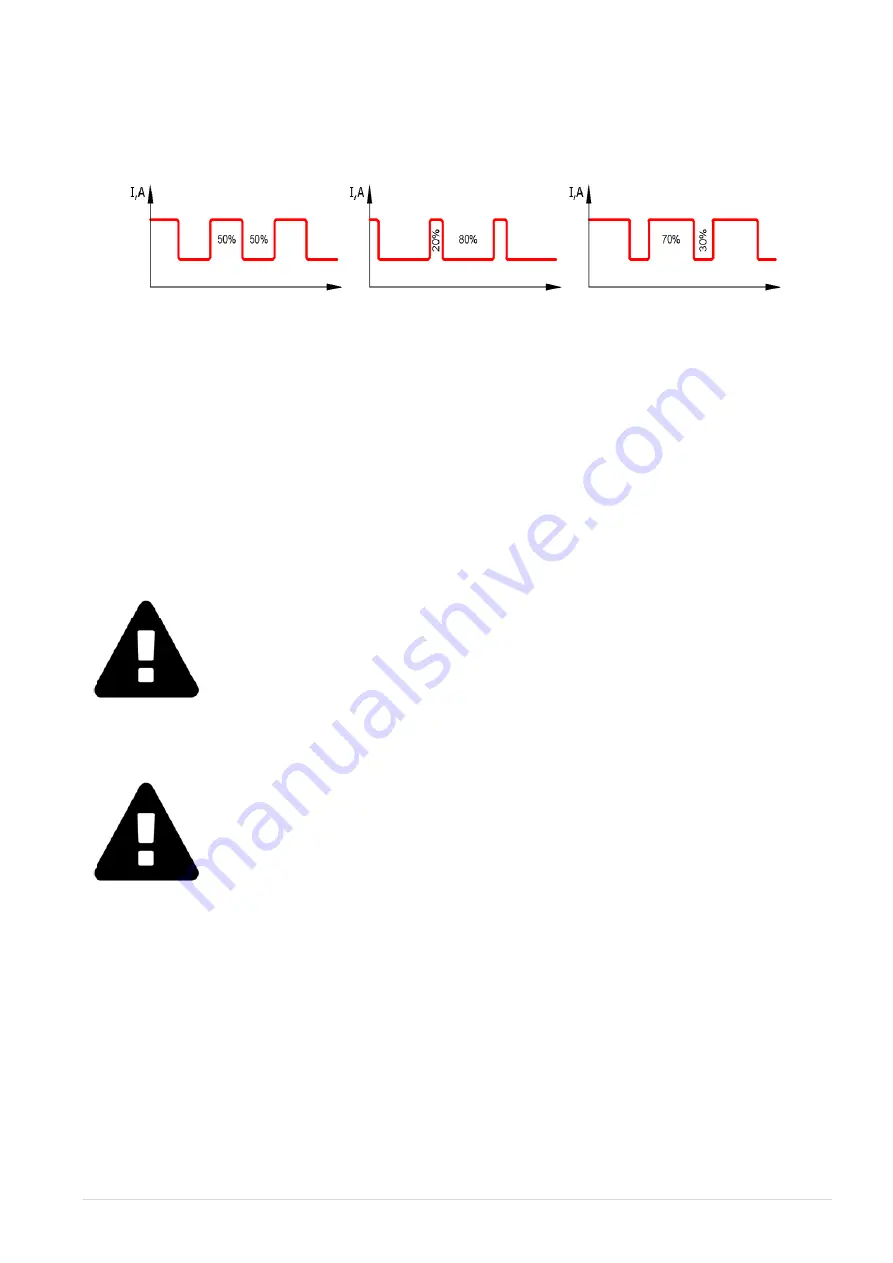
22 | P a g e
PATON
®
PSI PRO 315 A 400 V DC MIG/MAG TIG/MMA
Default
[DUTY CYCLE OF PULSE]
50%
[DUTY CYCLE OF PULSE]
20%
[DUTY CYCLE OF PULSE]
70%
If it is required to reduce heat input to the weld, as in welding thin parts, the welding current should be
decreased by performing the standard setting operations. In this case, current pulse parameters will be
adjusted automatically according to the set welding current, and the operator can control the reduction
of the heat input, as compared with the heat input at the initial welding current, by simultaneously
varying the current pulse amplitude and duty cycle.
The aforementioned parameters should be set differently for different welding processes, depending on
the requirements of the operator.
Operations required to set these parameters for the current welding process are described in Section 6.1.
5. SEMIAUTOMATIC ARC WELDING PROCESS (MIG/MAG)
ATTENTION!
As the shielding gas during welding of carbon steel, carbon
dioxide "CO2" is used, it is the cheapest option of protective gas, it is not
widely used due to the large amount of fumes and welding dust, as well as
spatter, the most common mix is used in the proportions "Ar" (82%) "CO2"
(18%). When welding aluminum, inert gases are used - argon "Ar", sometimes
more expensive helium "He". For stainless steel and high-alloy steels mixtures
with variable proportions of "75% Ar + 25% CO2" are commonly used. The
use of other gases only after consultation with the manufacturer of the device
ATTENTION!
As in the welding unit a standard KZ-2 euroconnector for a
welding torch is used, any welding torch can be purchased at the option of the
user
t, s
t, s
t, s