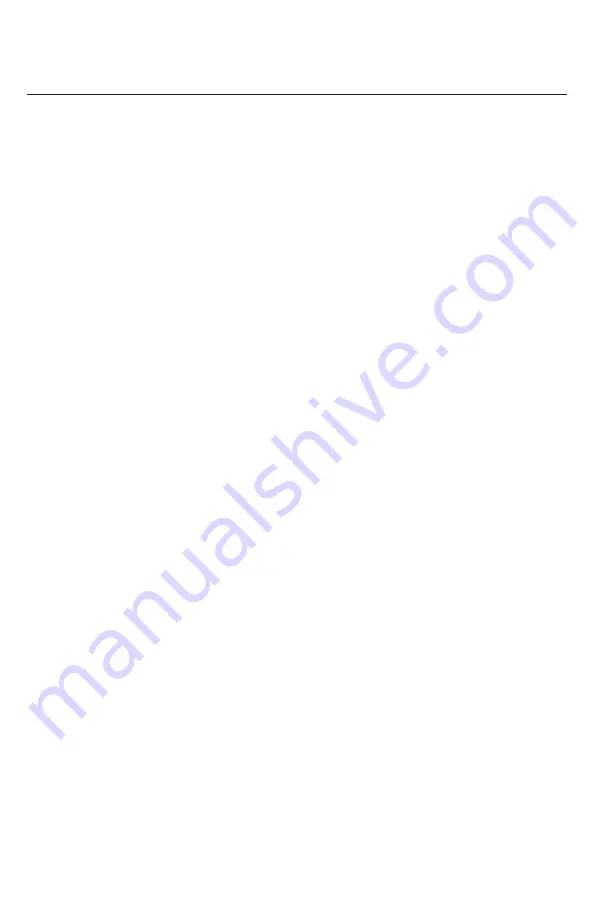
RG27/35/37 Operation • Service • Maintenance
800.392.2686
23
Safety
Precautions for Welding on FRAME
with ENGINE/MACHINE Electronic
Control Unit (ECU)
Important: ALWAYS disconnect Electronic Control Unit (ECU)
connectors and engine control system-to-machine ground
before welding on engine or machine.
High currents or electrostatic discharge in electronic
components from welding may cause permanent damage
Safety Decals
The safety decals located on this machine contain useful
and important information which will help you to operate
your machine safely. The complete decal kit and location of
each decal is given in the “Parts” manual. For your protection,
familiarize yourself with each label until you completely
understand the warning intended. Do not violate any such
warnings!
Keep all decals in place and in good condition:
• Use soap and water to keep decals clean. DO NOT
use mineral spirits, abrasive cleaners or other similar
cleaners which will damage the decals.
• Replace any damaged or missing decals. Before
attaching decals, the surface temperature of the metal
must be at least 40 degrees. The metal should also be
clean and dry before attaching the decal.
• If a machine component to which a decal is attached is
replaced, be sure to replace the decal as well.
• Replacement decals may be purchased from Rayco Mfg
or your Rayco dealer.
LOCK-Out / Tag-Out Guidelines
Always practice lock out tag out procedures when working
on this machine.
Locking and tagging out equipment safeguards those working
on the equipment from being injured by its unexpected
energized or releasing stored energy. This section summarizes
the applicable requirements for lockout/ tag out procedures,
and its intent to comply with OSHA regulations.
Lock Out Procedure
• All affected persons are to be notified that the equipment
will be off and locked out.
• All energy sources for the equipment should be identified.
• The equipment shall be shut off or otherwise deenergized,
being careful to de-energize all energy sources. This
includes all valves, switches, breakers, or other controls
that supplies energy to the equipment. In case of
mechanical energy, a block may be used to stop the
release of stored energy.
• A lock is to be placed on each energy source disconnect
or energy release block.
1. The lock is to be placed directly on the equipment if
provided with an integral locking device.
2. If there is no integral lockout device on the equipment,
securely attach an independently manufactured lockout
device on the equipment and then place the lock on the
lockout device.
3. If none of the above are possible, use the tag out
procedure.
• A tag to be secured to the lock indicating that the
equipment is not to be energized and who owns the lock.
• It should be safely tested and verified that the lockout
does prevent the release of energy.
Tag Out Procedure
• This procedure is to be used only if it is not reasonable
to use the lockout procedure.
• All affected persons are to be notified that the equipment
will be shut off and tagged out.
• All energy sources for the equipment should be identified.
• The equipment shall be shut off or otherwise de-
energized, being careful to de-energize all energy
sources. This includes all valves, switches, breakers, or
other controls that supplies energy to the equipment.
incase of mechanical energy, a block may be used to
stop the release of stored energy.
• Securely place a tag on each energy source disconnect
or energy release block.
Removal Procedure
• Lockout/tag out equipment must be removed by the
worker who placed it.
• Before the removal of a lockout/tag out the following
must be completed:
1. Removal of all non essential items.
2. Check to see that all workers and bystanders are
located in a safe position.
3. Inform all affected personnel.
• If a worker who applied the lockout/tag out is not present,
and his supervisor deems it necessary to energize the
equipment, the following must be done by the supervisor.
1. Make all reasonable effort to contact the worker who
placed the tag.
2. Determine the purpose of the lockout/tag out, and
whether it is safe to operate the equipment in its current
condition.
3. Remove all non essential items.
Содержание Super Jr RG27
Страница 47: ...RG27 35 37 Operation Service Maintenance 800 392 2686 47 Maintenance Notes ...
Страница 50: ...RG27 35 37 Operation Service Maintenance 50 Wiring Schematic ...
Страница 51: ...RG27 35 37 Operation Service Maintenance 800 392 2686 51 Wiring Schematic ...
Страница 54: ...RG27 35 37 Operation Service Maintenance 54 Hydraulic Schematic RG37 802846 RF T T P P ...
Страница 56: ...RG27 35 37 Operation Service Maintenance 56 Specifications SERVICING TAPER BUSHINGS ...
Страница 63: ...RG27 35 37 Operation Service Maintenance 800 392 2686 63 ...