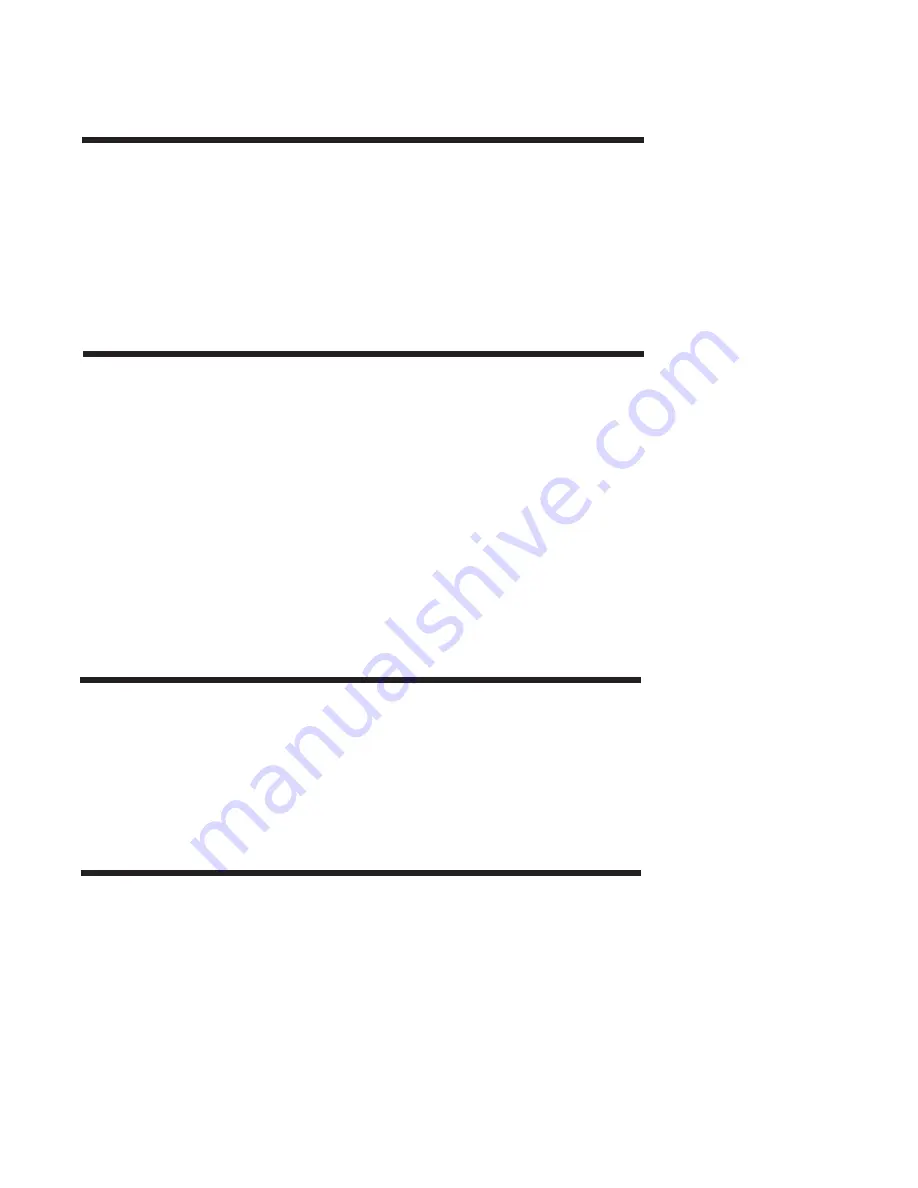
P
AGE
41
On-Off Control 4.4
On-Off control can be implemented with SPST relay or SSR driver output(s) . On-Off
operation can be assigned to either or both Output 1 and 2. A hysteresis adjustment is
provided for On-Off Outputs. This adjustment is in terms of degrees/engineering units and
defines the bandwidth of the hysteresis. The hysteresis value straddles the setpoint. Relay
chatter can be eliminated by proper adjustment of this parameter. When operating in On-Off
control, the output(s) will turn on or off depending upon the setpoint, the process value, Tune
mode selections, and the hysteresis adjustment.
Time Proportioning Control 4.5
Time Proportioning control can be implemented with a SPST relay or SSR driver. Time
Proportioning control can be selected for either Output 1 and/or Output 2, depending on
hardware configuration. Time Proportioning control is accomplished by cycling the output on
and off during a prescribed period of time when the process variable is within the
proportional band.
Ex: Calculated output % = 40%; Cycle time adjustment = 20 seconds
Output on time = .4 x 20 = 8 seconds
Output off time = .6 x 20 = 12 seconds
When the unit is operating in the Control mode, the control algorithm determines the output %
required to correct for any difference between the process value and the
setpoint. The output calculation is affected by Tune mode parameter adjustments.
See Figure 4-1 (page 42) for proportional bandwidth effect on the output.
Current Proportioning Control 4.6
Current Proportioning control can be implemented on units provided with mADC current
output(s). Current Proportioning control provides a 4 to 20mADC or 0 to 20mADC output in
response to process value and setpoint. As with Time proportioning, the calculated output %
for Current proportioning control is affected by the Tune mode parameter adjustments.
See Figure 4-1 (page 42) for proportional bandwidth effect on the output.
Position Proportioning Control 4.7
Position Proportioning Control can be implemented on those units provided with two SPST
relay or two SSR driver outputs and the Position Proportioning (slidewire feedback) option.
Position Proportioning control permits the use of PID control when the final control element is
a modulating device such as a motorized valve. Two outputs are required to control the
valve. One output opens the valve, the second output closes the valve. The slidewire
feedback is used to indicate the valve position to the instrument. The valve position will be
dependent upon the process value, the setpoint and Tune mode
parameters. (Continued on next page)