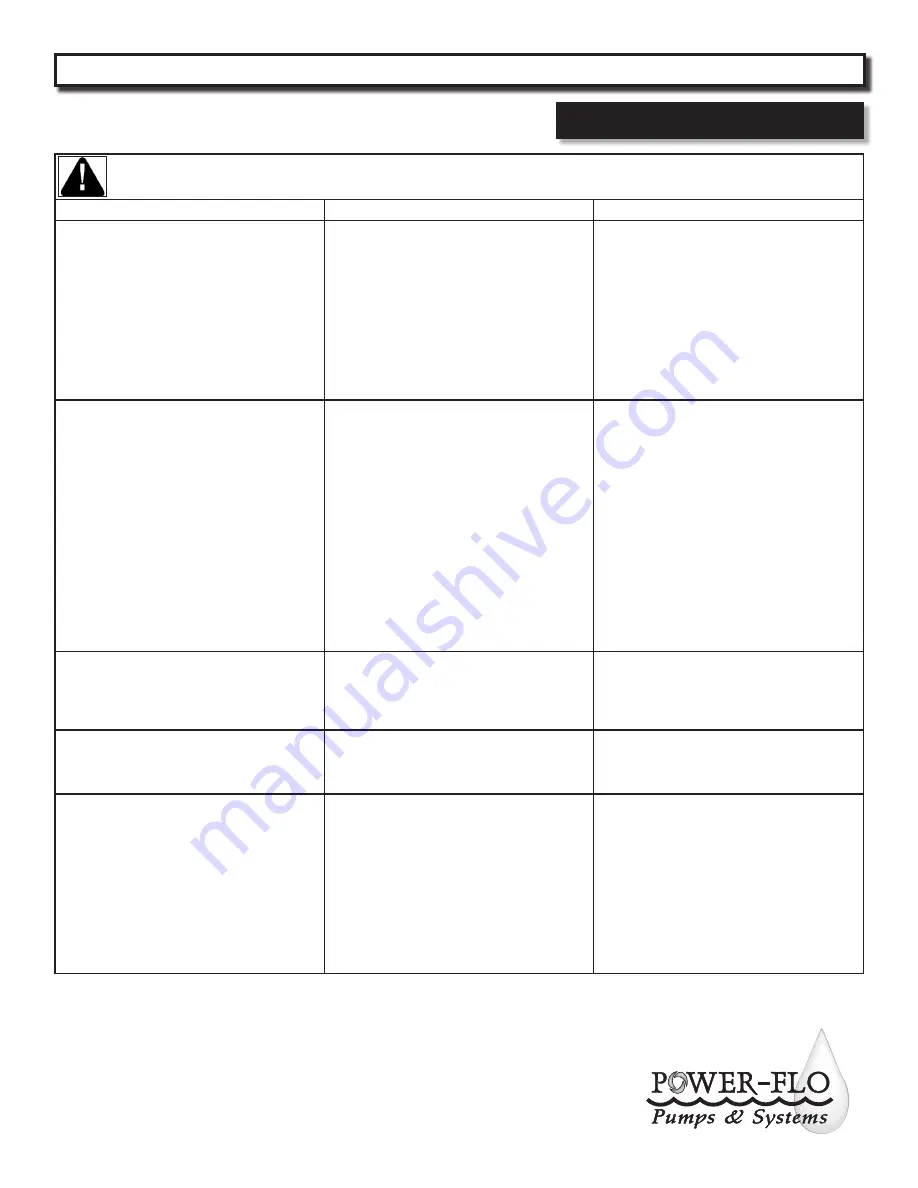
Power-Flo Pumps & Systems • 877-24PUMPS • www.powerflopumps.com
11
Risk of electric shock. Always disconnect the pump from the power source before handling inspections or repairs.
Symptom
Possible Cause(s)
Corrective Action
Pump will not run
Blown fuse or other interruption of
power; improper voltage.
Switch is unable to move to the “turn ON” position
due to interference with the side of basin or other
obstruction
Insufficient liquid level
Defective level control
Check that the unit is securely plugged in. Have an
electrican check all wiring for proper connections
and adequate voltage and capacity.
Position the pump or switch so that it has adequate
clearance for free operation.
Make sure the liquid level is allowed to rise enough
to activate level control(s).
Remove and replace level controls
Pump will not turn off
Discharge is blocked or restricted
Check valve is stuck closed or installed backwards
Gate or ball valve is closed
Total lift is beyond pump’s capability
Pump impeller is jammed or volute casing is pluged
Check the discharge line for foreign material,
including ice if discharge line passes through or
into cold areas
Remove check valve(s) and examine for freedom of
operation and proper installation
Open gate or ball valve
Try to route piping to a lower level.
If not possible, a larger pump may be required.
Consult the factory
Disconnect unit electrically. Remove the pump
from the basin. Detach the pump base and clean
the area around the impeller. Rotate impeller by
hand. Reassemble and reinstall
Pump will not turn off
Level control(s) unable to move to the “turn OFF”
position due to interference with the side of basin
or other obstacle
Defective level control
Posistion the pump or level control so that it has
adequate clearance for free operation
Remove and replace level control
Pump runs periodically when fixtures are not in use
Check valve is stuck open or is leaking
Fixtures are leaking
Remove check valve(s) and examine for freedom of
operation and proper installation
Repair fixtures as required to eliminate leakage
Pump operates noisily
Debris in the impeller cavity
Damaged impeller
Worn bearings
Piping attachments to building are too rigid
Remove the pump from the basin.
Detach the pump base and clean the area around
the impeller. Reassemble and reinstall
Consult the factory for information regarding
replacement of impeller
Return pump to the factory or authorized repair
station for repair
Replace a portion of the discharge line with rubber
hose or connector
NOTE:
Power-Flo Pumps & Systems assumes no responsibility for damage or injury due to disassembly in the field. Disassembly of the pumps or supplied
accessories other than at Power-Flo Pumps & Systems or its authorized service centers, automatically voids warranty.
Trouble Shooting Chart
PFS411HTCE-2
Submersible Effluent, Sump & Sewage Pumps