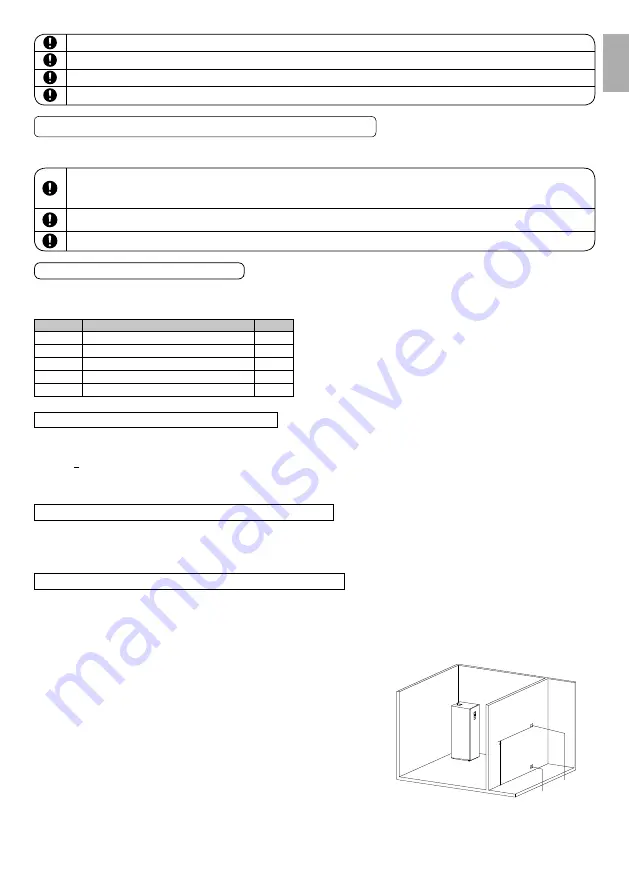
3
ENGLISH
Ensure the correct polarity is maintained throughout all wiring. Otherwise, it will cause electrical shock or fi re.
After installation, check the water leakage condition in connection area during test run. If leakage occurs, it will cause damage to other properties.
If the Tank Unit not operates for long time, the water inside the Tank Unit should be drained.
Installation work.
It may need three or more people to carry out the installation work. The weight of Tank Unit might cause injury if carried by one person.
PRECAUTION FOR USING R32 REFRIGERANT
•
The basic installation work procedures are the same as conventional refrigerant (R410A, R22) models.
However, pay careful attention to the following points:
When connecting fl are at indoor side, make sure that the fl are connection is used only once, if torqued up and released, the fl are must be remade. Once the fl are connection
was torqued up correctly and leak test was made, thoroughly clean and dry the surface to remove oil, dirt and grease by following instructions of silicone sealant. Apply
neutral cure (Alkoxy type) & ammonia-free silicone sealant that is non-corrosive to copper & brass to the external of the fl ared connection to prevent the ingress of moisture
on both the gas & liquid sides. (Moisture may cause freezing and premature failure of the connection)
The appliance shall be stored, installed and operated in a well ventilated room with comply to Indoor Floor Area Requirement and without any continuously operating
ignition source. Keep away from open fl ames, any operating gas appliances or any operating electric heater. Else, it may explode and cause injury or death.
Refer to “PRECAUTION FOR USING R32 REFRIGERANT” in outdoor unit installation manual for other precautions that need to pay attention to.
INDOOR FLOOR AREA REQUIREMENT
•
If the total refrigerant charge in the system is <1.84 k
g
, no additional minimum fl oor area is required.
•
If the total refrigerant charge in the system is
≥
1.84 k
g
, additional minimum fl oor area requirements is complied as described below:
Symbol
Description
Unit
m
c
Total refrigerant charge in system
k
g
m
max
Maximum refrigerant charge allowed
k
g
m
excess
m
c
- m
max
k
g
H
Installation height
m
VA
min
Minimum ventilation opening area
cm
2
A) Determine
Maximum refrigerant charge allowed,
m
max
1. Calculate Installation Room Area,
A
room
.
2. Based on Table I, select
m
max
which corresponds to the calculated
A
room
value.
3. If
m
max
>
m
c
, the unit can be installed in the installation room with
the specifi ed installation height (
H
=600mm) in Table I and without additional room area or any additional ventilation.
4. Else, proceed to B) and C).
B) Determine
Total Floor Area of
A
room
and
B
room
compliance to
A
min total
1. Calculate the
B
room
area adjacent to the
A
room
.
2. Determine the
A
min total
based on the Total Refrigerant Charge,
m
c
from Table II.
3. The total fl oor area of both
A
room
and
B
room
must exceed
A
min total
.
C) Determine
Minimum Venting Opening Area
,
VA
min
for natural ventilation
1. From Table III, calculate
m
excess
.
2. Then determine
VA
min
corresponding to the calculated
m
excess
for natural ventilation between
A
room
and
B
room
.
3. The unit can be installed at specifi c room only when the following conditions are fulfi lled:
•
Two permanent openings, one at bottom, another at top, for ventilation purposes are made between
A
room
and
B
room
.
•
Bottom opening:
- Must comply to the minimum area requirement of
VA
min
.
- Opening must be located 300mm from the fl oor.
- At least 50% of required opening area must be 200mm from the
fl oor.
- The bottom of the opening shall not be higher than the point of
release when the unit is installed and must be situated 100mm
above the fl oor.
- Must be as close as possible to the fl oor and lower than
H.
•
Top opening:
- The total size of the Top opening must be more than
50% of
VA
min
.
- Opening must be located 1500mm above the fl oor.
•
The height of the openings must more than 20mm.
•
A direct ventilation opening to outside is
NOT
encouraged for ventilation opening (the user can block the opening when it is cold).
•
The value of
H is considered as 0.6m to comply to IEC 60335-2-40:2018 Clause GG2.
Total refrigerant charge in system,
m
c
(k
g
)
= Pre-charged refrigerant amount in unit (k
g
)
+ Additional refrigerant amount after installation (k
g
)
Adjacent
Room
(
B
room
)
Installation
Room
(
A
room
)
>0.5
VA
min
>
VA
min
>1500mm
Содержание WH-UD03JE5
Страница 36: ...Printed in the Czech Republic ACXF60 37631 AB ...