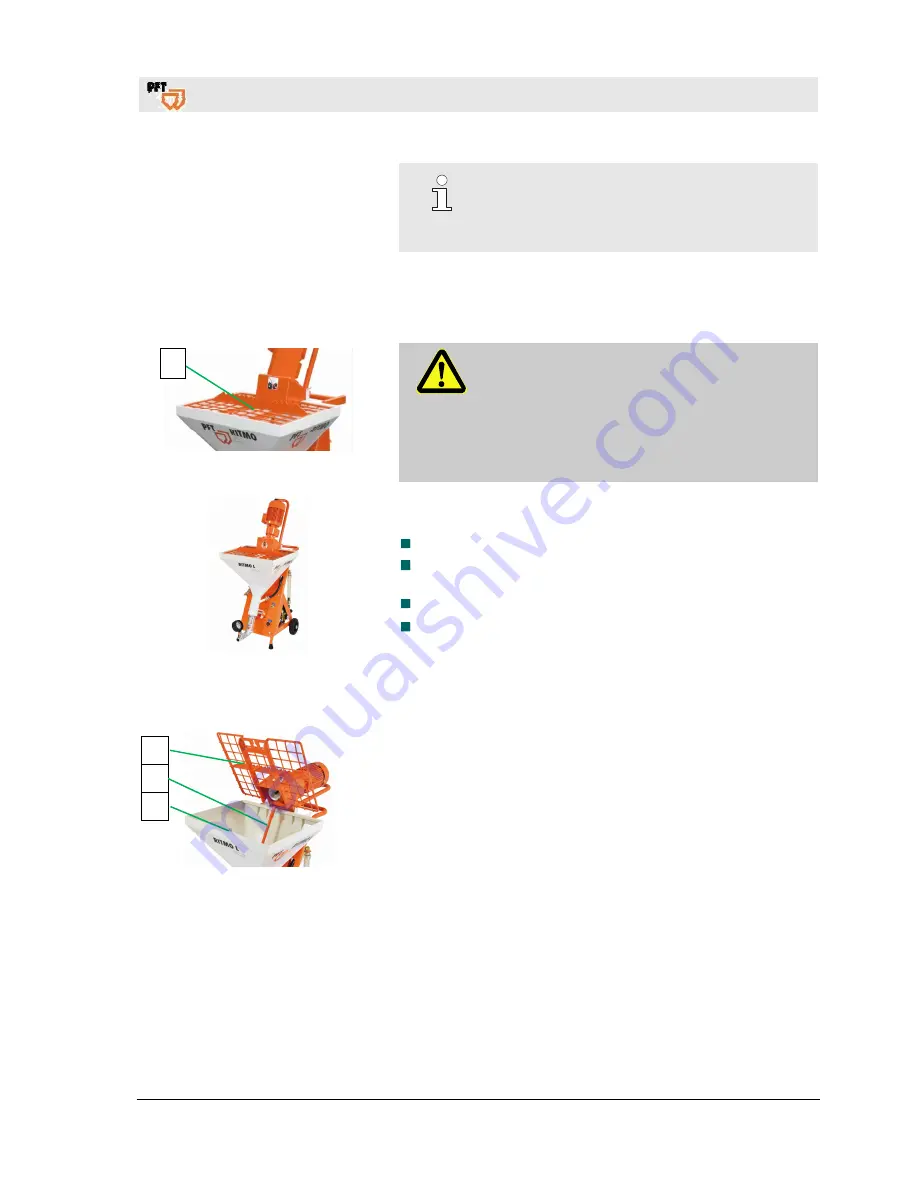
Mixing pump RITMO L Eco Overview - Operation
Preparing the machine
12 April 2019 13:43:00
31
NOTE!
Further protective equipment that is to be worn
during particular jobs will be pointed out separately
in the warning instructions of this chapter.
29 Preparing the machine
Prior to operating the machine carry out the following steps for
preparing the machine:
Fig. 31: Grille cover
DANGER!
Rotating mixing shaft!
Risk of injury when reaching into the material
hopper.
During machine preparation and operation the
grille cover (1) must not be removed.
Never reach into the running machine.
Fig. 32: Set-up
Put up the machine on a stable, even surface and secure against
unwanted movements:
Neither tilt nor roll off the machine.
Put up the machine in such a way that it cannot be hit by falling
objects.
The operating elements have to be freely accessible.
Maintain a clearance of approx. 1.5 metres around the
machine.
29.1 Open the protection grille
Fig. 33: Open the protection grille
1. Loosen nuts (1) of the protection grille.
2. Tilt the protection grille with motor (2) backwards.
3. Remove the mixing shaft (3).
4. Close the protection grille with motor (2).
5. Firmly tighten the nuts (3) of the protection grille.
1
2
3
1