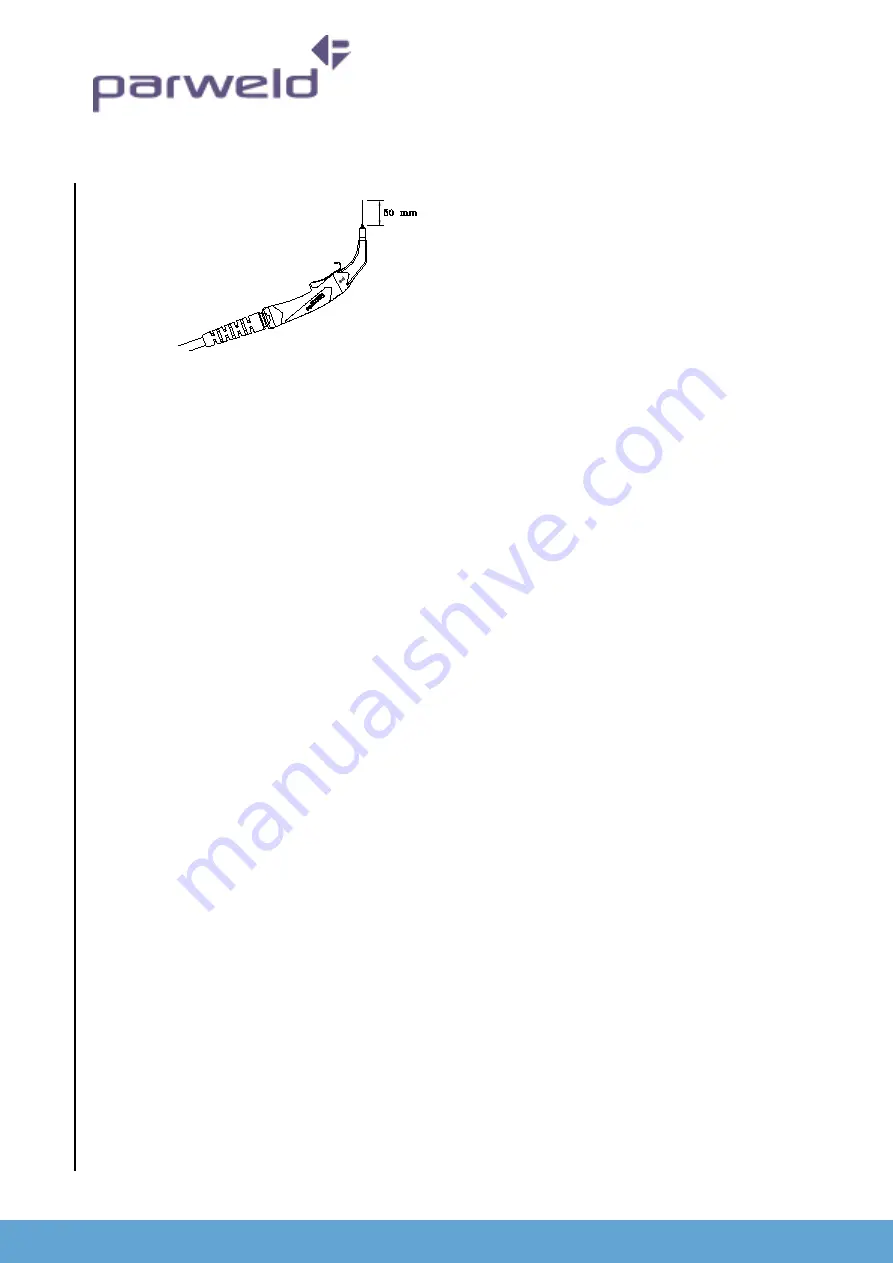
www.parweld.com
8
feeding,
x
5.7 torch installation
Your Parweld MIG/MAG Welding Torch has been supplied ready to
weld. It has been supplied with the standard consumables denoted
in the product brochure.
To connect the torch to the power source:-
1. Remove the tip adaptor and contact tip
2. Inch the wire from the exit of the wire guide on the feed unit
as Figure 1. Ensure that it does not short out on any machine
panels.
3. Carefully slide the electrode wire into the torch liner and
slowly locate the torch gun plug body into the feed unit central
connector and tighten the gun plug nut as Figure 2
note; to aid the initial location of a new torch and to prevent
damage to the gas nipple O-ring a very light application of
grease to the O Ring is beneficial.
4. Keeping the torch as straight as possible, use the power source
inch facility or torch trigger to feed the electrode wire 50mm
from the end of the liner conduit.
5.
Once the electrode wire has stopped, refit the tip adaptor,
diffuser, contact tip and gas nozzle.
6. Trim the electrode wire to within 5mm of the face of the nozzle,
this will facilitate jolt free arc initiation.
7.
Press the gas purge button and check the gas flow is adequate
for your application.
8.
An inexpensive flow meter is available from Parweld reference
806001.
9. If you are setting a water-cooled torch ensure you have the
recommended water flow rate.
Note;- It is essential to ensure adequate flow of clean, cool
water to prevent irreparable torch failure, a minimum of 1.2 l/
min is recommended.
Parweld recommend the use of its XTS water recirculation system
designed specifically for use with all water cooled MIG, TIG and
Plasma welding torches.
The Parweld XTS recirculation equipment can be fitted with a fail-
safe flow protection device to prevent overheating or meltdown.
Note. Water flows into the torch through the blue hose. The blue
hose delivers cold water directly to the prime source of heat, the
swan neck and consumable. The re circulated water is then passed
through the torch power cable to cool the power cable as it is
returned to the cooler through the red water return lead.
Ensure all air is removed from the water cooling circuit before
welding.
5.8 Work return lead connection
Insert the work return lead connector into the receptacle on the front
panel of the machine and twist it clockwise until tightly secured.
Connect the earth clamp to the work piece as close as possible to
the point to be welded and ensure that a good electrical connection
is created to bare metal.
5.9 Shielding gas connection
1. Using the gas hose supplied connect the hose to the gas inlet
connection on the rear of the machine and tighten it with a
spanner.
2. Connect the opposite end of the gas hose to the output
connection of a gas regulator capable of supplying the correct
gas flow for the welding operation.
Note if the gas cylinder is to be stored on the back of the
machine ensure it is secured using the retention chain provided
6.0 Operation
1. Switch on the machine using the mains on/off switch.
2. Select the welding mode using push button (8) and switching
option with Button (9)
6.1 MIG welding Feeding wire electrode
You can MIG weld in 2 modes Manual and Synergic the manual
mode takes more skill to setup.
Synergic MIG,
Select the Synergic MIG mode using button (10)
Select the wire size using button (14)
Select the gas type using button (12)
Rotating the amperage button (5) select the desired welding
amperage. you can refer to the table at the rear of the instruction
book for recommended welding amperages. The machine will
adjust the welding voltage automatically but you may trim it and the
inductance to your personal preference by adjustment of the Voltage
knob (7) and inductance (13) The voltage will increase or decrease
penetration and the inductance affects the arc stability and droplet
transfer.
Manual MIG
Select the Manual MIG mode using button (8)
Содержание XTM254i
Страница 1: ...Operator Manual ISSUE 2 XTM254i...