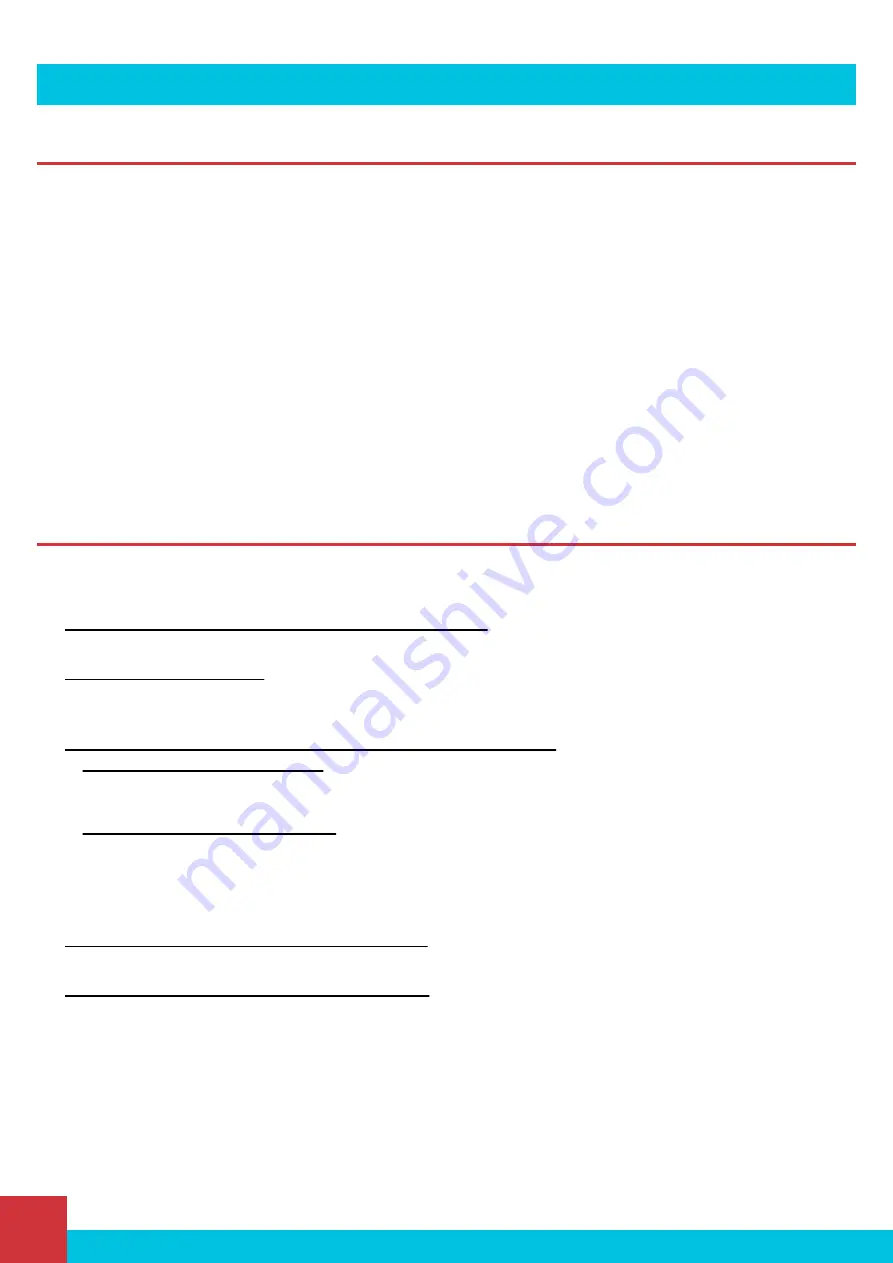
P a g e | 3
Progressive Automations – Position Control Communication Protocol
1. Before Use
1.1 Introduction
Please carefully read through this manual before using our product for proper operation and to prevent any unexpected
damage.
Progressive Automations’ Micro Precision Actuators have been developed to provide reliable, high-quality linear solutions
in a compact size. Our Micro Precision Actuators can be applied in various fields such as factory automation, medical
devices, robotics, professional UAV, and radio control applications.
Features:
▪
Position Control (Positional Accuracy 50~90um – see spec chart of each model)
▪
Embedded Drive circuit
▪
4096 Step High Resolution
▪
High-Performance Coreless Motor
▪
Minimal Mechanical Backlash (30um)
▪
Excellent Substitute for pneumatic cylinders which do not support position control
1.2. Safety
Please read our safety instructions below for operating our Micro Precision Actuators. Warranty will be void if products
have been abused, altered, or tampered with in any way.
1. DO NOT press the rod when the actuator is being operated.
Constantly applying a load that is higher than the rated
force capacity may damage and burn out the motor.
2. Apply proper input voltage.
Use a power supply or battery that has an output voltage within the proper range. For
instance, apply 4.0~7.4V for 7.4V input products and 7.0~12V for 12V input products. The motor may burn out when
12V is applied to our 7.4V input products.
3. Product lifespan may vary based on the load applied, duty cycle, etc.
1)
Usage below rated force capacity.
For instance, the rated force of our PA-12-10645012R is 4.50lbs. Using the
PA-12-10645012R in applications that experience force conditions below 4.50lbs will maximize the product lifespan.
The lower the applied load, the longer the motor lifespan.
2)
Usage below 50% Duty Cycle rating
: If the motor operates continuously without any interval (rest), the motor will
be overloaded the and overload protection feature will cut off power to the actuator motor. Therefore, it is important to
consider the 50% duty cycle when using in your application. For example, a 20-minute period with a 50% duty cycle
means that the motor must be off for, at least, 10 minutes and on for, no more than, 10 minutes to ensure it does not
overheat. Usage below a 50% duty cycle will optimize lifespan. The lower the duty cycle, the longer the lifespan.
4. Make sure not to damage the actuator motor case.
Installing your own brackets to fix the actuator on your system
may risk dissipation and cause overheating.
5. Set position commands within the mechanical limit
: The application should allow the actuator rod to have a full
mechanical range of motion to reach the stroke limits without running into physical obstructions. Make sure the
positional commands are made within the application’s mechanical limit. If the positional command is out of the
application’s mechanical limit, the actuator will be overloaded at certain points in time and power will be cut off to
protect the actuator due to the overload protection feature. If overload protection is inactivated by the user, the motor
will not be protected. When considering precise position control, make sure to double-check this step before fully
integrating the actuator.