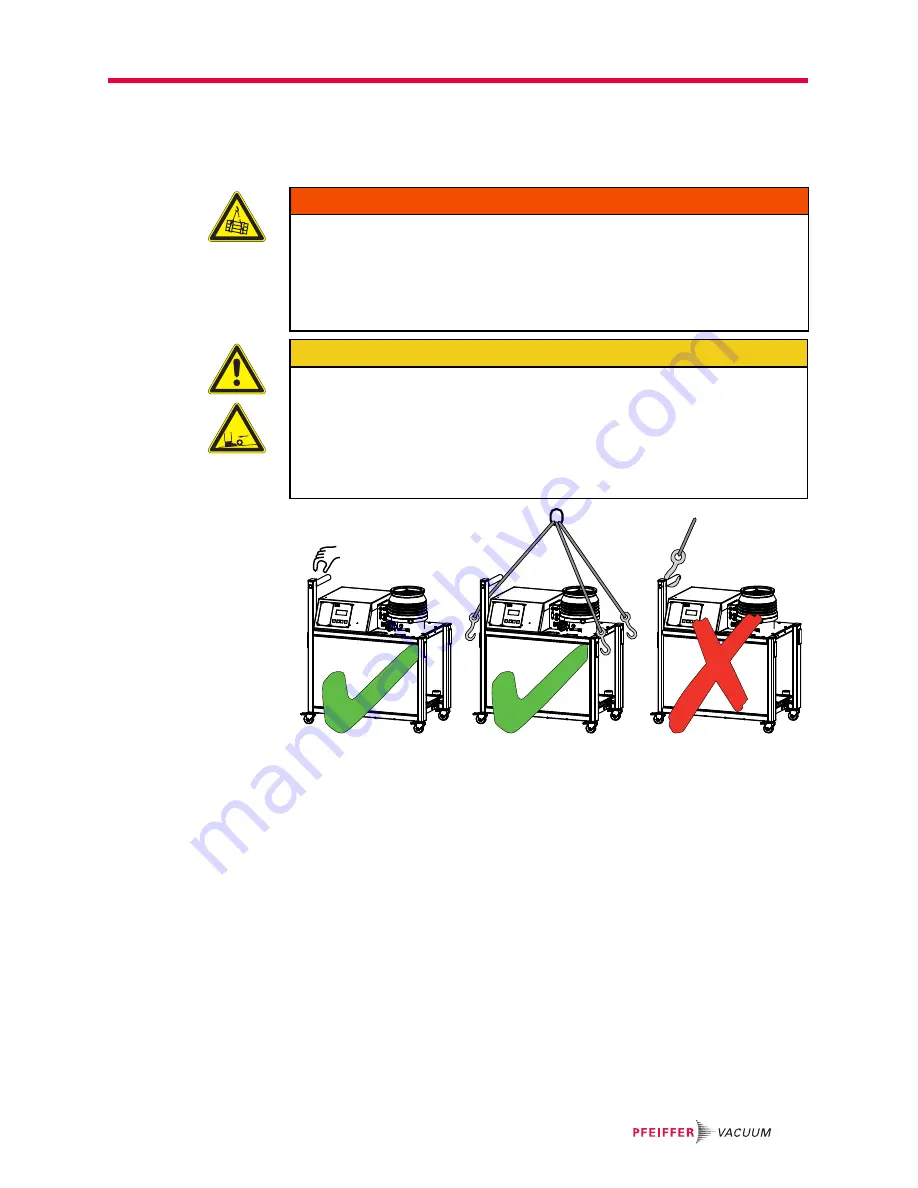
Transport and storage
9
3
Transport and storage
3.1
Transport
Always transport the pumping station uprightly and as even as possible.
Keep the original protective covers.
3.1.1
Transportation lock
The backing pump of the pumping station HiCube Pro is secured against damage during
transport .
Follow instructions concerning the installation location!
Before putting into operation loosen the backing pump's transportation lock device at
the installation location.
3.2
Storage
Close the flange openings by using the original protective covers.
Close further connection ports by using the corresponding protective covers.
Only store the pumping station indoors at an ambient temperature between -10 °C
and +40 °C.
In rooms with moist or aggressive atmospheres, the pumping station must be airproof
shrink-wrapped in a plastic bag together with a bag of dessicant.
WARNING
Danger from falling and swinging loads!
When lifting the pumping station there is a danger of falling parts.
Only fix a lifting device for transport on all provided points of the frame of the pumping
station (first remove the rubber caps).
Make sure that there are no persons under the suspended load.
Do not lift the pumping station on the handle.
CAUTION
Risk of injury due to the pumping station's tipping or rolling away
Superstructural parts provided by customer can shift the pumping station's center of
gravity, creating a risk of tipping. On inclined planes, there are general risks of tipping
and injury due to squeezing from rolling pumping stations.
Do not transport or move pumping stations with superstructural parts.
Do not transport or position a pumping station on inclined planes with a downgrade
> 5° (approx. 8.7%).