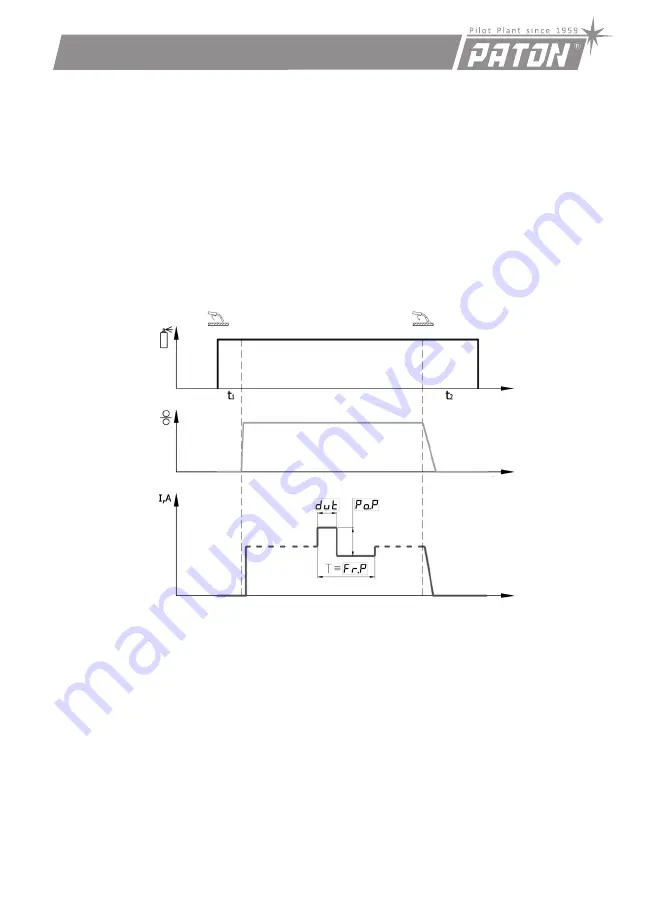
‐
17
‐
PATON
PRO-series
DC
MMA/TIG/MIG/MAG
to
save
gas.
Start
also
with
average
position
of
wire
feeding
speed
controller
on
the
feeding
machine
(~
6...8
m/min.)
and
average
source
voltage
(~19
V)
for
any
diameter
of
installed
wire
(Ф0.6...1.2
m).
This
configuration
may
be
not
optimum,
but,
under
condition
of
correct
work,
even
wire
feeding
(without
jerks)
and
correct
connection,
this
"source
+
feeding
machine"
combination
shall
be
able
to
weld
so
far.
For
better
results,
adjust
source
voltage
with
buttons
3
and
speed
of
wire
feeding
by
the
feeding
machine
according
to
general
recommendations
on
semiautomatic
welding.
Remember
that
these
parameters
are
different
for
each
specific
application.
5.1
WELDING
CYCLE
–
MIG/MAG
See
paragraph
6.1
for
sequence
of
changing
parameters
of
functions.
Time
of
pre
‐
purging
(
t
1
)
and
post
‐
purging
(
t
2
)
with
shielding
gas
is
set
on
the
wire
‐
feeding
machine.
5.2
FUNCTION
OF
VOLTAGE
FADE
‐
OUT
IN
THE
END
OF
WELDING
This
function
is
designed
for
smooth
filling
of
a
crater,
which
is
formed
in
the
weld
pool
by
the
action
of
electromagnetic
draft
of
the
electric
arc
and
subsequently
becomes
a
source
of
weld
defects.
Release
of
the
torch
button
in
the
end
of
welding
becomes
the
signal
to
start
the
function.
Once
this
happens,
stop
moving
the
torch
and
weld
the
pothole
(which
is
a
crater)
in
the
weld
with
fading
‐
out
voltage.
Smoothness
of
this
process
can
be
controlled
through
voltage
fade
‐
out
time
[t.dn]
both
in
the
source
and
in
the
wire
feeding
speed
control
unit.
These
values
must
be
t,
s
t,
s
t,
s
Содержание PRO-160
Страница 1: ......