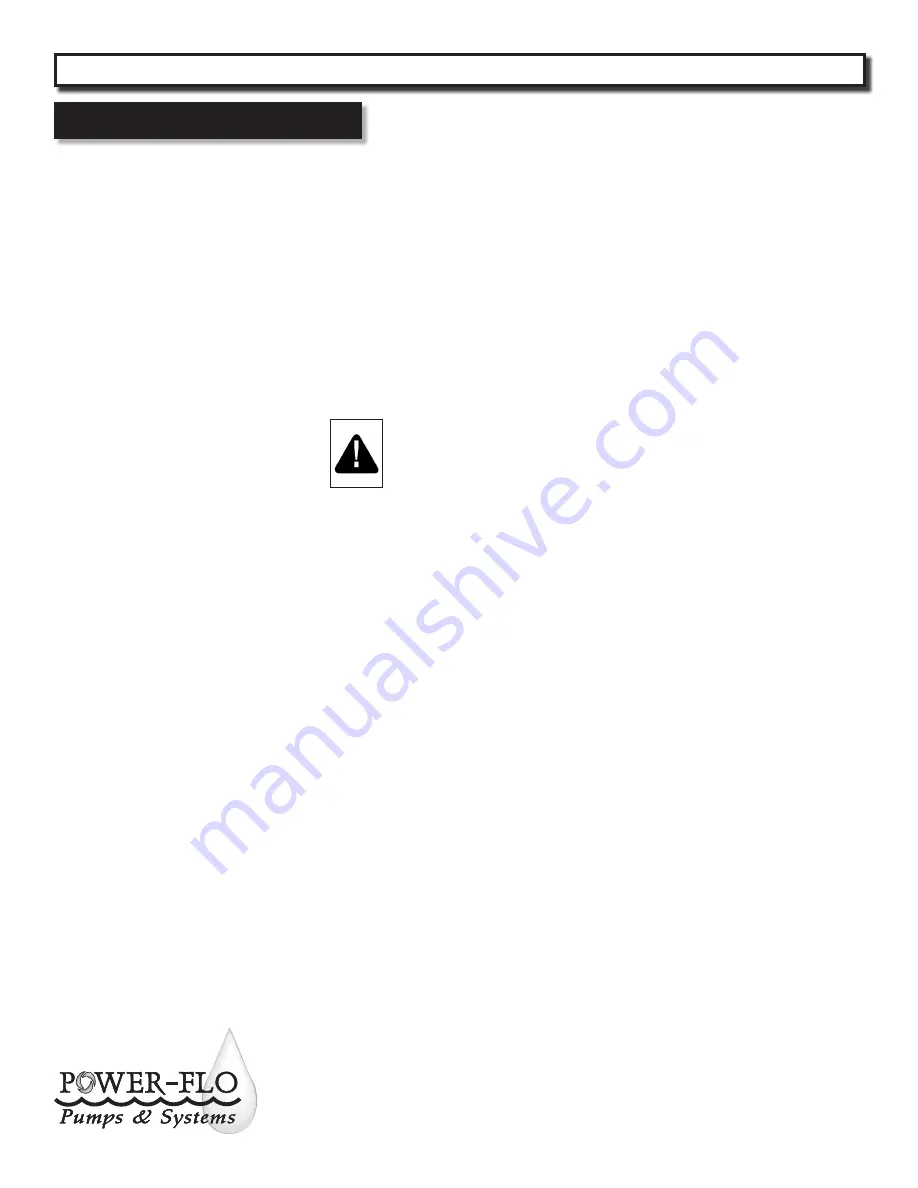
Power-Flo Pumps & Systems • 877-24PUMPS • www.powerflopumps.com
6
The installation should be at a sufficient
depth to ensure that all plumbing is
below the frost line. If this is not feasible,
remove the check valve and size the
basin to accommodate the additional
backflow volume.
Discharge Piping
Discharge piping should be as short
as possible and sized no smaller than
the pump discharge.
Do not reduce
the discharge pipe size below that
which is provided on the pump.
Both
a check valve and a shut-off valve are
recommended for each pump. The
check valve is used to prevent backflow
into the sump. The shut-off valve is
used to manually stop system flow
during pump servicing.
Electrical Connections
Power cable:
The power cable mounted to the pump
must not be modified in any way except
for shortening to a specific application.
Any splice between the pump and the
control panel must be made in
accordance with the electric codes. It is
recommended that a junction box, if used,
be mounted outside the sump or be of
at a minimum Nema 4 construction if
located within the wet well.
DO NOT USE
THE POWER CABLE TO LIFT PUMP.
Always rely upon a Certified Electrician
for installation.
Overload Protection:
Single Phase
- The stator in-winding
overload protector used is referred to
as an inherent overheating protector
and operates on the combined effect of
temperature and current.
This means that the overload protector
will trip out and shut the pump off if the
windings become too hot, or the
load current passing through them
becomes too high.
IMPORTANT ! -
The overload will then
automatically reset and start the pump
up after the motor cools to a safe
temperature. In the event of an overload,
the source of this condition should be
determined and corrected immediately.
WARNING! - DO NOT LET
THE PUMP CYCLE OR RUN IF
AN OVERLOAD CONDITION
OCCURS !
Wire Size:
If longer power cable is required consult
a qualified electrician for proper wire
size.
Pre-Operation
1. Check Voltage and Phase
Compare the voltage and phase
information stamped on the pump
name plate.
2.
Check Pump Rotation
- Improper
motor rotation can result in poor
pump performance and can damage
the motor and/or pump. Incorrect
rotation for Single-Phase pumps is
unlikely. If the rotation is incorrect
contact factory.
3.
Name Plate
- Record the information
from the pump name plate to
drawing in front of manual for future
reference.
4.
Insulation Test
- An insulation
(megger) test should be performed
on the motor. Before the pump is put
into service. The resistance values
(ohms) as well as the voltage (volts)
and current (amps) should be
recorded.
5.
Pump-Down Test
- Be sure pump
has been properly wired, lowered into
the basin, sump or lift station, check
the system by filling with liquid and
allowing the pump to operate through
its pumping cycle. The time needed to
empty the system, or pump-down
time along with the volume of water,
should be recorded.
Maintenance
No lubrication or maintenance is required.
Perform the following checks when pump
is removed from operation or when pump
performance deteriorates:
a). Inspect motor chamber for oil level
and contamination.
b). Inspect impeller and body for
excessive build-up or clogging.
c). Inspect motor and bearings.
d). Inspect seal for wear or leakage.
Servicing
NOTE: Item numbers in ( ) refer to Figure 5.
Cooling Oil -
Anytime the pump is
removed from operation, the cooling oil
in the motor housing should be checked
visually for oil level and contamination.
To check oil, set unit upright. Remove pipe
plug from housing or remove capscrews
(21), washers (22) and remove upper
motor housing (17), do not damage o-ring
(9). With a flashlight, visually inspect the
oil in the housing to make sure it is clean
and clear, light amber in color and free
from suspended particles. Milky white oil
indicates the presence of water. Oil level
should be just above the motor when
pump is in vertical position.
Installation & Service
PFS411HTCE-2
Submersible Effluent, Sump & Sewage Pumps