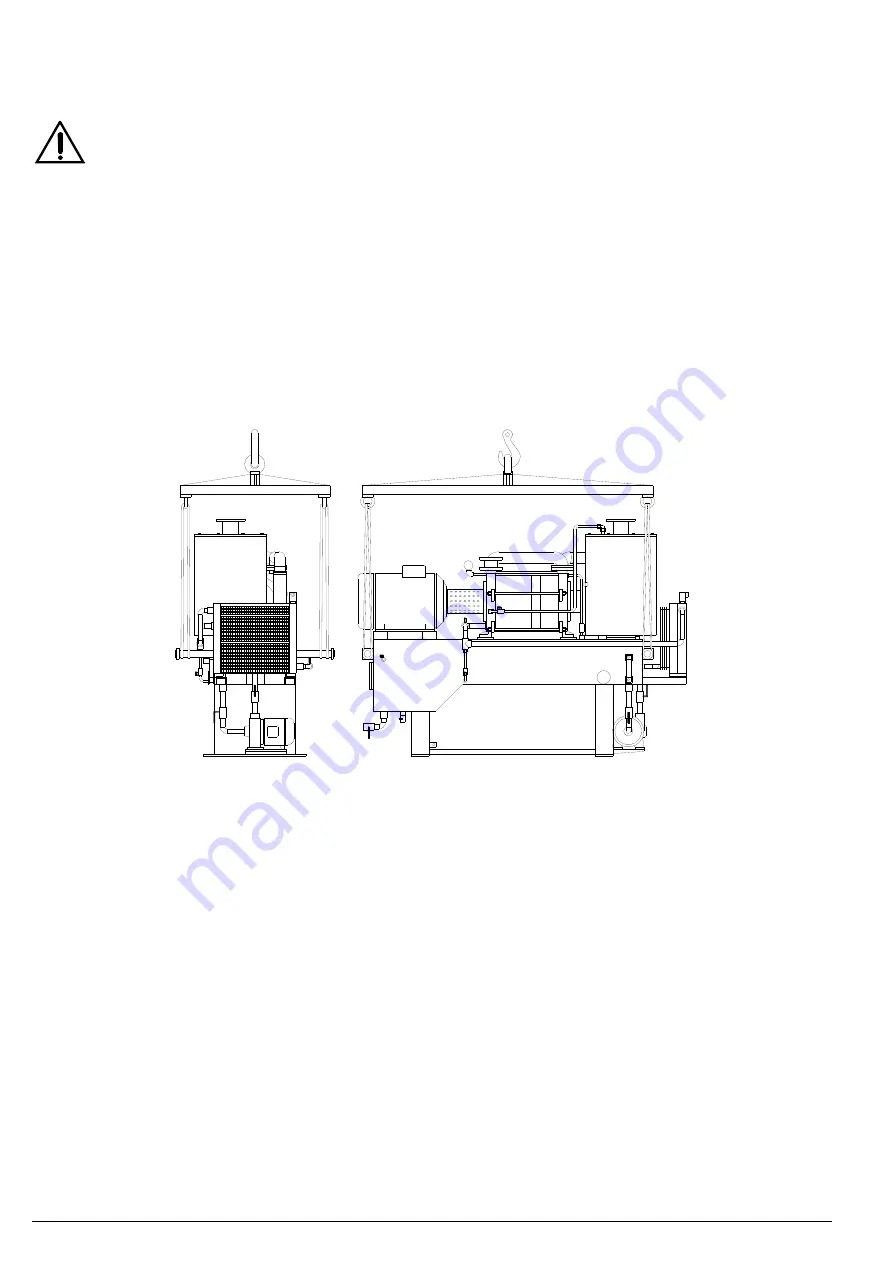
Operating manual liquid ring vacuum pumps and compressors series TRH - TRS - TRM - TRV - SA & Systems type HYDROSYS - OILSYS
46
21.1
– LIFTING AND MOVING OF OILSYS SYSTEMS
DANGER!
Danger due to overturning or crushing. The Oilsys systems must ALWAYS be handled and lifted and moved
in horizontal position and without any oil in the tank.
For a safe lifting it is necessary use only ropes or belts positioned on metal bars that were previously inserted
in the lifting holes present on the base (see fig. 48) and handle it carefully to avoid damages to the system or
harm to the operators.
The bars diameter MUST NOT BE MORE than 5 mm smaller than the diameter of the lifting holes on the
base.
During handling always use appropriate protective devices.
The bars diameter must not be more than 5 mm smaller than the diameter of the lifting holes on the base.
The lifting bars, after having been inserted in the lifting holes, must be blocked at both ends to avoid the withdraw of the
rope or of the bars itself.
For the lifting with ropes or belts use only a balance beam to have a traction upright to the ground.
NOTE:
The eyebolts intended for the lifting of a single component of the system MUST NOT be used to lift the entire
pump system.
For further information and clarifications ask our Sales Office.
Fig. 48