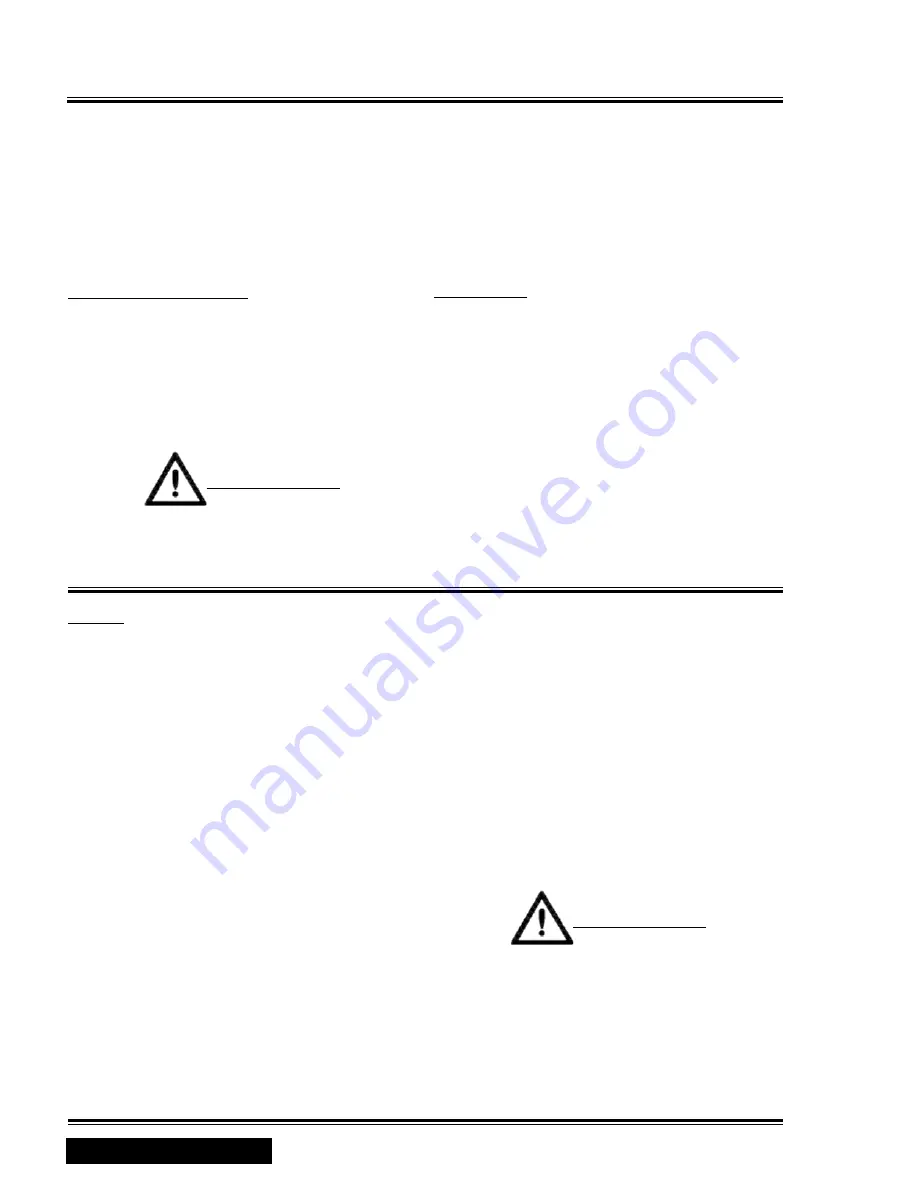
Section V - Integrated Dryer (option)
• General Information
• Inspection
• Safety
• Installation
• Start-up & Operation
• Maintenance
• Automatic Drains
General Information
The Quincy Air Drying System is designed
to cool and remove moisture from
compressed air. When properly installed,
the unit requires little maintenance or
adjustments.
Warning!
DO NOT install, operate, maintain,
adjust or service this unit without
thoroughly reading this manual.
Inspection
Inspect equipment. Any concealed
shipping damage must be reported to the
carrier immediately. Damage claims should
be filed by the consignee with the carrier.
Safety
When using air compressors and
compressed air accessories, basic safety
rules and precautions must always be
followed, including the following:
1) Read all instructions fully.
2) Wiring, breakers and other electrical
equipment must conform to local
and national electrical codes.
Do not operate this unit with
damaged wiring or after the unit
or air handling parts have been
dropped or damaged in any manner.
Notify authorized service facility
for examination, repair or other
adjustments.
3) Use suitable parts & accessories. Do
not use air pressurized accessories or
parts in the air system not suitable for
the maximum air pressure.
4) Release air pressure slowly. Fast
moving air will stir up dust and
debris, which may be harmful.
Release air pressure slowly when
depressurizing your system to avoid
bodily injury.
5) Secure drain lines. Fasten drain lines
to floor or drain. Pressurized air may
periodically pass through drain lines,
which will cause an unsecured line to
whip and may cause bodily injury.
Warning!
Air from the compressor and from
Quincy Air Drying System, as equipped,
is not safe for human respiration
(breathing).
24
Quincy Compressor-QGB
™
Back to Table of Contents
Содержание QGB 20
Страница 2: ......
Страница 35: ...Section V Integrated Dryer option Flow Diagram Quincy Compressor QGB 31 Back to Table of Contents...
Страница 88: ...Appendix A Dimensional Drawings QGB 20 25 30 84 Quincy Compressor QGB Back to Table of Contents...
Страница 89: ...Appendix A Dimensional Drawings QGB 40 50 60 Quincy Compressor QGB 85 Back to Table of Contents...
Страница 99: ......