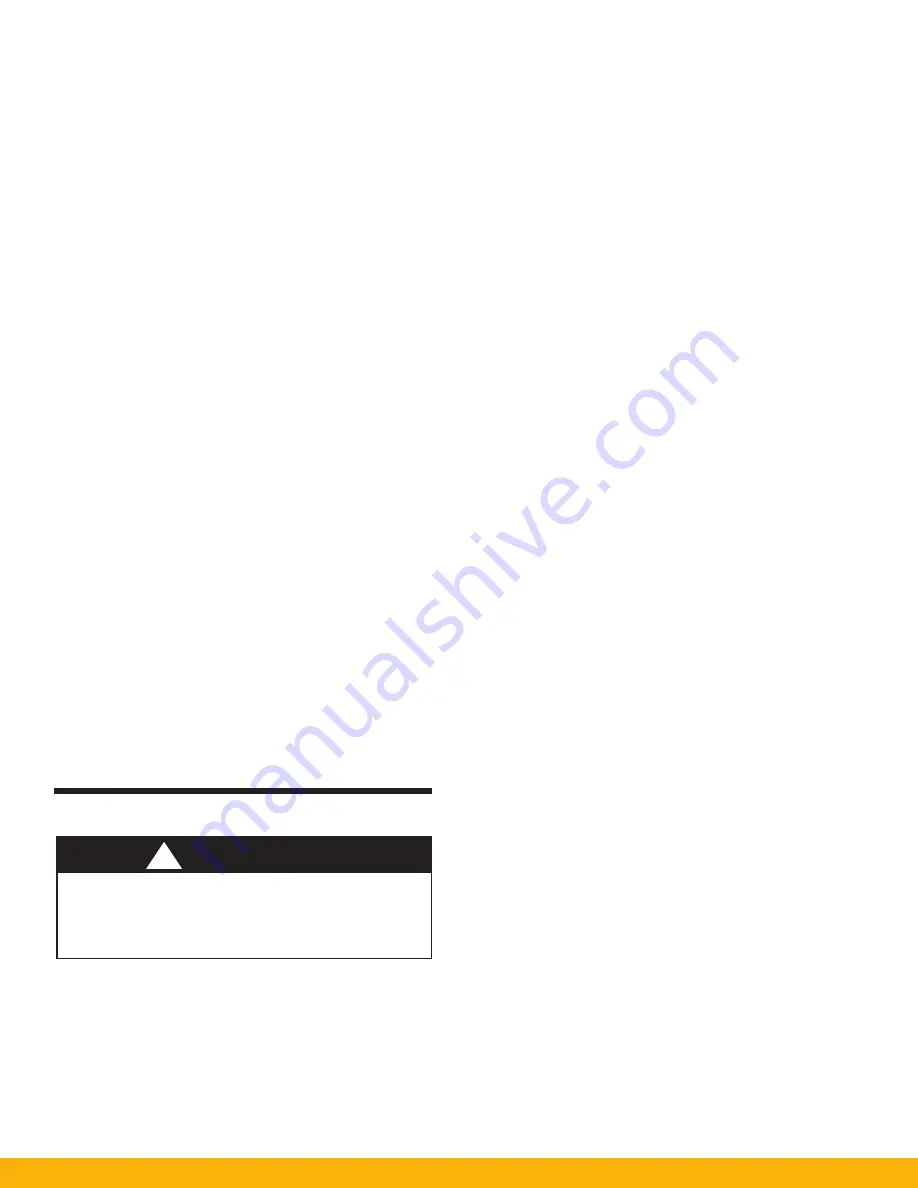
12
4.1.11 In-Place Cleaning
The spray nozzles to the wash headers can become clogged
or otherwise obstructed due to debris within the field piping.
At initial start-up, water should be purged before final pipe
connection at the PSG. The Y strainer to the detergent injector
tee assembly should also be checked for debris. A wash cycle
should be initiated before placing the PSG on line, refer to the
In-Place Cleaning Owner’s Manual for the start up operational
procedure.
4.1.12 Placing PSG Online
Depending upon job specifications or other requirements, the
PSG may be placed on line by a customer-supplied switch,
or a time clock, or through a building maintenance system
(BMS), refer to unit Electrical Drawings. Upon PSG start-up,
the system blower is placed on line and the power packs are
placed on line after a 45 second delay. The indicator light on
each power pack enclosure should be illuminated. The power
pack enclosure toggle switch should be checked if the indica-
tor light is not illuminated. If the indicator light is not illuminated
after checking the toggle switch or the indicator light is flashing.
Refer to Section 10 Troubleshooting. The unit Main Electrical
Panel has a 40 second time delay at start-up for the power
pack circuit. This represents a standard precaution since PSG
operates in applications where combustible gases could be
present in process enclosures or process duct at start-up. The
time delay of 40 seconds purges the duct before activating
the power pack circuit to assure safe operation. For operation
of auxiliary system equipment, refer manufacturer’s owner’s
instructions for proper operating procedures.
4.1.13 Parker On Site Start Up
The PSG system may include on site start up by a Parker
Field Service Technician. Usually this is listed on the order
acknowledgment. As installation nears completion, allow at
least two weeks for scheduling a Field Service Technician.
Contact Parker Customer Service for a start-up request form.
The completion of the request form is required before
scheduling a Parker Field Service Technician. The on site start
up consist of a complete mechanical and electrical inspection
including the operation of all supplied Parker equipment. A
Parker Field Service Technician is available for on site service
at a daily rate plus travel and expenses.
5. Maintenance and Manual Cleaning
The PSG unit should be inspected frequently and
collected contaminant removed from the system
regularly to prevent excessive accumulation which
may result in a flashover or risk of fire.
5.1.1 Check Power Pack Enclosure Indicator Lights
The PSG should be monitored daily by observing that the indicator
light is illuminated to each power pack enclosure or by the remote
status panel or remote beacon or BMS. Occasional arcing (flashing
of an indicator light) is normal. An established arcing condition or
dead short condition (continuous flashing of an indicator light) or the
indicator light is not illuminated is not normal should be corrected.
Refer to Section 10 Troubleshooting.
5.1.2 Unicell(s) Weekly Visual Inspection
A visual inspection of a few modules could identify problems such
as moderate to extreme contaminant build up to the unicells even
though the indicator lights are illuminated. This will be helpful
in scheduling a manual cleaning of the components, refer to
Section 6 and 7. To check the condition of the unicells, place the
PSG off line. Open the module door and perform the grounding
procedure, refer to Figures 12 and 13, inspect the condition of
the unicells, filters, door feed-thru insulators and interior of the
cabinet. Experience will dictate whether contaminant build-up is
excessive. Contaminant build up will decrease high voltage to
the ionizer and collector cell circuits and also system efficiency.
When accessing a module, always clean the two door feed-thru
insulators. Inspect the ionizer section of each unicell, noting the
condition of the contact spring (distorted?, bent? missing?), ionizer
weld nut (missing?), ionizer standoff insulators (contaminant build
up) and ionizer wires (contaminant build up?, missing?), repair
or replace. Ionizer wires should be taut and centered between
ground plates. Ground plates between each ionizer wire should be
straight and parallel. Unicell module support tracks should be free
of contaminant build-up for ground contact.
Inspect the collector cell section of each unicell, noting the
condition of the contact spring (distorted? bent? missing?) cell
contact screw (missing?), cell plates (bent? warped?) should be
parallel and straight, repair or replace. Cell hot plates (smaller
dimensional plates) should be centered between ground plates
(larger dimensional plate). Cell plates should not have contaminant
bridging between the cell plates or at support structure corners or
the triangular insulators Unicell module support tracks should be
free of contaminant build-up for ground contacts.
5.1.3 Filters, Drain Sumps, and Access Door Gasket
Inspection
Inspect filters, noting the condition (contaminant build up? media
separation? bent frames?) should not have contaminant build up
restricting airflow, repair or replace.
Module drain sumps should not have moderate to extreme
contaminant build up or an accumulation of wash water if
equipped with In Place Cleaning, clean module sumps as required.
Component access doors gaskets should be in-place and in good
condition.
5.1 Recommended Maintenance
Once the system is operational, periodic maintenance is
necessary to assure proper performance. Follow a regular
pattern of system observation and log abnormal conditions.
Since systems reflect the process under control, maintenance
patterns will vary accordingly.
!
CAUTION