transducer is calibrated to a set of six default speeds:
•
0.5 kt, 1.5 kt, 2.8 kt, 4.8 kt, 10.6 kt and 80 kt
These values provide acceptable transducer performance in most circumstances.
However you can insert and/delete different calibration speeds, up to a maximum of
eight, to provide a range of speed values to best suit the way the boat will be used.
To do this:
1. With the
Transducers Found
menu displayed
(see
Preliminary procedure
on
page 45
), scroll
to the
DST
option.
2. Press
OK
to select the DST
Details
page, then
press
OK
, to display the
Depth Offset
setup
page.
3. Ensure the correct depth offset is correct, then
press
OK
to display the DST
Temperature
page.
4. Press
OK
again to display the
Speed Calibra-
tion
page. This shows the list of speeds to
which the DST800 transducer is calibrated.
5. To change these speeds, press
OK
to display
the
Airmar Speed Calibration
menu. This gives
the following options:
•
Add point
. Use this to add a speed value to
the list of calibration speeds (see below).
•
Delete point
. Use this to remove a speed
value from the list of calibration speeds (see below).
•
Factory Reset
. Use this to reapply the default list of calibration speeds.
new calibration factor =
indicated speed
actual speed x old calibration factor
i
D1
1235-1
Transducers Found
DST
Raymarine
Serial no.175417
Press OK to select
Press OK to continue
Speed Calibration
1
2
3
4
5
6
7
8
0.5 Kts
1.5 Kts
2.8 Kts
4.8 Kts
10.6 Kts
80 Kts
D1
1383-1
87099_1.book Page 50 Thursday, March 12, 2009 10:18 AM
Содержание ST70 Instrument
Страница 1: ...www raymarine com ST70 Document reference 87099 1 Date January 2009 Installation Guide ...
Страница 6: ...vi ...
Страница 10: ...x ST70 Installation Guide ...
Страница 20: ...10 ST70 User Reference Manual ...
Страница 28: ...18 ST70 User Reference Manual ...
Страница 64: ...54 ST70 User Reference Manual ...
Страница 70: ...60 ...
Страница 72: ...62 ...