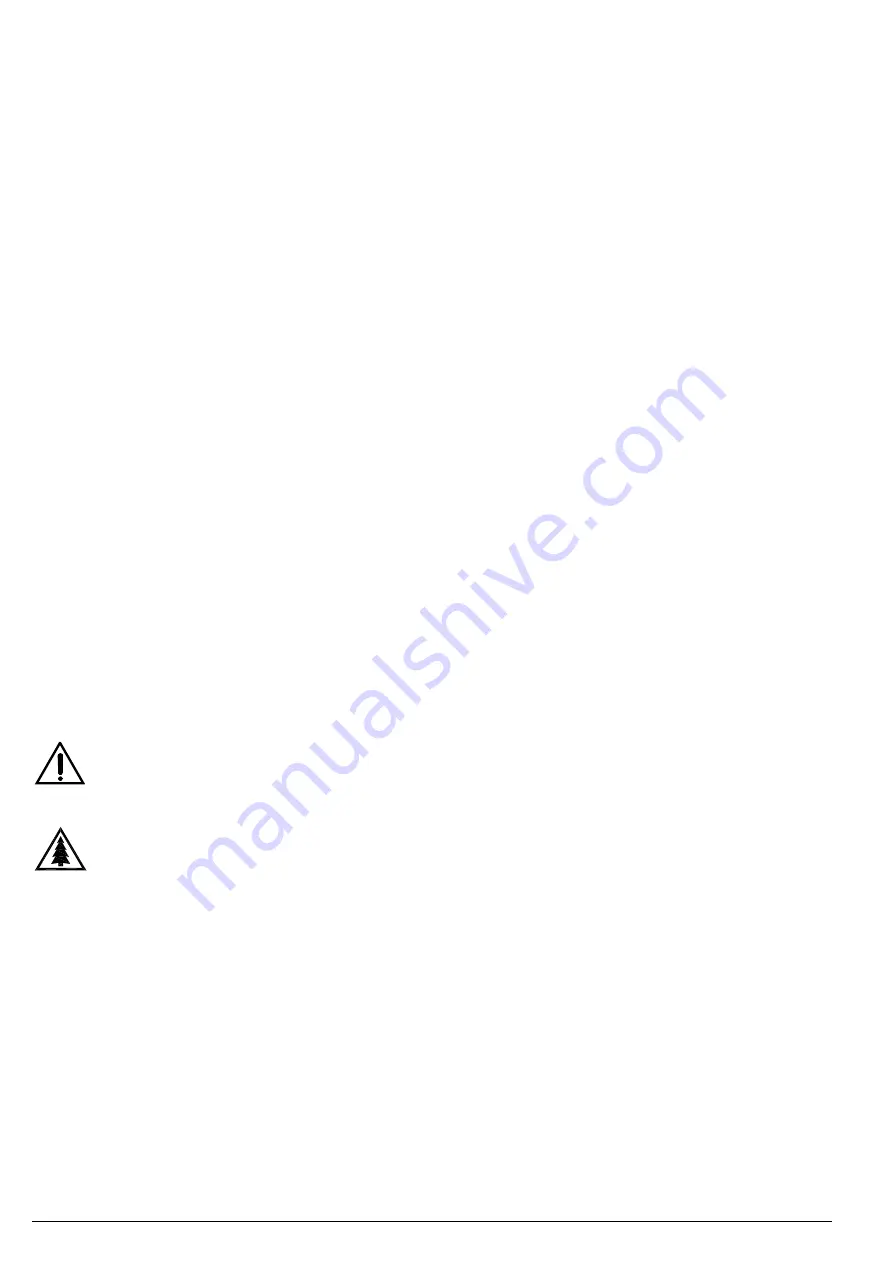
Operating manual liquid ring vacuum pumps and compressors series TRH - TRS - TRM - TRV - SA & Systems type HYDROSYS - OILSYS
30
This is a damaging condition for the impellers, port plates and casings. The cavitation causes erosion taking away metal
particles and attacking the surface of the pump components. This is particularly damaging if the pump is handling
corrosive gases, see chapter 16 for suggestions to correct the problem.
Pump series TRH, TRM and TRV are designed for the application of an anti-cavitation valve that should be left open (if
required) see fig. 11 and 12 for the location. This valve should be connected toward the upper part of the discharge
separator so that, depending upon the operating vacuum, the pump can either take air or discharge excessive liquid.
For OILSYS systems the anti-cavitation valve ITEM 13H is piped from pump ITEM 4 to the frame separator ITEM 1B.
During operation it must be avoided to have sudden and frequent variations from high to low vacuum. (e.g.: suddenly
opening the suction valve when the pump is operating at pressures lower than 200 mbar).
This would flood the pump creating high power absorption that would put heavy stress on the motor and coupling.
Particular attention should be put on the quantity of the service liquid flow. The flow will depend upon the type of
installation (see chapter 7), the pump size, and/or the desired temperature rise.
The flow of service water at 15°C, for standard pumps and normal operating conditions at various vacuum levels, is
listed on the specific pump curves and/or on tab. 2 of chapter 7.7
.
Usually the temperature rise of service water, when handling dry air at 20
°C
, is approximately 4°C.
When condensable (e.g.: vapours) are present in the gas stream the heat load to be removed by the service water will
be higher, therefore the service water temperature rise will be higher.
The service liquid flow and its temperature will affect the pump performance.
Generally the low service liquid flow will decrease the pump capacity, while a high service liquid flow will increase the
absorbed power by flooding the pump (see chapter 19 for information and calculations).
Hard service water will generate limestone build-up inside the pump. The severity of the deposit will vary with the water
temperature. Limestone or mineral deposits on the surface of the internal pump components will cause an increase of
absorbed power, wear of the components and possiblely will seize the pump.
It is recommended to monitor the water hardness and, if too high (>18°F), treat the water. If there are no alternatives,
there should be periodical flushing of the pump with a solution that will remove the specific deposits, or the pump must
be periodically disassembled, cleaned of all incrustations and re-assembled.
Systems with total service liquid recovery require periodical change of the service liquid contained in the closed loop.
The heat exchanger must be kept well cleaned of all mineral deposits for an effective thermodynamic heat exchange.
During operation, a closed loop system will loose some of the service liquid, due to evaporation and/or saturation of the
discharged gases. It will be required to periodically make-up fresh liquid into the system.
This operation is not required for those systems that are fitted with a float type automatic make-up valve ITEM 8. This
valve requires water at a pressure of approximately 1 bar.
Systems that handle condensable will experience a rise in the level of the service liquid in the separator. The excessive
liquid will be overflowed through the overflow valve or connection.
If the specific gravity of the condensable is higher than that of the service liquid, the condensable must be discharged
through the separator drain valve ITEM 11, preferably with system not running.
12.1 -
“OILSYS” SYSTEMS
CAUTION!
Possible contact with warm media and warm surfaces. Operate only provided with apposite protective
devices.
(For ITEM numbers refer to fig. 29 and legend of chapter 21).
In case of systems OILSYS series, as service liquid, mineral oil is used which, if dropped on the ground, is
greatly polluting and dangerous for the environment: therefore high and constant care to possible leaks and, if
the case, provide immediately to dispose the leaks in conformity with the laws into force.
It is very important to keep the service oil temperature under control; when the oil temperature exceeds 90°C there is
the danger of seizing the pump and the gasketing may start leaking.
Every 100/200 working hours it is suggested to check the oil level in the frame reservoir ITEM 1B, make-up oil if
necessary and change the oil every 4000/6000 working hours (depending upon the use and the application): take care
of its possible disposal according to the laws into force and to a safe local environment management.
Those installations where the handled gases are contaminated with dust or suspended solids that can alter the oil
characteristics will require more frequent oil check and changes.
The frame is fitted with two inspection ports ITEM 43 which can be used for cleaning the frame reservoir after it has
been
drained of all the oil.
Condensable, if present during evacuation, can be flushed right through the discharge of the separator (if they have low
boiling point) or, when the system is idle, can be drained by opening valves ITEM 13F and/or 13L.
During the service, the oil demister filter will be impregnated with oil particles; the pressure gauge ITEM 14 installed at
the housing ITEM 1C will provide an indication of the filter being plugged; pressure reading over 0.3 bar is an indication
that the filter needs replacement.
At higher discharge pressures the discharged air quality will decrease and the vacuum pump absorbed power will
increase.
The oil separated by the filter is accumulated at the bottom of the filter cartridge.
To remove this oil there is a scavenger line with a regulating valve ITEM 13G that is connected to the vacuum pump
suction flange. It is recommended to keep this valve ITEM 13G minimally opened.