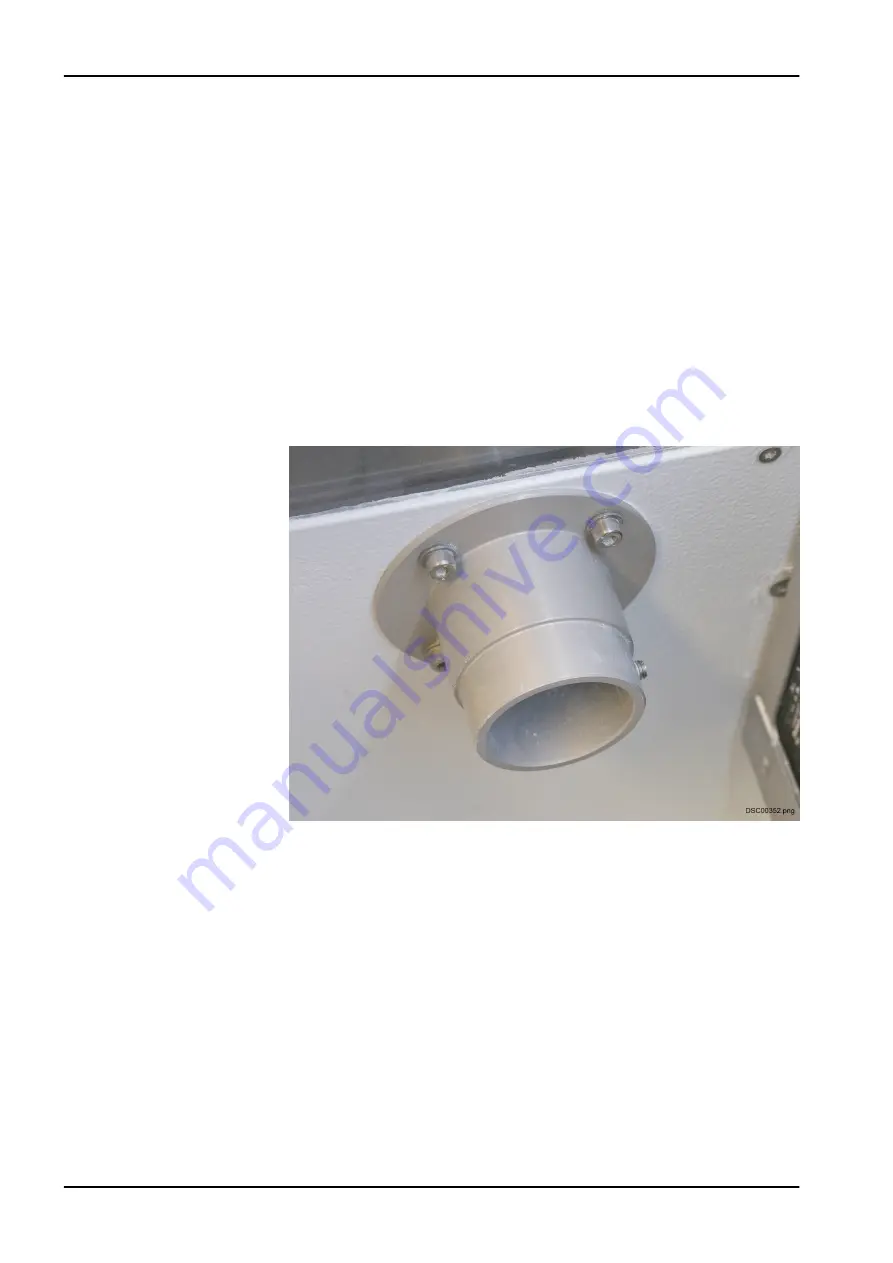
2. Set the workpiece in the adapter and check for correct seating of the
workpiece (see section "Inserting workpiece" on page 52).
3. Make sure that all necessary tools are present in the tool magazine and
in the correct position (see section "Loading tool magazine" on page 56).
4. Close the milling chamber lid.
5. Select the desired milling program from the menu by selecting
Open
milling program (see section "Touch screen commands" on page 64).
6. Start the milling process.
8.18.1 Dry milling
NOTE
Always use the suction system for dry milling.
1. Open the milling chamber lid.
2. Remove the protective cap from the extraction nozzle.
8 Operating milling unit
60 Planmeca PlanMill 50 S
User's manual
Содержание PlanMill 50 S
Страница 1: ...PlanmecaPlanMill 50S user s manual EN 30018608...
Страница 130: ......
Страница 131: ......