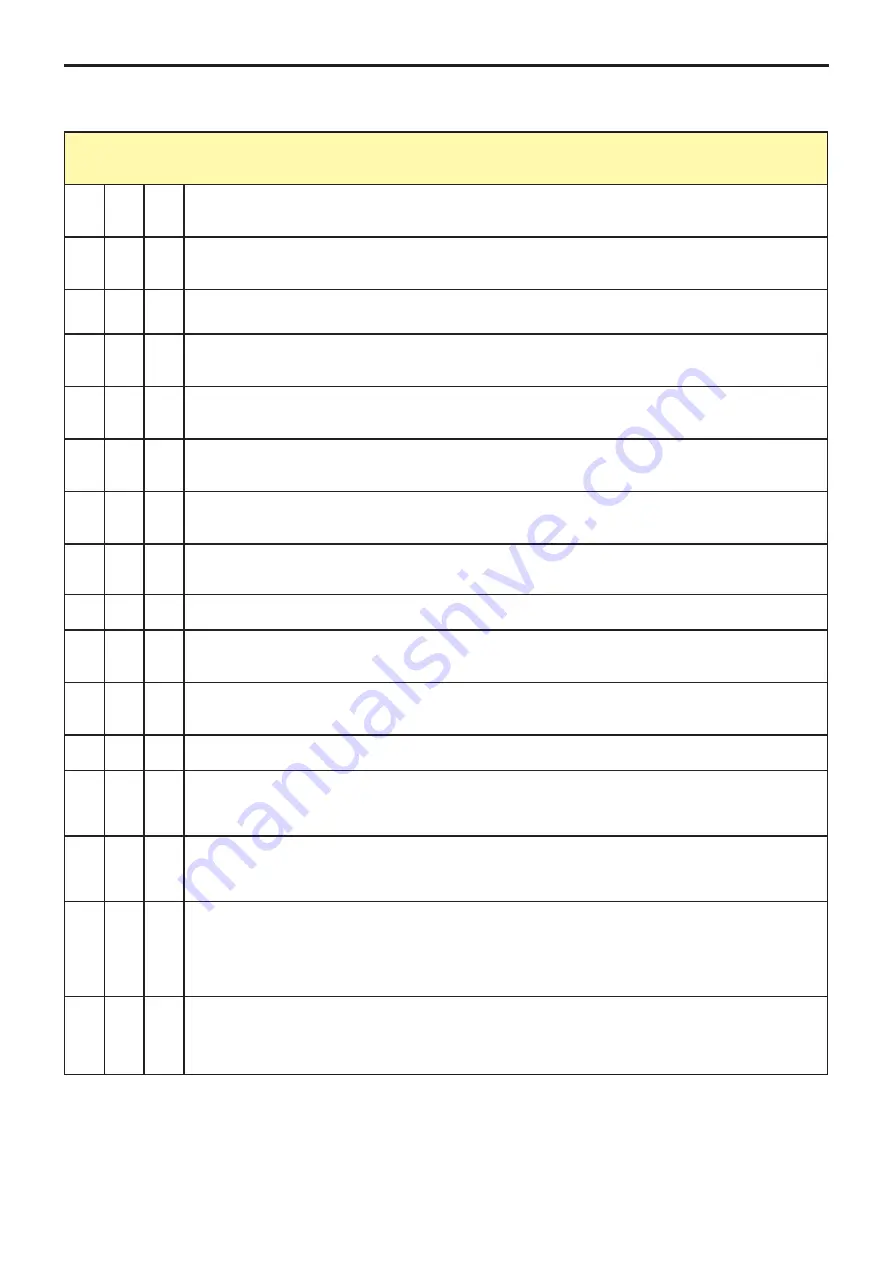
26/28
NT 1004-C00 03 18 SLC12 i - SLC18 i - SLC12 i HT - SLC18 i HT e
14. TROUBLESHOOTING
ZERO OR INSUFFICIENT FLOW
1
PRELIMINARY CHECKS
1-1
Make sure that the plastic plugs have been taken away from the ports of the pump and that the pump is
running (defective drive, damaged motor, etc., faulty transmission : broken coupling, sliding belt, worn or
poorly coupled clutch, etc.).
1-2
Make sure that the pump rotates in the correct direction corresponding to the direction in which the liquid
circulates in the installation (cf. the pump plate). If necessary, change the electric motor connections.
1-3
Make sure that the pump rotation speed is sufficient. Determine this by checking the speed of the pump
motor (see motor plate) and the speed reduction ratio (see reduction gearbox plate) or use a rev. counter.
If these checks do not highlight the problem :
2
MEASURE THE DISCHARGE PRESSURE
(as close to the outlet of the pump as possible, with a mini-
mum distance of 5 pipe diameters).
2-1
If the pressure is lower than the figures given for the material, or null, this could be due to :
2-1-1 The pump is worn, this will also affect the suction capacity of the pump (cf 3-2-2 b).
3
MEASURING THE VACUUM PRESSURE
(as close as possible to the pump inlet, inlet side).
3-1
If the vacuum is high, e.g. higher than or equal to 6 to 7 metres WC (0.6 to 0.7 bara i.e. about 45 or
50 cm of mercury), this can result in pump noise. The cause could be :
3-1-1
a. the suction lift is too high (reduce it by taking the pump down closer to the level of the liquid).
b. the dynamic suction losses are too high : the inlet piping orifice is too close to the bottom of the tank.
3-1-2 The inlet piping is completely blocked (valve, tap, filter, cloth, full seal forgotten, etc.)
3-1-3
The liquid vapour pressure is too high (or has become too high following, for example, a change of tem-
perature). Bring the pump closer to the level of the liquid, install the pump closer to the feed or cool the
liquid to reduce the vapour pressure.
3-2
If the vacuum is low, for example, less than 3 metres WC (i.e. about 20 cm of mercury), check for leaks
on the inlet pipe, isolate the pump from the inlet piping (by closing the valve nearest the pump or by inser-
ting a full flange seal) and measuring the vacuum once again.
3-2-1
If the vacuum is high with the isolating valve closed on suction line, e.g. higher than or equal to 6 or 7
metres WC (i.e. about 45 to 50 cm of mercury), the pump is not the cause :
a. there must be an air inlet upstream of the pump isolating valve.
b. the liquid vapour pressure is or has become too elevated due to a change of temperature (cf 3-1-3).
3-2-2
If the vacuum is low or non-existent, the reason could be :
a. air is entering the pump (check the front cover seals, flanges, etc...)
b. the pump is worn and the internal tightness is out of specification (the piston bushings are worn, worn
piston and cylinder, broken piston wear compensation springs, worn partition, broken shaft).