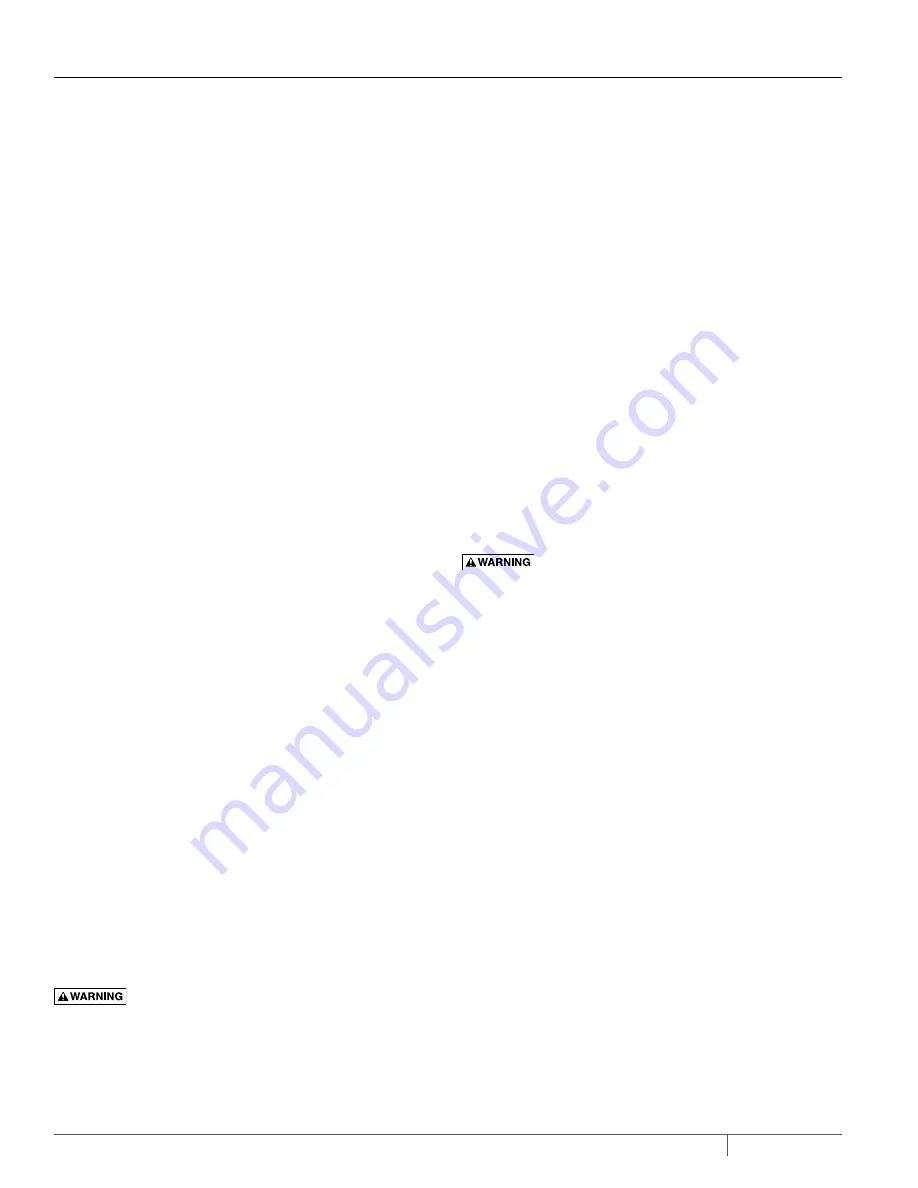
6
E-03-577 (01-23-20)
PUMP OPERATIONS STARTING SYSTEM
1. Double check all wire connections.
2. Turn pumps to Off position on H-O-A switches.
3. Turn on breakers.
4. When using single phase pumps, make sure red pump lead
is connected to capacitor circuit. Connect amprobe to pump
power cord and turn pump on. The pump will show high amp
draw momentarily, then as pump comes off start wirings, amps
will drop to normal nameplate amps.
5. When using three phase pumps (230/460/575), turn the
H-O-A switch to Hand position on one pump and notice
operation. If pump is noisy and vibrates, rotation is wrong.
To change rotation, interchange any two line leads to pump.
Do not interchange main incoming lines. Check rotation of
all pumps in this same manner.
6. Now set both H-O-A switches to Auto position and allow
water to rise in sump until one pump starts. Allow pump to
operate until the level drops to turn-off point.
7. Allow sump level to rise to start other pump(s). Notice run
lights in panel. Pumps should alternate on each successive
cycle of operation.
8. Turn both H-O-A switches to Off position and allow sump to
fill to the override control level(s).
9. Turn switches to Auto position, and pumps should start and
operate together until level drops to turn-off point.
10. Repeat this operation and cycle several times before
leaving the job.
11. Check voltage when pumps are operating and check the
amp draw of each pump. Check amps on each wire as
sometimes a high leg will exist. For excessive voltage on
one leg, the electric utility company should be consulted.
PUMP MAINTENANCE
As the motors are oil filled, no lubrication or other maintenance is
required.
If the heat sensor and seal failure are hooked up properly, no
attention is necessary as long as the seal failure indicator light
does not come on. To ensure continuity of the seal sensor leads,
a test light is provided on intrinsically safe Hydromatic panels as
standard equipment.
Pump should be checked every quarter for corrosion and wear.
Before handling these pumps and controls,always
disconnect the power first. Do not smoke, use flames or devices
that can produce electrical discharge or sparks in a septic
(gaseous) or possible septic sump.
FIELD SERVICE ON HYDROMATIC ORDINARY LOCATION PUMPS
Ordinary location submersible motors that are out of warranty
can be serviced in the field by any reliable motor service shop.
Any pump that is in warranty must be returned to the factory for
service or repaired at an authorized Pentair Hydromatic service
center. Charges will not be allowed if (in warranty) pump is not
taken to an authorized Pentair Hydromatic service center. When
field service is performed on a pump, these instructions should be
carefully followed.
FIELD SERVICE ON HYDROMATIC HAZARDOUS LOCATION PUMPS
Hydromatic hazardous location pumps must be returned to the
factory for electrical and motor service. Any repair not at an
authorized service center will void the Factory Mutual (FM) listing.
This will ensure the integrity of the hazardous location rating of
the pump and comply with our warranty requirements.
The quick disconnect cords, upper and lower seal, volute
and impeller components may be repaired or replaced by an
authorized Hydromatic service facility without compromising the
hazardous location rating to the pump.
Any time a seal is disturbed, it must be replaced.
Check the pump for proper rotation before returning to service.
ADJUST CUTTER CLEARANCE ON CHOPPER PUMP
Disconnect power before adjusting chopper
clearance; always keep fingers and hands away from chopper
parts.
1. First install the chopper plate (Item D) into the volute. It may
be helpful to install ½-20 studs into the chopper plate to line
up the holes with the corresponding volute holes. You may
have to tap the plate all the way down with a rubber hammer.
2. Remove the studs and replace with four ½-20 x 1 (Item A) in
long socket head screws from beneath the volute, do not
tighten.
3. Install motor with impeller mounted, tighten motor housing
bolts to the volute
4. Install the chopper retainer ring (Item B) and tighten the four
3/8 -16 x 1" long (Item C) socket head cap screws to force the
chopper plate up against the impeller and chopper blade
5. Next back off these 3/8-16 (Item C) bolts one quarter of a
turn. This should give you .015 clearances.
6. Tighten the outer four ½ -20 screws (Item A) to 75-85 Ft-lbs.
7. Measure the clearance with a feeler gage it should be
between .010 and .015.
8. Spin impeller with a hex wrench on the Impeller hub screw or
use a wooden pry bar to spin impeller to make sure there is no
rub.
9. If you hear or feel a rub readjust the clearance by loosening
the inner 3/8-16" screws evenly and tightening the ½- 20
screws.
PUMP OPERATIONS & MAINTENANCE
Содержание C4S(X)P Series
Страница 14: ...14 E 03 577 01 23 20 NOTES...
Страница 15: ...15 E 03 577 01 23 20 NOTES...