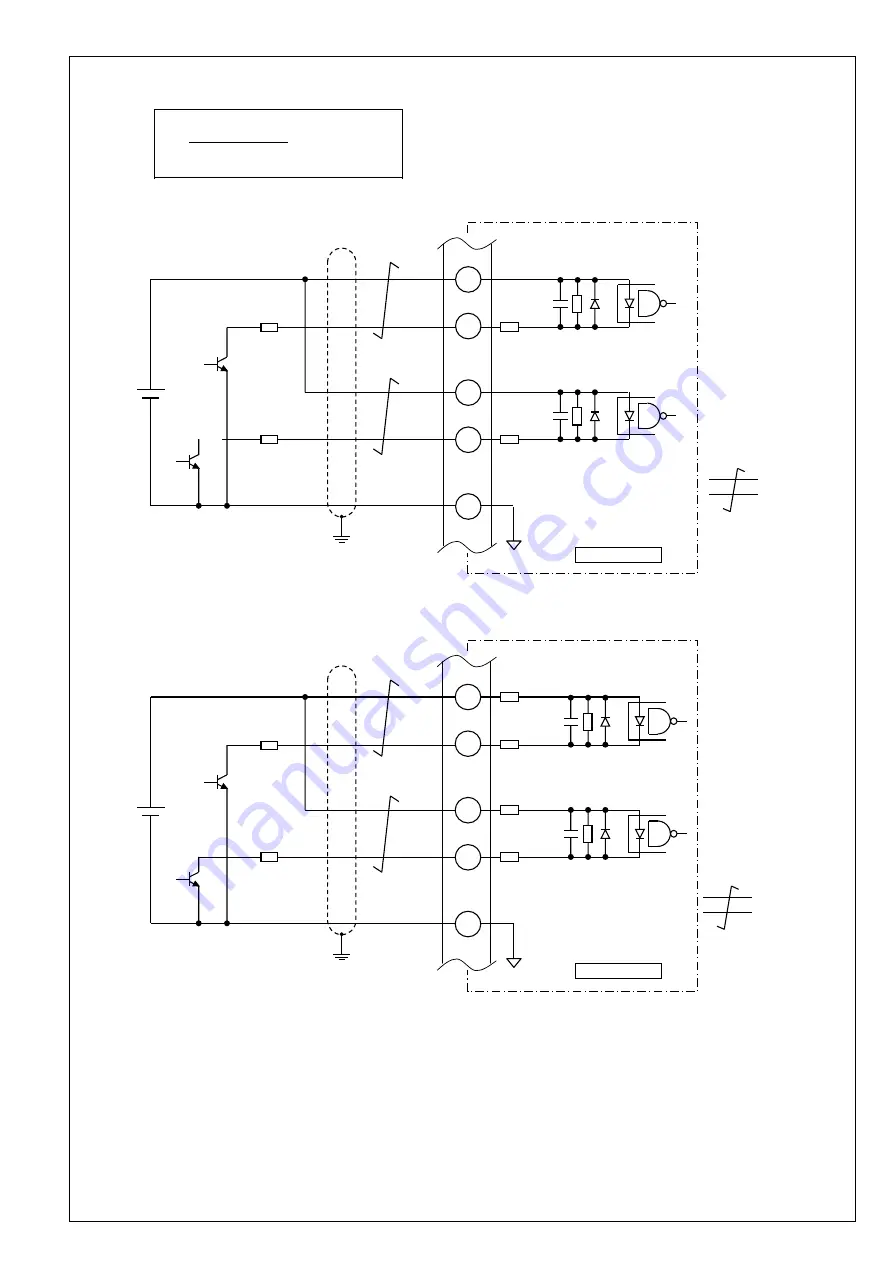
No. SX-DSV03167 - 23 -
R6.0 Motion Control Business Unit, Panasonic Industry Co., Ltd.
Open collector interface
Note: Precautions for using the command pulse input as an open collector interface
Shorten the wire length (up to 1 m).
Be aware that the maximum pulse frequency of the open collector interface is small (200 kpps)
compared with that (500 kpps) of the line driver interface.
R
R
V
DC
2.2 k
Ω
220
Ω
220
Ω
2.2 k
Ω
R
R
24 V
DC
2.2 k
Ω
220
Ω
220
Ω
2.2 k
Ω
Twisted pair
Twisted pair
2.2 k
Ω
2.2 k
Ω
OPC1
PULS2
OPC2
SIGN2
GND
PULS1
PULS2
SIGN1
SIGN2
GND
X4
X4
A1
A4
A2
A6
B10
A3
A4
A5
A6
B10
Servo driver
Servo driver
1000 pF
1000 pF
1000 pF
1000 pF
V
DC
-
1.5
R+220
= 10 mA