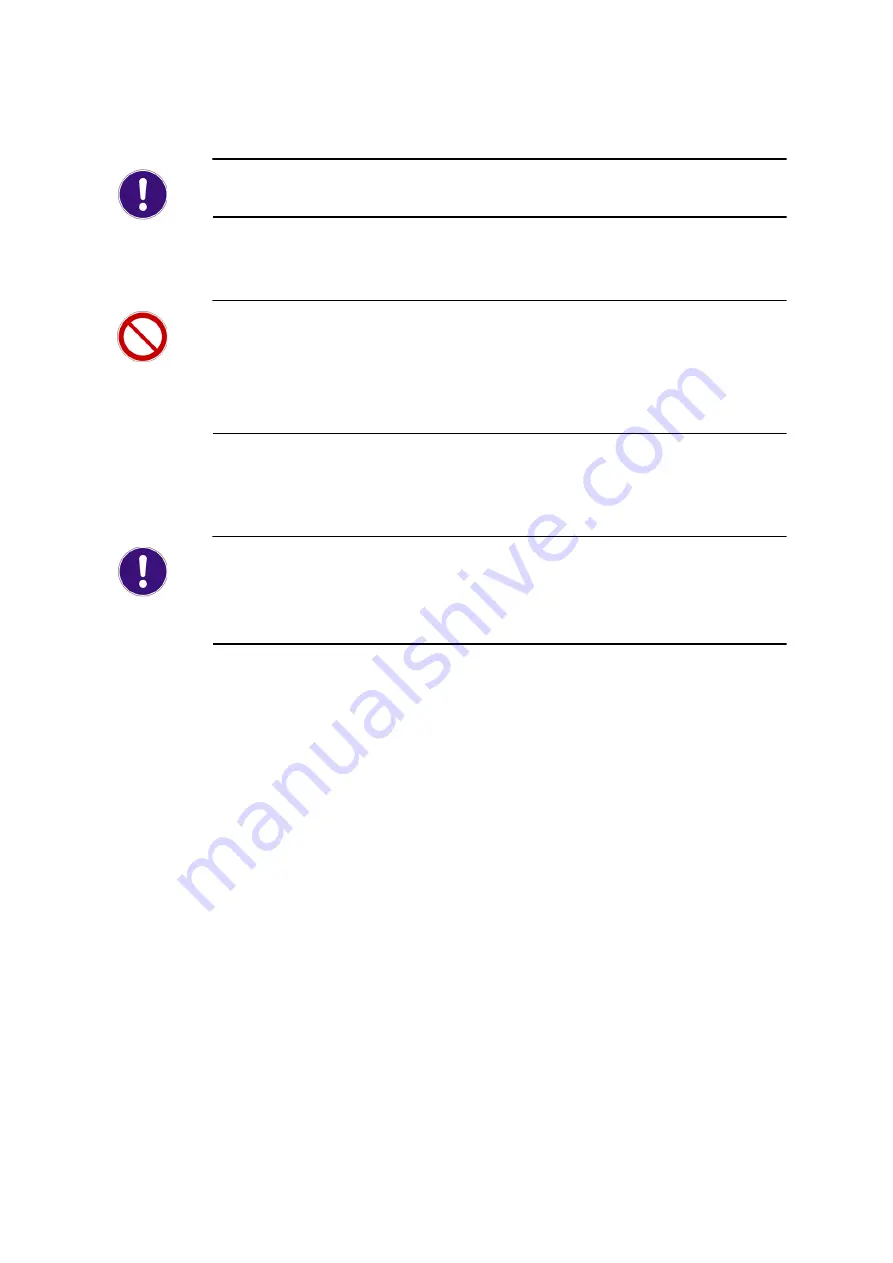
4-2
4 Making Measurements
7. Start the data acquisition as described in your software manual.
NOTE!
Before working with laser light, read the information on laser safety in
1.2 !
8. Open the beam shutter on the front of the scanning head.
The laser beam is now emitted from the scanning head.
WARNING!
Danger of injury caused by laser light !
Do not look directly into the laser beam !
Do not use any reflective tools, watches etc. when you are working in the beam path of the
laser !
Wear suitable laser adjustment eyewear when you have to look at the target area of the laser
beam long and hard to set it up !
Measure
9. Data acquisition is now fully controlled by the software. Once the laser
has warmed up you can setup the software, set the optics, define scan
points and make measurements as described in your software manual.
NOTE!
The instrument does not reach its optimal metrological properties until a warm-up period of
approx. 30 minutes. For measurement tasks with high angular stability requirements we
recommend a warm-up period of 120 minutes. This applies especially when you are working
with imported 3D geometries.
4.2
Selecting Suitable Settings
4.2.1
Measurement Range
The available measurement ranges depend on the bandwidth set. For this
reason, first select the bandwidth. Thus, the list of the available measurement
ranges is updated. Select your measurement range depending on the
expected maximum velocity. The available measurement ranges are given in
the specifications (refer to
Many applications are covered by the 100 mm / s measurement range.
Therefore, this measurement range should be selected for initial
measurements with the system. Use the smallest possible measurement
range to minimize the noise and to maximize the optical sensitivity.
If either the positive or the negative limit of a measurement range is reached,
the Overrange of the measurement range is displayed in the software. Then
select the next highest measurement range. However, note that this
Overrange display can also be activated by very brief overloading which is
caused by noise spikes. In such cases, the velocity measurement range can
be maintained as long as it is suitable for the amplitude of the wanted signal.
Observe the signal in the time domain to obtain information about this.
Содержание PSV-500
Страница 10: ...1 6 1 Safety Information...
Страница 14: ...2 4 2 Introduction...
Страница 50: ...4 8 4 Making Measurements...
Страница 104: ...C 2 C Declaration of Conformity...