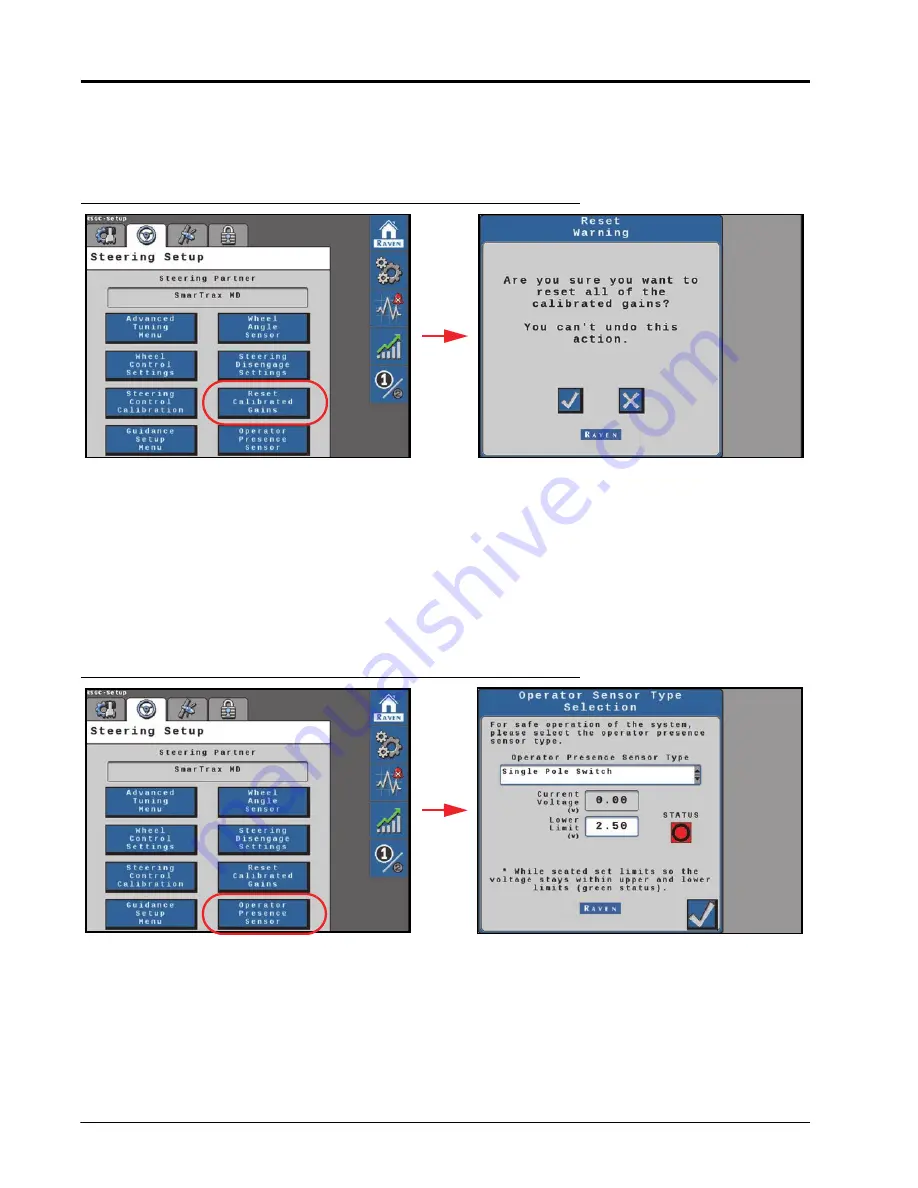
CHAPTER 5
48
Raven SC1™/TC1™ (software version 1.5) Calibration & Operation Manual for Tractors and Sprayers
3. Select the Accept button in the lower, right corner of the page to return to the Steering Setup tab.
RESET CALIBRATED GAINS
FIGURE 19. Reset Calibrated Gains Page
To reset the SC1/TC1 system to factory defaults:
1. From the SC1/TC1 Home page, select the Settings Menu button.
2. Select the Steering Setup tab and the Reset Calibrated Gains button.
3. Review the warning prompt and select the Accept button to reset the SC1/TC1 to a factory condition. Select the
Cancel button to keep the current system configuration and return to the Steering Setup tab.
OPERATOR PRESENCE SENSOR
FIGURE 20. Steering Disengage Settings Page
SENSOR TYPE
Use the drop down list to select the type of switch used to detect the presence of the operator while the system is
engaged.
• Single Pole
• Double Pole
• CAN Switch
Содержание SC1
Страница 8: ...CHAPTER 1 4 Raven SC1 TC1 Calibration Operation Manual for Tractors and Sprayers ...
Страница 28: ...CHAPTER 3 24 Raven SC1 TC1 software version 1 5 Calibration Operation Manual for Tractors and Sprayers ...
Страница 54: ...CHAPTER 5 50 Raven SC1 TC1 software version 1 5 Calibration Operation Manual for Tractors and Sprayers ...
Страница 66: ...CHAPTER 6 62 Raven SC1 TC1 Calibration Operation Manual for Towed Implements ...
Страница 98: ...CHAPTER 9 94 Raven SC1 TC1 Calibration Operation Manual for Towed Implements ...
Страница 104: ...CHAPTER 10 100 Raven SC1 TC1 software version 1 5 Calibration Operation Manual for Tractors and Sprayers ...
Страница 108: ...Index 104 Raven SC1 TC1 software version 1 5 Calibration Operation Manual for Tractors and Sprayers ...