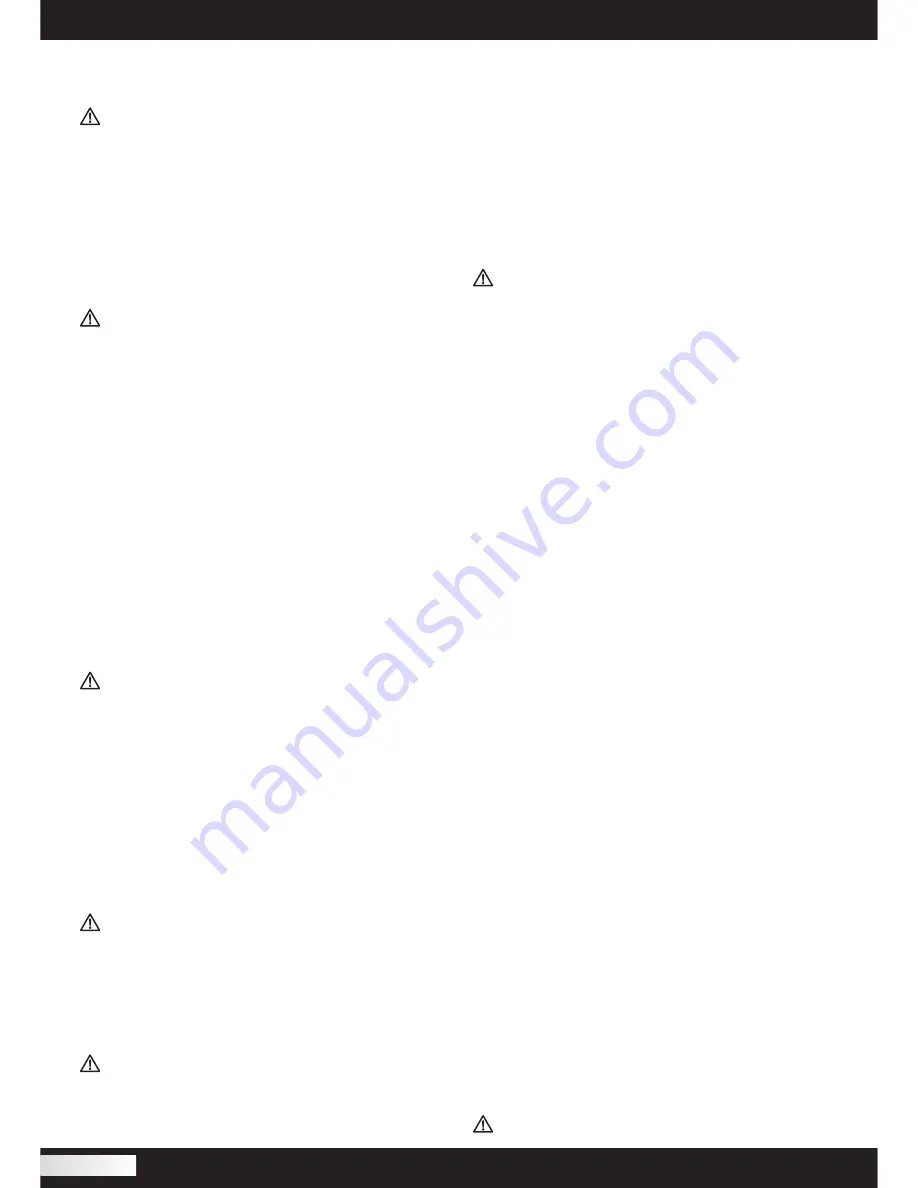
14
ENGLISH
you can use also oil: Shell advance gear SAE 10 W 40 API GL-3 or an
oil with 10W40 viscosity compatible with clutch (similar to motorcycle
engine oil)
WARNING:
Do not throw spent oil into the environment.
Dispose of it correctly through authorized collection points.
9.4- STARTER ROPE REPLACEMENT (Flash Starter)
Remove the starter from the engine unscrewing the 4 screws (Photo
6).
Remove the handle rope. Be careful since the central wheel will turn
till the spring is completely discharged: keep it and discharge it slowly
to avoid damages or possible injuries. Remove the central screw and
its cover (photo 7).
ATTENTION!
Under the cover there are two teeth for the starter
jaw (check their condition and if worn replace them), under them 2
small calipers. Be very careful not to lose these small parts.
Prepare the new rope and tie a knot at the top. Remove the plastic
wheel and the old rope. Put the new rope in its hole (photo 8), wind
up the rope on the wheel (according to the entrance sense of the rope
on the wheel (Photo 9). Now insert the plastic wheel in its housing
again, and check through the hole that the internal spring hook is
perfectly coupled (Photo 10), place the springs, the teeth for the
starter jaw and screw the cover again using medium thread-locker.
All the parts in movement, including the springs, must be well
lubricated.
Now go on by charging the return spring: take the head of the rope
leaving 10-20 cm coming out the hole with “u” shape on the wheel
side. Turn the wheel three times in counter clock-wise sense till it stops
in front of the exit hole on the aluminium case. Keeping the plastic
wheel stopped, pass the rope through the case hole. Insert the handle
and the washer and tie a single knot as shown in photo 11.
ATTENTION:
verify that the return spring does not reach the end
of the stroke. Pull the rope completely and turn the wheel again to
check that it can make at least one turn before stopping.
This test is very important because the spring hasn’t been studied to
reach the end of the stroke and, if it happens, the spring will break.
Reassemble the starter in the engine and tight the 4 screws (M5) with
strength (see the tightening torque values table).
9.5- HOW TO CHECK THE COOLING SYSTEM LEVEL
Periodically check the cooling system: when the engine is cold the
coolant must reach half of the bottle. If necessary add some liquid,
using the one specific for aluminium radiator.
ATTTENTION:
never open the cap when the engine is hot, you
could burn.
9.6- HOW TO EMPTY THE COOLING SYSTEM
If necessary empty the cooling system by unscrewing the proper screw
(see photo 12) and collect the leaking liquid. Remove the cap to make
this operation easier.
ATTENTION:
Do not empty it when the engine is hot, you could
burn.
9.7- HOW TO FILL IN THE COOLING SYSTEM
Fill in the cooling system using coolant specific for aluminium radiator
till ½ of the water charging bottle. It is important to check that there
are no bubbles inside the cooling system. To proceed with this control
we suggest you should plugging, using a finger, the upper hole inside
the bottle and using the other hand pushing the pipe till the air
bubbles stop to exit.
After filing the cooling system start the engine for some minutes, then
switch it off and check the level.
9.8- ADVANCE TIMING SETTING
WARNING:
This adjustment is necessary only if the ignition is
disassembled and it must be done by qualified people only owning
the necessary tools. Screw one m.5x30 screw in the hole with thread
passing through the flywheel and lock it. Assemble the flywheel and
insert the screw in the case: the flywheel will be fixed (Photo 14).
Screw the flywheel nut without locking it so that the crankshaft can
rotate in the flywheel. Screw the dial gauge support into the spark
plug hose, insert the dial gauge and move the piston to the top dead
centre. Now reset the dial gauge and rotate the crankshaft ant-clock
wise of 1,7 mm towards the flywheel sense (see arrow in photo 15).
Once achieved the value, keep the pulley or the crankshaft stopped
using one hand and tight the flywheel nut using a key, without
exceeding. Check that the advance timing is as indicated (1,7+/-
0,1), remove the m.5x30 screw and fit the coil. Before locking it with
the 2 screws, place between coil and flywheel one 0,35 mm calibrated
shim (photo 16). Now definitely tight the flywheel nut using a torque
wrench at 40Nm.
10- HOW TO BEHAVE WHEN FLYING
Maximum acceleration is recommended only to take off (full power)
or when really necessary!
In order to avoid a poor mixture from acceleration/ascent to level
flight conditions, loosen the engine till a descending phase and then
gradually accelerate again till achieving a level flight or a glide angle
or a rise angle wished. In this way you will be sure to maintain firm
and efficient the carburation, avoiding being over rpm with a
minimum valve/throttle opening.
We remind you that two stroke engines do not stand constant range
for a long time too much. Take care of your engine by varying now
and then the rpm range. In this way the engine will have constant
performance and a good elasticity improving its working during the
time.
10.1- TEMPERATURE THERESHOLDS
Your engine is equipped with a thermocouple to read the water
temperature to which it is possible to connect a specific instrument
(928.830.003) that detects the water temperature, the rpm and the
operation hours (not supplied) (Standard operating temperatures:
min. 55°, max. 95°)
If you use the engine in cold weather conditions and the water
temperature does not reach the minimum one of 55° we suggest you
should install a thermostat with 60° opening (code 928.830.013).
ATTENTION:
The coolant pump is placed on the transmission
Содержание THOR 80
Страница 3: ...1 01 02 04 06 07 08 09 10 03 B A C 05 OIL LEVEL A B...
Страница 4: ...2 11 12 13 14 16 15...
Страница 29: ...27 FRAN AIS...