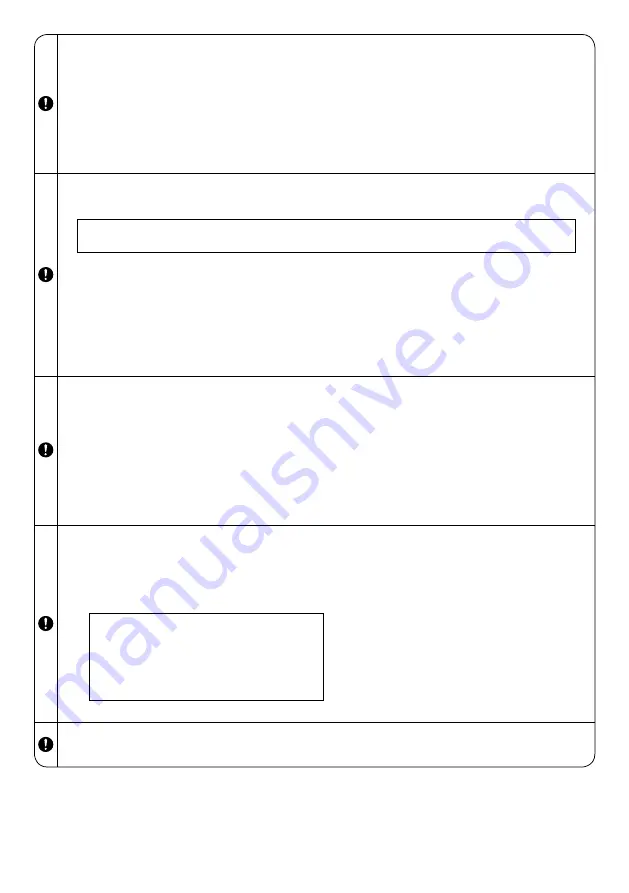
5
7. The following leak detection methods are deemed acceptable for all refrigerant systems.
• No leaks shall be detected when using detection equipment with a sensitivity of 5 grams per year of refrigerant or better under a pressure of at
least 0,25 times the maximum allowable pressure (>0.98MPa, max 3.90MPa). For example, a universal sniffer.
• Electronic leak detectors may be used to detect fl ammable refrigerants, but the sensitivity may not be adequate, or may need re-calibration.
(Detection equipment shall be calibrated in a refrigerant-free area.)
• Ensure that the detector is not a potential source of ignition and is suitable for the refrigerant used.
• Leak detection equipment shall be set at a percentage of the LFL of the refrigerant and shall be calibrated to the refrigerant employed and the
appropriate percentage of gas (25 % maximum) is confi rmed.
• Leak detection fl uids are also suitable for use with most refrigerants, for example, bubble method and fl uorescent method agents. The use of
detergents containing chlorine shall be avoided as the chlorine may react with the refrigerant and corrode the copper pipe-work.
• If a leak is suspected, all ignition sources shall be removed/extinguished.
• If a leakage of refrigerant is found which requires brazing, all of the refrigerant shall be recovered from the system.
The precautions in #8 must be followed to remove the refrigerant.
8. Removal and evacuation
• When breaking into the refrigerant circuit to make repairs – or for any other purpose – conventional procedures shall be used.
However, it is important that best practice is followed since fl ammability is a consideration.
The following procedure shall be adhered to:
• remove refrigerant -> • purge the circuit with inert gas -> • evacuate -> • purge with inert gas -> • open the circuit by cutting.
Brazing must not be used.
• The refrigerant charge shall be recovered into the correct recovery cylinders.
• The system shall be purged with OFN to render the appliances safe. (remark: OFN = oxygen free nitrogen, type of inert gas)
• This process may need to be repeated several times.
• Compressed air or oxygen shall not be used for this task.
• Purging shall be achieved by breaking the vacuum in the system with OFN and continuing to fi ll until the working pressure is achieved, then
venting to atmosphere, and fi nally pulling down to a vacuum.
• This process shall be repeated until no refrigerant is within the system. (Until the concentration of purge gas is 0.25 LFL or less by the leak
detector).
0.25LFL = 0.525Vol%
• When the fi nal OFN charge is used, the system shall be vented down to atmospheric pressure to enable work to take place.
• This operation is absolutely vital if brazing operations on the pipe work are to take place.
• Ensure that the outlet for the vacuum pump is not close to any potential ignition sources and there is ventilation available.
9. Charging procedures
• In addition to conventional charging procedures, the following requirements shall be followed.
- Ensure that contamination of different refrigerants does not occur when using charging equipment.
- Hoses or lines shall be as short as possible to minimize the amount of refrigerant contained in them.
- Cylinders shall be kept in an appropriate position according to the instructions.
- Ensure that the refrigerating system is earthed prior to charging the system with refrigerant.
- Label the system when charging is complete (if not already).
- Extreme care shall be taken not to over fi ll the refrigerating system.
• Prior to recharging the system it shall be pressure tested with OFN (refer to #8).
• The system shall be leak tested on completion of charging but prior to commissioning.
• A follow up leak test shall be carried out prior to leaving the site.
• Electrostatic charge may accumulate and create a hazardous condition when charging and discharging the refrigerant.
To avoid fi re or explosion, dissipate static electricity during transfer by grounding and bonding containers and equipment before charging/discharging.
10. Decommissioning
• Before carrying out this procedure, it is essential that the technician is completely familiar with the equipment and all its details.
• It is recommended good practice that all refrigerants are recovered safely.
• Re-use of recovered refrigerant is prohibited.
• It is essential that electrical power is available before the task is commenced.
a) Become familiar with the equipment and its operation.
b) Isolate system electrically.
c) Before attempting the procedure ensure that:
d) Make sure that cylinder is situated on the scales before recovery
takes place.
e) Start the recovery machine and operate in accordance with
instructions.
f) Do not over fi ll cylinders. (No more than 80 % volume liquid
charge).
g) Do not exceed the maximum working pressure of the cylinder,
even temporarily.
h) When the cylinders have been fi lled correctly and the process
completed, make sure that the cylinders and the equipment
are removed from site promptly and all isolation valves on the
equipment are closed off.
• mechanical handling equipment is available, if required,
for handling refrigerant cylinders;
• all personal protective equipment and leak detectors are
available and being used correctly;
• the recovery process is supervised at all times by a
competent person;
• recovery equipment and cylinders conform to the
appropriate standards.
• Electrostatic charge may accumulate and create a hazardous condition when charging or discharging the refrigerant.
To avoid fi re or explosion, dissipate static electricity during transfer by grounding and bonding containers and equipment before charging/discharging.
11. Labelling
• Equipment shall be labelled stating that it has been de-commissioned and emptied of refrigerant.
• The label shall be dated and signed.
• Ensure that there are labels on the equipment stating the equipment contains fl ammable refrigerant.