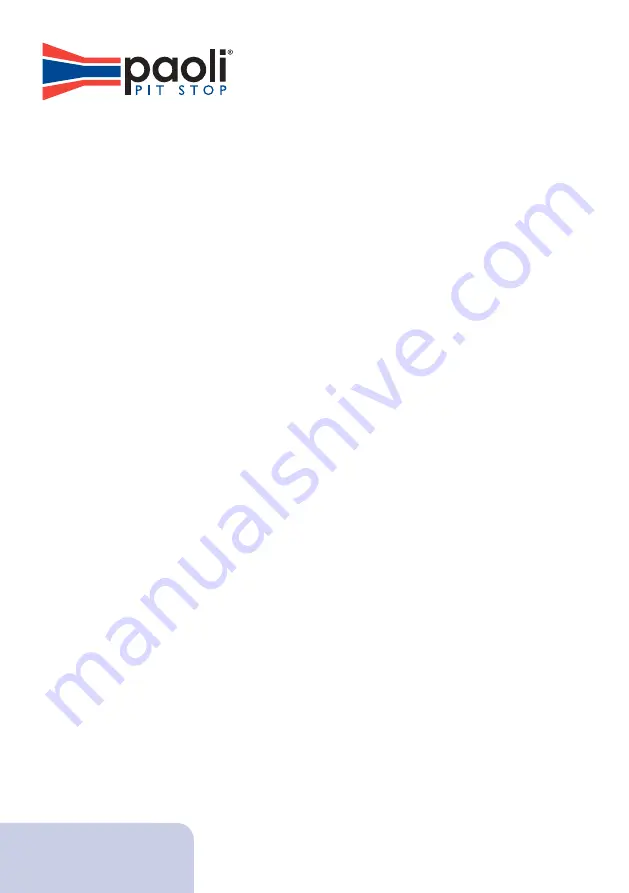
ENGLISH
6
INSTALLATION OF ACCESSORIES
Before changing an accessory, always make
sure that the air supply line is depressurized (no
air pressure), and only after disconnecting the
wheel gun and replace it. Use only accessories
suitable for the job (view our catalogue for
accessories).
Use only impact sockets with a hole for the
locking pin.
Do not use chrome sockets or for manual use.
Do not use square drive adapters (reductions
or multiplies).
Always check that the locking pin of the socket
is present and secured firmly. To install the
wheel nut socket, proceed as follows:
L
Mark each clutch cover with the wheel gun’s
serial number.
L
Remove the four clutch cover (hammer
case) screws, discard lock washers.
L
Holding the 1” square drive, remove the
anvil shank, clutch cover bearing and clutch
cover from gun. Clutch spring should
remain with clutch shaft, clutch plate and
clutch housing. Retain the anvil shank,
clutch cover bearing and clutch cover as an
assembled unit.
L
Using an appropriately sized aluminum
block, support the 1” square drive from
the bottom. This will provide the base
for pressing the socket onto the square
drive. Make sure the block is tall enough
to allow clearance for the clutch cover.
L
In ideal situations, an aluminum block
should be machined to fit either the I.D.
or the surface of the socket. This will be
used for pressing the socket onto the
square drive. Special attention must be
taken to assure the inner O-ring groove
(retention ring) is not damaged by a tool
used on the socket I.D.. A tool used
on the magnet surface (i.e. for wheel
nut sockets with magnets) should also
fit properly to prevent damage to the
magnets. In certain situations a thick
block of aluminum can be used to press
directly on the teeth of the socket (i.e.
for wheel nut sockets with fingers) for
installation. This is not a recommended
practice and should only be used when
a proper press tool cannot readily be
made.
L
Before the use, always perform a dynamic
adjustment of the supply air pressure (
view
figure Fig.5
). Adjust the supply air pressure
on the low pressure gauge turning the
adjusting screw of the air pressure regulator
while keeping the trigger pressed.
L
Do not exceed the maximum supply air
pressure of 20 bar (with wheel gun running).
REGULATION OF
THE AIR PRESSURE
L
Slide the rotation reverse shaft (
see
figure Fig.1-I
) and push the trigger (
view
figure Fig.1-C
). See the figure
Fig.4
to
identify the rotation direction of the
square drive.
L
Avoid accidental starting, being careful not
to unwittingly act on the trigger (
view figure
Fig1-C
).
HANDLING
OPERATING AND MAINTENANCE MANUAL
Содержание DP 197 SFE
Страница 55: ...ATTACHMENTS TECHNICAL CHARTS 55...
Страница 56: ...ATTACHMENTS TECHNICAL CHARTS 56...
Страница 58: ...ATTACHMENTS TECHNICAL CHARTS 58 Fig 4 CLOCKWISE ANTICLOCKWISE...
Страница 63: ......