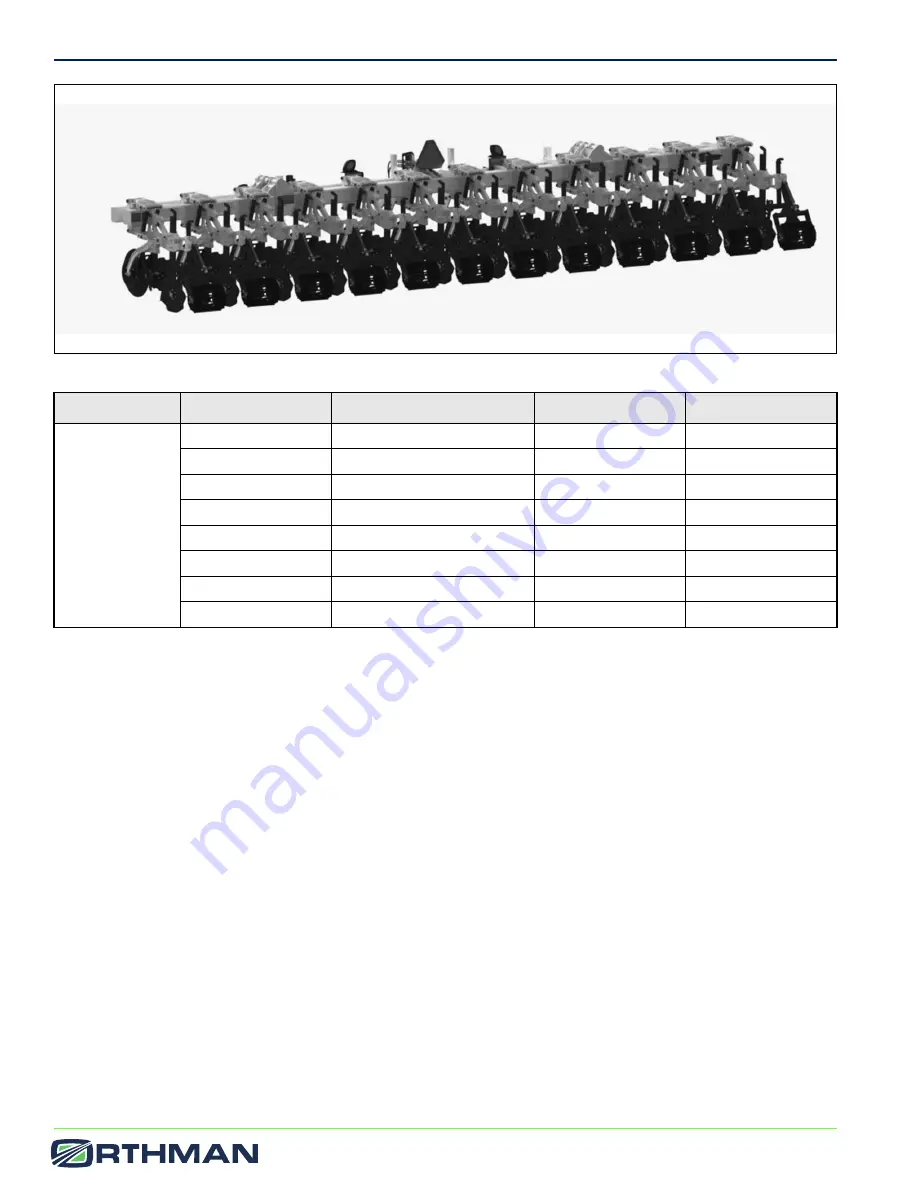
MAINTENANCE AND SPECIFICATIONS
1TRIPR II Row Units OM-EN
7-6
ORM000263
Figure 7-2: Folding Machine (12 rows)
Number of Rows
Row Spacing
Weight
Transport Width
Mounted
Folding
Machines
8
30 in (76.2 cm)
6790 lb (3080 kg)
11.7 ft (3.9 m)
8
36 in (91.4 cm)
7072 lb (3208 kg)
13.8 ft (4.6 m)
8
38–40 in (96.5–101.6 cm)
7164 lb (3250 kg)
14.7 ft (4.9 m)
12
30 in (76.2 cm)
9660 lb (4382 kg)
16.7 ft (5.6 m)
12
36 in (91.4 cm)
9883 lb (4483 kg)
19.3 ft (6.4 m)
12
38–40 in (96.5–101.6 cm)
10155 lb (4606 kg)
21.3 ft (7.1 m)
16
30 in (76.2 cm)
12368 lb (5610 kg)
21.7 ft (7.2 m)
16
38–40 in (96.5–101.6 cm)
15764 lb (7150 kg)
28.1 ft (9.4 m)
Содержание 125-082-01-EN-OM
Страница 1: ...Operator s Manual 1TRIPR II ROW UNITS Part 125 082 01 EN OM Rev A ...
Страница 2: ...Intentionally Left Blank Page ...
Страница 6: ...1TRIPR II Row Units OM EN TOC iv Page Intentionally Blank ...
Страница 22: ...SAFETY INFORMATION 1TRIPR II Row Units OM EN 2 12 Page Intentionally Blank ...
Страница 28: ...MAJOR COMPONENTS 1TRIPR II Row Units OM EN 3 6 Page Intentionally Blank ...
Страница 70: ...OPERATION AND FIELD SETTINGS 1TRIPR II Row Units OM EN 5 24 Page Intentionally Blank ...
Страница 74: ...TROUBLESHOOTING 1TRIPR II Row Units OM EN 6 4 Page Intentionally Blank ...
Страница 82: ...MAINTENANCE AND SPECIFICATIONS 1TRIPR II Row Units OM EN 7 8 Notes ...