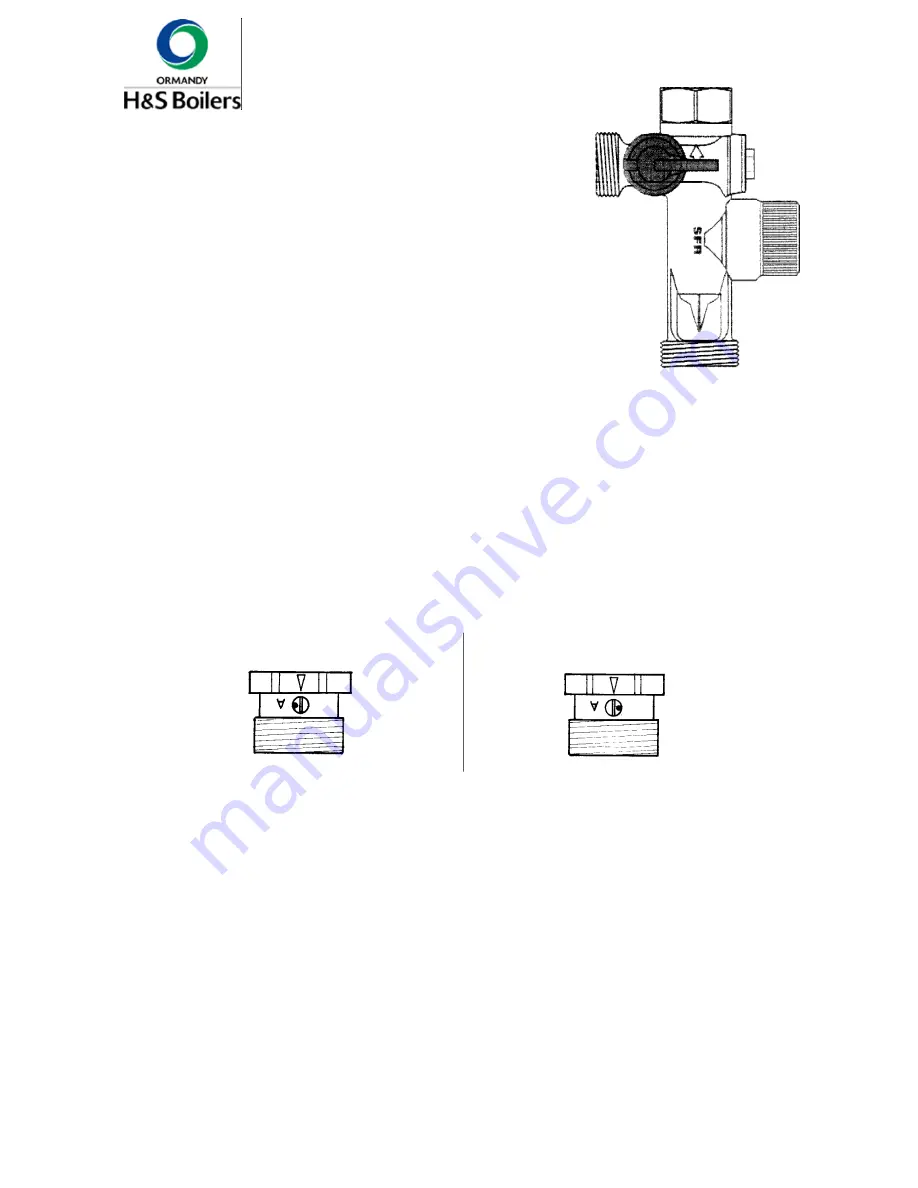
Page
11 / 19
It is prohibited, under threat of warranty cancellation, to position any
device which might cut the direct communication between the safety
group and the tank. The safety device will be placed on the tank cold
water feeding duct, outside the water jacket, at a max. distance from
the tank of 1 meter.
B
C
A
Cold water
(input)
Cold water (outlet)
A) Locking valve
B) Safety valve
C) Draining opening
Drainage vs. sewerage
The safety group discharge will be connected to an evacuation pipe
having a diameter at least equal to the equipment connection pipe
by means of a funnel allowing an air rate of 20 mm min.
Filling of the installation
It is important to take into account that:
-
after every tank heating, a water draining by the C ori-
fice should occur. This event can be avoided by using a
domestic water expansion pot.
-
to avoid the formation of limestone (safety group enemy)
which might deposit on the valve seat, it is required to
manually operate the safety group valve once a month, by
completing a manual discharge.
Open position to the filling
(free flow of water in both directions)
Automatic position(active valve)
Non-returnvalve
- Open the anti-thermosiphon valves (inactive/free passage).
Before filling the installation, adjust the nitrogen pressure of the expansion vessel according to the height of the installation.
You become the value of this nitrogen pressure (P
vessel
[bar]) by dividing the head of water of the installation by 10 and adding
a safety margin of 0,2 to 0,5.
Ex. : for an installation height of 6 m : P
vessel
= (6/10 + 0,3) = 0,9 bar.
When all the accessories are in place (expansion tank, security valve, manometer, ...) and that the airtightness of the
hydraulic circuits is ensured, apply the following sequence for the filling of the hot sanitary water circuit :
Z
Z
- The filling must take place slowly, the drain cocks being open or unscrewed in order to avoid to the maximum the blocking
of air.
- Verify the functioning of the automatic drain cock placed on the reheating hydraulic circuit of the tank and control the
airtightness of the connections.
- After a first filling and a first drain, the pressure to read to the manometer will be equal to the static pressure (or static
height actual of the installation) raised of 0,1 to 0,5 kg/cm² according to the cases.
- The first heating must take place at the highest possible temperature (80-90°C) and be maintained during several hours
in order to degas at maximum and the most rapidly possible.
- During this phase of heating at high temperature, the air and the released gases must be regularly evacuated by the
separation devices and of air purging.
- After a last purging, you must read the pressure to the manometer like the temperature and stop the installation (circulation
pump included); let cool up to a temperature of approximately 50°C.
- The pressure to read to the manometer average of 50°C after degasification is approximately equal to the pressure of
inflation of the vessel, raised of 0,2 to 0,5 bar. Thus the pressure with which the installation will push on the diaphragm
of the vessel will be such, that this diaphragm as this diaphragm is slightly bent and that later on no point of the installation
can never be put in depression. In the example here above, the filling pressure in cold water of the installation will have
then to be adjusted to approximately: P
FILLING
=0,9 + 0,3 = 1,2 bar.
- The filling of water in the boiler must be complete.
- Control the airtightness of all the connections and close the anti-thermosiphon valves (active).