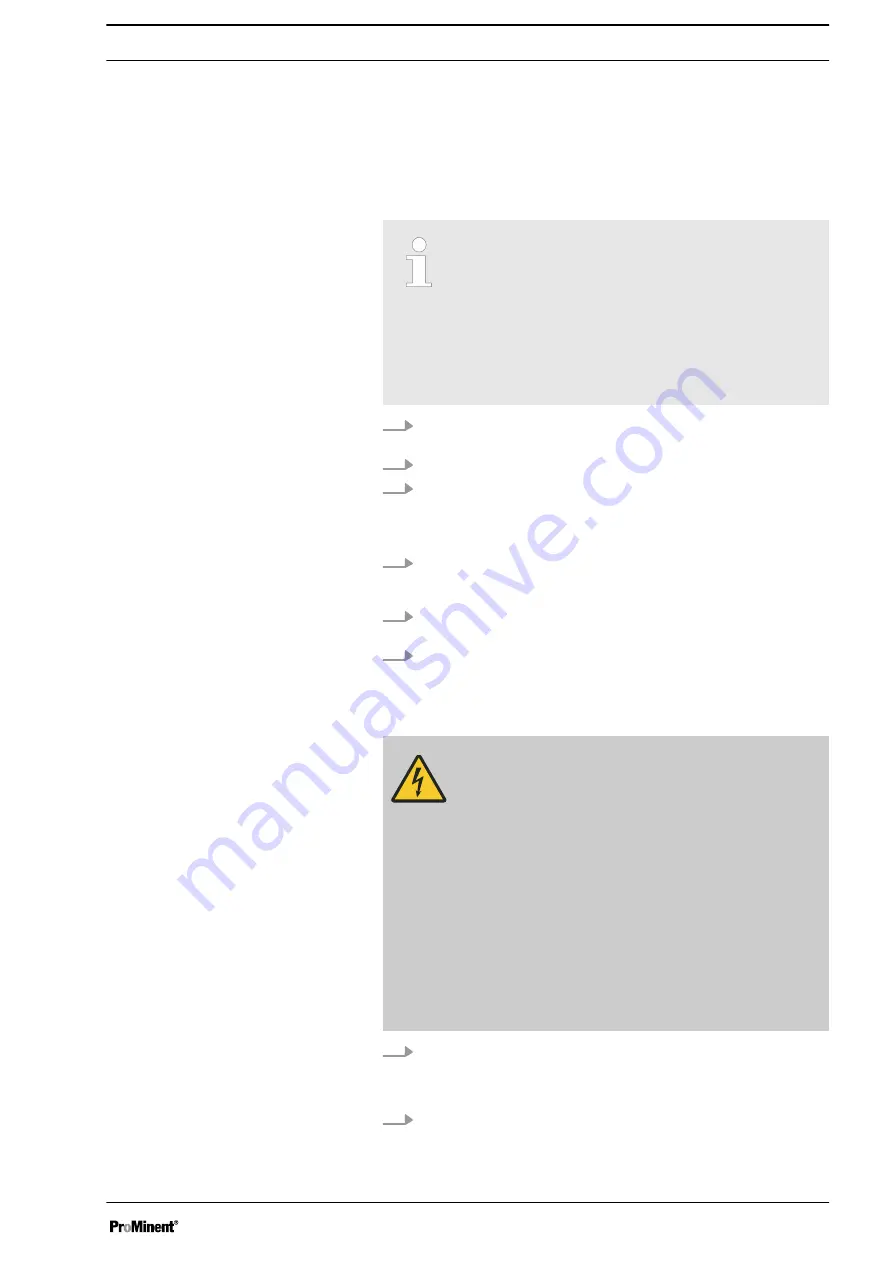
4
Assembly and installation
n
User qualification, mechanical installation: trained and qualified per‐
Chapter 2.1 ‘User qualification’ on page 21
n
User qualification, electrical installation: electrical technician,
Chapter 2.1 ‘User qualification’ on page 21
Intended use
The metering system is designed for installation indoors.
Operation outdoors is not permitted.
Do not operate the metering system under conditions
other than those described in the technical data.
Only allow adequately qualified and technically expert
personnel to operate the metering system.
All other uses or modifications are prohibited.
1.
Only fix the metering system on the feet intended for this purpose or
as a wall panel on the wall.
2.
Ensure that the fixing surface is level (e.g. DIN 18202).
3.
Tighten all connectors (threaded connectors, flange connectors ...).
1.
When installing the metering system, always make sure that the
connectors on site are connected to the metering system free of
tension.
2.
Only use materials that comply with the provisions and specifica‐
tions of the ProMinent resistance list.
3.
Only use adhesives approved for your application to bond the pipes.
If in doubt, contact the adhesives’ manufacturer.
WARNING!
Live parts
Cause: All work or installation work performed can lead
to danger from electrical current.
Possible consequence: Fatal or very serious injuries.
Measure: Carry out all work in line with the applicable
national and international statutory regulations, laws and
standards. The system operator is responsible for com‐
pliance and implementation.
We fundamentally recommend the use of appropriate
residual current circuit breakers (RCCB) or other
residual current devices (RCD) providing they can be
installed sensibly and professionally within the electrical
installation. Please adhere to all national standards and
regulations.
1.
The transition point for the electrical system is a terminal box
attached on the wall mounting plate with a master switch, to which
all signals and the power supply to the pumps and the power supply
to the controller are connected.
2.
Connect the metering system in accordance with the terminal dia‐
gram supplied to the on site electrical installation.
Installation work:
Hydraulic installation:
Electrical installation:
Assembly and installation
27