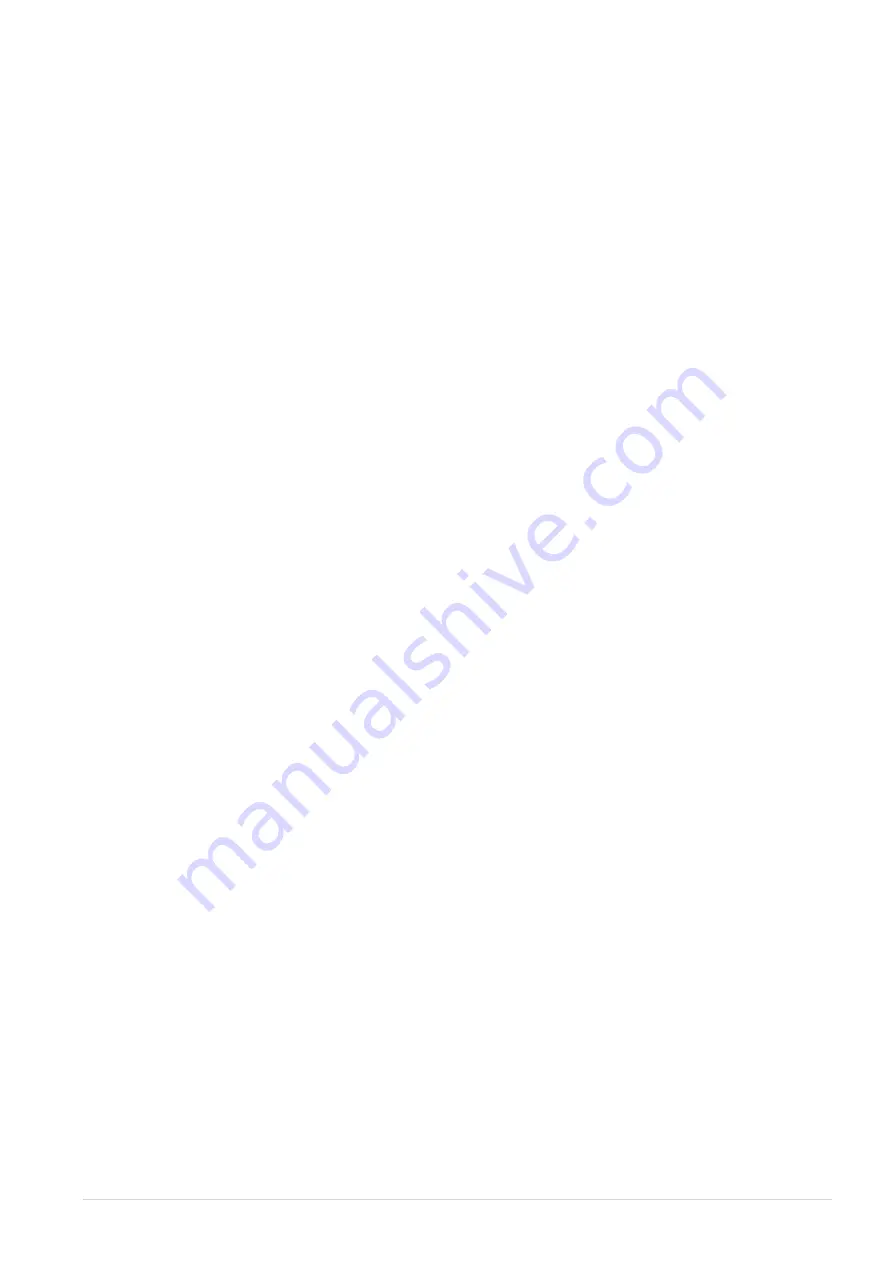
27 | P a g e
PATON
®
PSI PRO 315 A 400 V DC MIG/MAG TIG/MMA
5.5 FUNCTION OF BURNING OUT AT THE END OF WELDING
This function is intended for smooth filling of the crater, which is formed in the weld pool under the
influence of the electromagnetic deflection of the electric arc. The crater left at the end of the weld is a
very serious defect in the weld, which can cause the seam to burst or leak and is the source of
problems. The signal to the beginning of the function is to release the button on the handle at the end
of the welding process, while the movement should be stopped and welded with the falling voltage of
the dimples (this is the crater) in the weld. The time of voltage drop
[TIME DOWN VOLTAGE]
in the
welding source and the time of falling of the wire feed
[t.dn]
on the feeder correspond to the
smoothness of this process, these values must be the same for the unit to function properly. The default
value is set to 0.1s. This value can be changed at your own discretion, see section 6.1 for the order of
change.
5.6 FUNCTION OF POSTWELD GAS CLEANING
This function is intended to clean the shielding gas welding zone after the welding arc has expired. The
welded lake is exposed to the harmful effects of atmospheric air. By default, the purge time
[TIME
POST GAS]
is set to 1.5 seconds, this value can be changed at any time in its sole discretion.
5.7 WELDING AT PULSE WELDING VOLTAGE
This function is designed to simplify the control of a welding process in various spatial welding
positions, excluding a flat welding position. This function is also used in welding nonferrous metals.
When this function is activated, the application of pulse welding voltage improves mixing of molten
metals in the weld area and causes forced action on the transfer of molten metal drops into the welding
pool, therefore the stability of the weld formation and the stability of the welding process are
improved.
The pulse welding voltage in the manual arc welding process affects the weld parameters similar to the
movement of the operator hand in a manual arc welding process, specifically at hard-to-reach places.
The proper adjustment of the welding process parameters in the welding at pulse welding current has a
direct effect on the weld quality, specifically reduces weld metal porosity and decreases the graininess
of the weld metal. As a result of the improved weld quality, the weld strength increases.
To activate this function, it is necessary to set the following three operational parameters of the
welding process: voltage pulse amplitude
[POWER OF PULSE]
,
voltage pulse frequency
[FREQUENCY
OF PULSE]
,
and duty cycle
[DUTY CYCLE OF PULSE]
.
By default, the voltage pulse amplitude is 0
[OFF],
that is, the function is switched off, the voltage pulse frequency is 20 Hz, and the duty cycle is
50%. To activate the function, set the voltage pulse amplitude
[POWER OF PULSE]
higher than 0. The
voltage pulse amplitude should be set in percentage of the welding voltage specified for the welding
process.
Example
:
Welding is to be performed with electrode wire 0.8 mm in diameter. The set wire
feed velocity is 5.5 m/min. The set welding voltage is 18 V. The voltage pulse
amplitude
[POWER OF PULSE]
is 20%. The voltage pulse frequency
[FREQUENCY OF
PULSE]
is 20 Hz (default value). The duty cycle
[DUTY CYCLE OF PULSE]
is 50%
(default value).
The result is:
The following: the welding pulse voltage amplitude will be in the range of 14.4 …
21.6 V. the welding voltage pulse frequency will be 20 Hz, and the pulse length will
be equal to the length of an interval between pulses. If the
[DUTY CYCLE OF PULSE]
is not equal to 50%, the pulses will be nonsymmetrical relative to the intervals
between pulses, but the average welding value will be equal to the set welding
voltage of 18 V. As a result, the average heat input to the weld will not change.