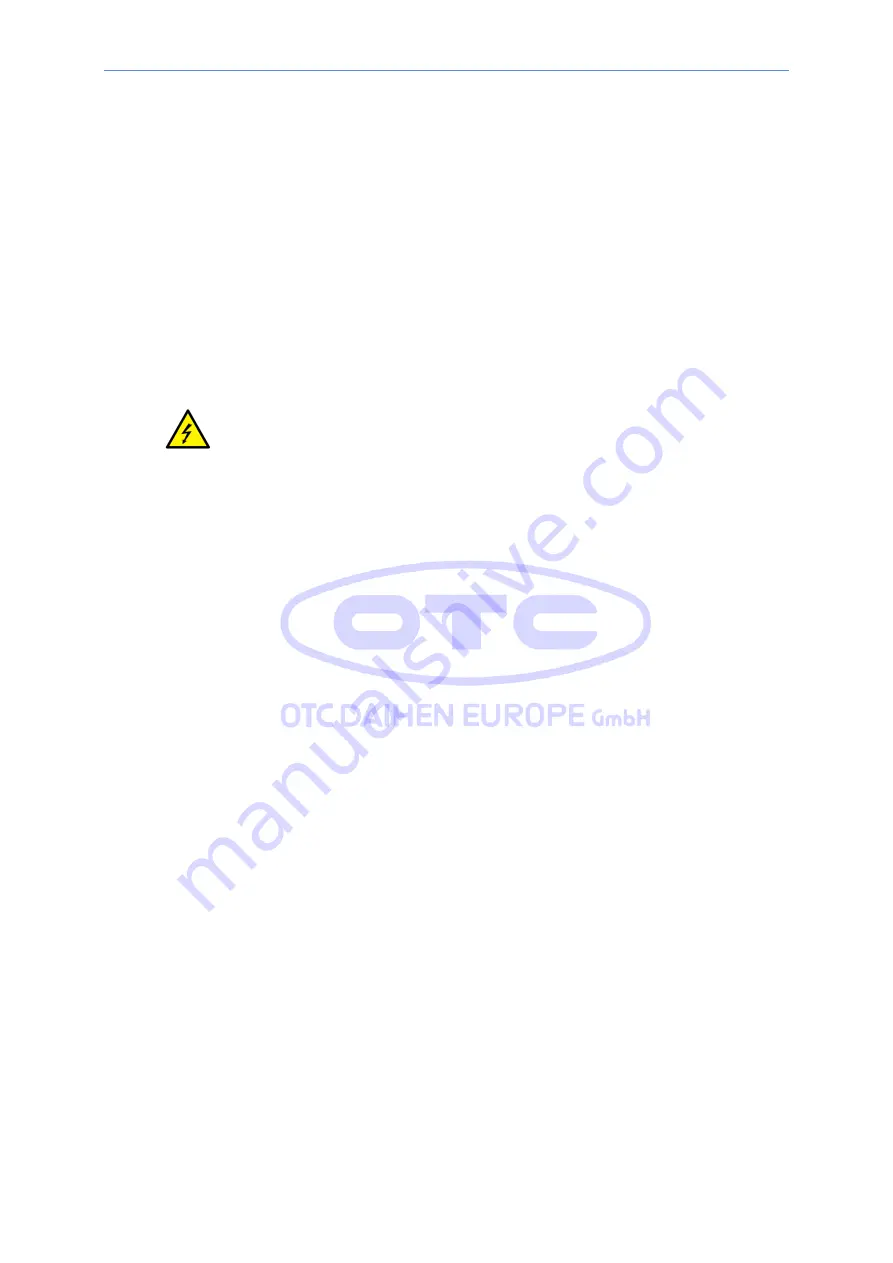
Regulations for the prevention of accidents
6
DTX-2200-3000 AC/DC
3
Regulations for the prevention of accidents
The use of welding equipment and welding itself are always associated with a certain safety risk. Therefore each
set up and operation of the device assumes that the instruction manual is understood and complied. The properly
used welding machine grants a high degree of operational security but can, in case of improper handling, lead to
property and personal damage.
Be sure that you observe the following safety rules:
3.1
Connection of the power source
The installation and maintenance of the system must be carried out in accordance with the general
safety and accident prevention regulations of the legislature.
The state of the power cord and plug must be checked and any damage eliminated. The
electrical equipment must be tested at regular intervals. Use cables of sufficient diameter.
The ground cable must be fastened as close as possible to the work area of the work piece be. Is it
connected directly to the building design or too far away from the work area, this can lead to energy
loss or discharging.
The system may not be used in damp areas and in no case encounter water or other liquids.
Direct contact with hands or with wet clothing to components that might be under tension is to be
avoided. Make sure that your gloves and protective clothing are dry.
When working in damp rooms or on metal surfaces, use protective gloves and work shoes with
rubber
soles.
The system has to be cut off at each interruption, even at sudden loss of power. Accidental ground
contact can lead to overheating of the system and cause a fire. The system must therefore never
be turned on without supervision.
Содержание DTX-202 TIG
Страница 1: ...DTX 2200 AC DC DTX 3000 AC DC User Manual ...
Страница 69: ...Wiring diagram DTX 2200AC DC 69 DTX 2200 3000 AC DC ...
Страница 70: ...Wiring diagram DTX 2200 AC DC 70 DTX 2200 3000 AC DC ...
Страница 71: ...Wiring diagram DTX 3000 AC DC 71 DTX 2200 3000 AC DC ...
Страница 72: ...Wiring diagram DTX 3000 AC DC 72 DTX 2200 3000 AC DC ...