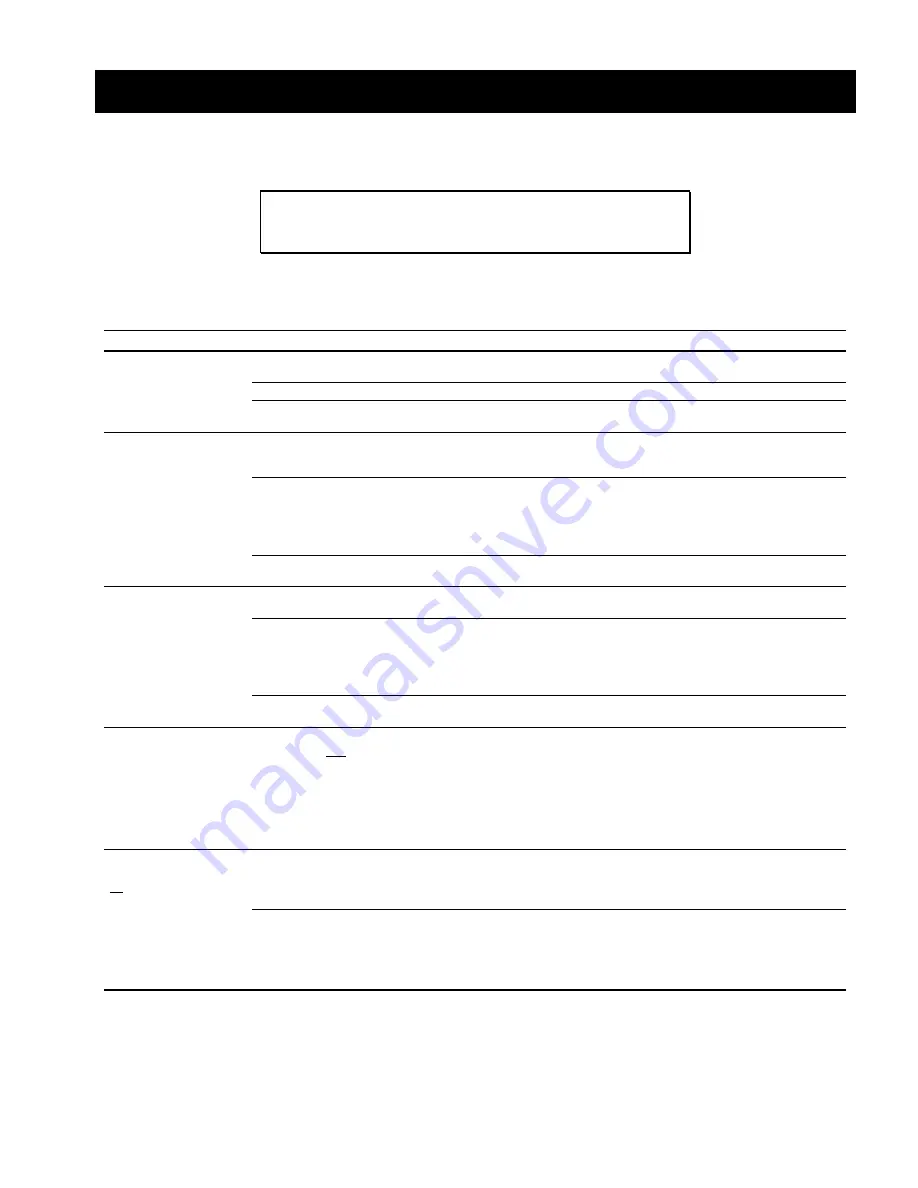
Chapter 2. Troubleshooting
35
6ROXWLRQV
#
WR
#
&RPPRQ
#
3UREOHPV
NOTE
Some software-related causes are provided because it is sometimes
difficult to identify a problem as either hardware or software related.
Problem
Cause
Solution
Communication
(Ethernet) errors.
1. Ethernet card not installed
correctly.
1. Refer to the user instructions that came with your Ethernet card.
2. Ethernet or IP address conflict.
2. Refer to the configuration instructions in the Programmer’s Guide.
3. Connection to Ethernet port is
compromised or miswired.
3. Check the connections according to page 24.
Communication (serial)
not operative, or receive
garbled characters.
1. Improper interface connections or
communication protocol.
1. Check the connections according to page 24.
NOTE: Refer also to
the diagnostic
procedures on page
38.
2. COM port disabled.
2.a. Enable serial communication with the
E1
command.
2.b. If using RS-485, make sure the internal jumpers are set
accordingly (see page 5). Make sure COM 2 port is enabled for
sending 6K language commands (execute the
PORT2
and
DRPCHKØ
commands).
3. In daisy chain, unit may not be set
to proper address.
3. Verify proper application of the
ADDR
command.
Direction is reversed.
(stepper axes only)
1. Direction connections to the drive
are reversed.
1. Switch DIR+ with DIR- connection to drive (see page 15).
2. Phase of step motor reversed
(motor does not move in the
commanded direction).
2. Switch A+ with A- connection from drive to motor.
SOFTWARE ALTERNATIVE: If the motor (and the encoder if one
is used) is reversed, use the
CMDDIR1
command to reverse the
polarity of both the commanded direction and the polarity of the
encoder counts).
3. Phase of encoder reversed
(reported
TPE
direction is reversed).
3. Swap the A+ and A– connection at the ENCODER connector.
Direction is reversed,
servo condition is stable.
(servo axes only)
1. Command output (CMD)
connections and feedback device
connections or mounting are
reversed.
1. Software remedy: Issue the
CMDDIR1
command to the affected
axis. This reverses the polarity of the commanded direction and the
feedback direction so that servo stability is maintained.
Hardware remedy: Switch CMD- with the CMD+ connection to drive
or valve (if your drive or valve does not accept differential outputs
this will not work). You will also have to change the feedback device
wiring or mounting so that it counts in same direction as the
commanded direction.
Direction is reversed,
servo condition is
unstable.
(servo axes only)
1. Not tuned properly.
1. Refer to tuning instructions on page 51.
2. Phase of encoder reversed or
mounting of ANI input is such that it
counts in the opposite direction as the
commanded direction.
2. Software remedy for encoder feedback only: For the affected
axis, issue
ENCPOL1
.
Hardware remedy: If using encoder feedback, swap the A+ and A-
connections to the 6K product. If using ANI feedback, change the
mounting so that the counting direction is reversed.