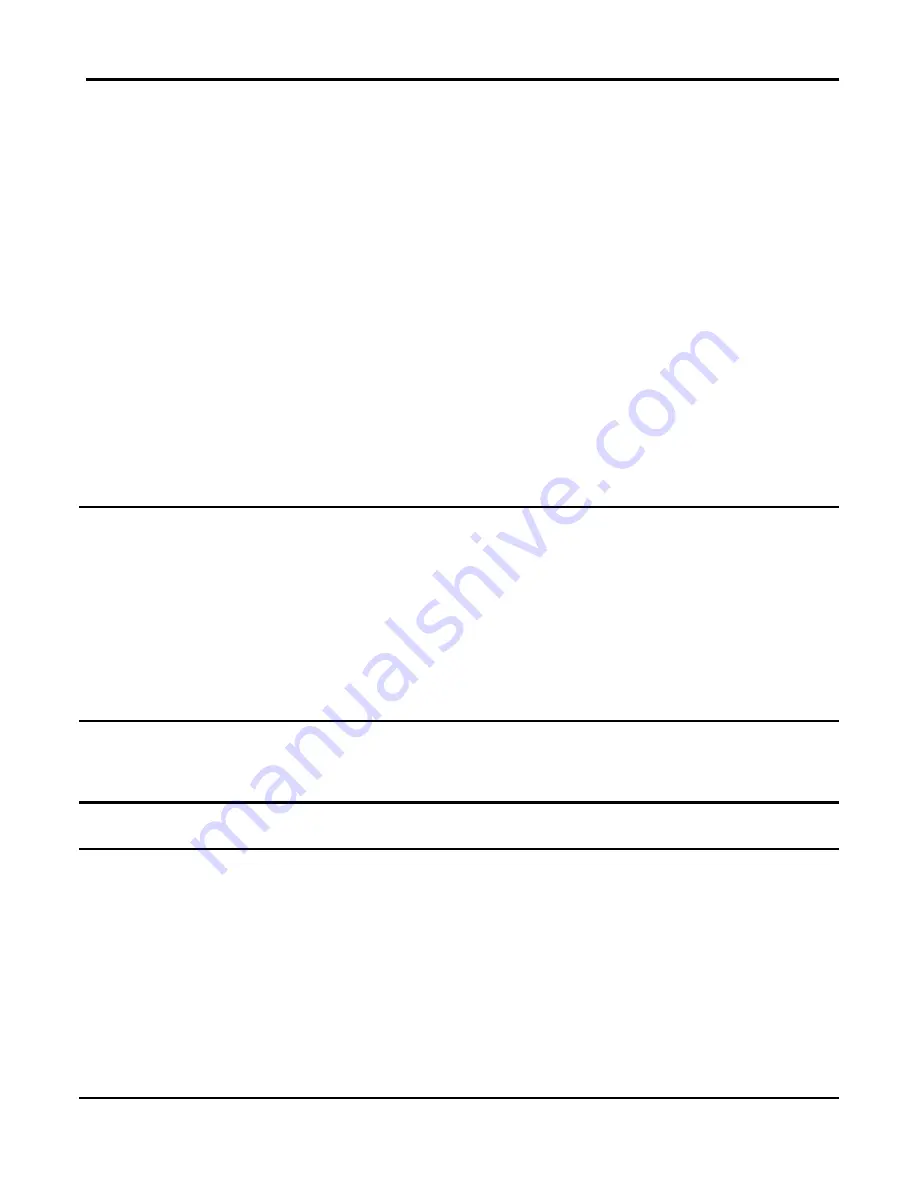
Pneumax
PTO-Driven Compressor Kit Installation Guide
Page 14 of 36
Connecting the cooler water lines and wye-strainer
The cooler water is supplied by diverting water through the wye-strainer supplied by
Pneumax from the
discharge
side of the fire pump (see the Hydraulic Schematic). The
cooling water supply hose should be 0.5” to 0.625 I.D. for the 140/200-SP to supply the
proper flow for cooling the system. The cooler discharge water may be routed back to the
booster tank fill tower or returned to the inlet side of the pump.
Normally, coolant water is returned to the booster tank and a check valve is installed in-line
to prevent backflow from the tank through the cooler and so as not to interrupt drafting
operations (A ½” check valve is supplied with the kit). However, during drafting and hydrant-
supplied operations, the booster tank may overflow because of the cooler water return. If
this is objectionable, route the return line to the inlet side of the pump. In this case, it is not
necessary to install an in-line check valve, but it will be necessary for the pump operator to
open the tank fill valve during operation to prevent overheating the fire pump.
Wye Strainer for Cooler
A wye-strainer is installed to strain water before it enters the cooler's water supply inlet. The
wye strainer is a service item and should be in an accessible location for service and/or
cleaning.
Caution: Pneumax is not responsible for damage due to plugged strainers. If the customer’s
water system contains excessive debris, or the vehicle relies on drafting for its water
supply, it may be necessary to install a larger strainer and/or a clean-out valve on the
wye-strainer.
Without good water flow through the heat exchanger, the compressor will overheat.
Compressor performance will be inadequate, and it may fail completely.
Omitting the Wye-strainer or removing the screen from the Wye does not improve
water flow. It will allow debris into the cooler, which can clog the tiny heat exchanger
tubes and restrict water flow.
Hydraulic Filter Installation
Caution: This is a one-way filter. Oil must flow in the direction indicated by the arrows on the
top of the filter.
The hydraulic filter should be mounted to the compressor cooler. This eliminates the need to
find a mounting location and simplifies the system hosing. It is best to keep the hydraulic
hose runs as short as possible, especially for the #8 lines from the sump to the filter/cooler
and to the oil inject at the compressor.
•
Make sure there is enough room so the filter can be removed and replaced.
•
Make sure the direction of oil flow is correct.
Содержание 140-SP
Страница 24: ...PTO Driven Compressor Kit Installation Guide Page 24 of 36 80 SP with 8 inch Vertical Sump Hydraulic Schematic...
Страница 28: ...PTO Driven Compressor Kit Installation Guide Page 28 of 36 Compressor Installation Angles...
Страница 29: ...PTO Driven Compressor Kit Installation Guide Page 29 of 36 Eight Inch Vertical Sump...
Страница 30: ...PTO Driven Compressor Kit Installation Guide Page 30 of 36 Ten Inch Vertical Sump...
Страница 31: ...PTO Driven Compressor Kit Installation Guide Page 31 of 36 80 P Heat Exchanger Oil cooler...
Страница 32: ...PTO Driven Compressor Kit Installation Guide Page 32 of 36 140 200 SP Heat Exchanger Oil Cooler...
Страница 33: ...PTO Driven Compressor Kit Installation Guide Page 33 of 36 80 SP Separator Filter Separator Filter...
Страница 36: ...PTO Driven Compressor Kit Installation Guide Page 36 of 36 Companion Flange Front View Side View...