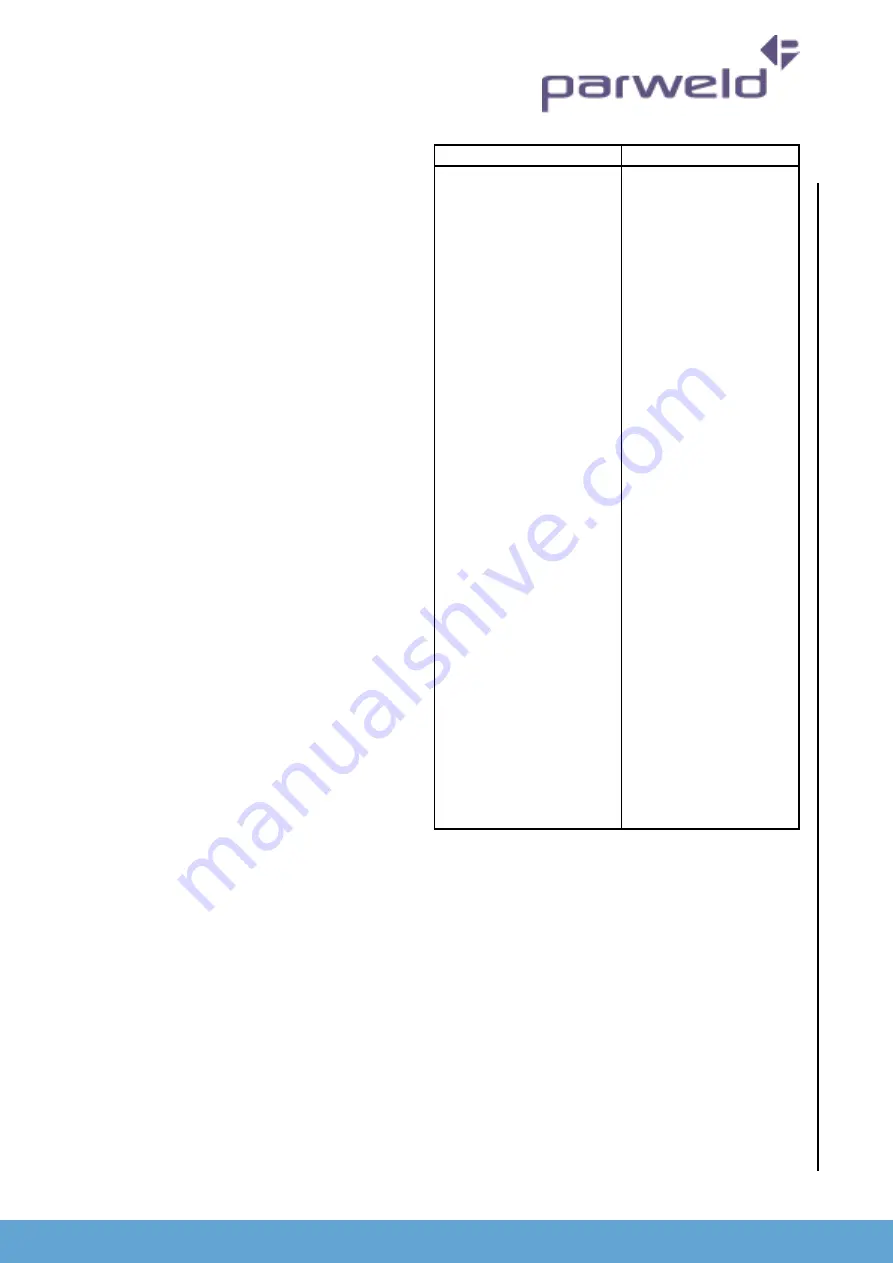
www.parweld.com
www.parweld.com
11
problem
Cause/Corrective action
Porosity - small cavities or holes
Resulting from gas pockets in
weld metal.
Inadequate shielding gas
coverage. Check for proper
gas flow rate.
Remove spatter from gun
nozzle.
Check gas hoses for leaks.
Eliminate drafts near welding
arc.
Place nozzle 6-13 mm from
work piece Hold gun near
bead at end of weld until
molten metal solidifies.
Wrong gas. Use welding
grade shielding gas; change to
different gas.
Dirty welding wire. Use clean,
dry welding wire. Eliminate
pickup of oil or lubricant on
welding wire from feeder or
liner.
Work piece dirty. Remove all
grease, oil, moisture, rust,
paint, coatings, and dirt from
work surface before welding.
Use a more highly deoxidizing
welding wire (contact supplier).
Welding wire extends too far
out of nozzle.
Be sure welding wire extends
not more than 13 mm beyond
nozzle.
Stainless steel
318l-16 high corrosion resistance. Ideal for dairy work, etc. On
stainless steels.
TIG Welding guide
Using the selector button (8) toggle through the functions until the
MMA light is illuminated
You can adjust he welding amperage using the knob (5)
Tig welding cable connection
Connect the TIG torch to the - terminal and the work lead to the +
terminal for direct current straight polarity. Direct current straight
polarity is the most widely used polarity for DC TIG welding. It allows
limited wear of the electrode since 70% of the heat is concentrated
at the work piece. Connect the gas hose on the TIG torch to the gas
outlet on the gas regulator.
Torch starting in SCRATCH-TIG mode
Ensure the gas supply is switched on and gas is flowing from the
front of the torch nozzle. Briefly contact the tip of the tungsten
electrode down onto the work piece with the torch at around 70
0
from
vertical, lift the torch up from the work piece to draw out an arc. To
prevent melting of the end of the tungsten so this in a smooth rapid
movement
7.0 Fault Finding
Содержание XTM254i
Страница 1: ...Operator Manual ISSUE 2 XTM254i...