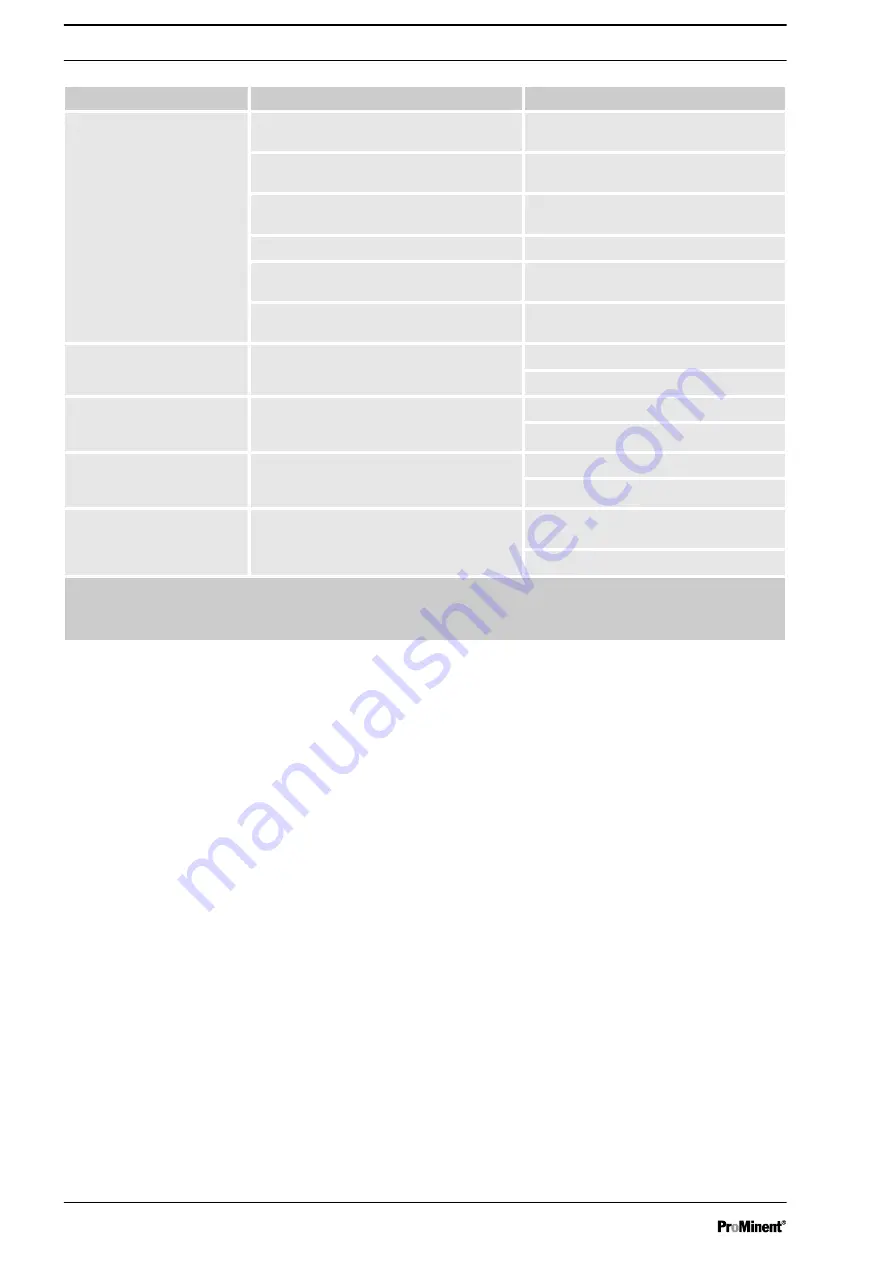
Fault
Possible cause
Remedy
Control failure, no control signal
Ensure correct control signal through
measurement
Cable for control is loose or incorrectly con‐
nected
Check connector and, if required, rewire
the signal cable
Stroke rate or stroke length set to "0"
Set the stroke rate / stroke length to the
desired value
Pump is set to standby mode or pause
Check the control or pause signal
Faulty operation of the pump/metering
system
Train operating staff
Electrical connection malfunctioning
Check the contacts for corrosion and
secure fixing
Display on the pressure
manometer pulsates
Pulsation damper pre-load is incorrect
Check the setting of the pulsation damper
Retrofit pulsation damper if necessary
Discharge line displays
strong vibrations or starts
"pulsating'
Pressure peaks too high
Check the setting of the pulsation damper
Retrofit pulsation damper if necessary
Suction line displays strong
vibrations or starts "pulsa‐
ting'
Pressure peaks too high
Check the setting of the pulsation damper
Retrofit pulsation damper if necessary
Fluid is leaking from the
backplate of the metering
pump
Liquid end not tight
Tighten the screws on the dosing head
crosswise to the correct tightening torque
Replace diaphragm/sealing set
The table does not claim to be complete.
Further reasons for failure and detailed information on the causes of faults can be found in the operating instructions
for the individual components.
Maintenance and Troubleshooting
38